Investments in innovation, people, technology must go on, even as market realities set in
Downturn could push advancements such as closed-loop automated drilling and configurable drill floors to the forefront
By Linda Hsieh, Managing Editor, and Alex Endress, Editorial Coordinator
Clay Williams is Chairman, President and CEO of National Oilwell Varco (NOV).

From your perspective, what are the most critical challenges facing the upstream oil and gas industry in the midst of the market slowdown?
These challenges are twofold. The first challenge is continuing to reduce our cost of operations. The second challenge is operational. This is an industry that requires experience and concentration to operate efficiently and safely, and I think the challenge for our leadership is to make sure that our teams aren’t distracted by the downsizing and the downturn.
Our leaders must help workers understand that they are part of a great industry that has seen downturns before. We are going to move through this one and be fine on the other side of it. The work that they do is critical, and we need to make sure leadership across the industry understands the stress that our teams are under.
As drilling contractors delay or cut back on equipment maintenance due to the drop in rig activity, what potential impacts do you foresee on equipment reliability and downtime?
There’s always a cost when you cut corners on maintenance. While we understand that a lot of drilling contractors are under an immense amount of stress, the companies that cut back the most will potentially face much bigger challenges with regards to maintaining uptime and efficiency. The other challenge that some drilling contractors will have is revitalizing idled equipment that is called upon to go back to work.
Drilling contractors are looking at all opportunities to reduce their cash outflow. Many, especially onshore, are cannibalizing equipment as they look across the board to reduce expenditure wherever they can. If a piece of equipment wears out, some contractors will go and remove that off an idled rig rather than order something new. This industry is pretty good at reducing expenditures quickly in a downturn like this, but there’s a limit to how far that can go. There’s going to be a cost to getting these machines back up and running again once drilling contractors have been called upon to go back to work.
Further, the costs associated with going back to work are not just with equipment but also with crews and training. It’s important that drilling contractors continue to invest in and maintain their equipment, as well as maintain their core capabilities – their core crews that have the most experience in drilling operations.
My main concern is making sure that we don’t lose the core capabilities of the industry. We’re already facing a lot of workforce challenges with the Big Crew Change, and this downturn may be accelerating that process. This industry requires a high level of attention and focus on safety. I really hope that we’re able to keep the people in the industry focused on the right thing to make sure they’re executing safely.
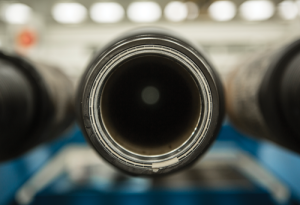
What can companies to do to maintain workforce competency through these challenging economic times?
NOV is promoting stable workforce competency amidst the downturn by continuing efforts with the NOV Technical College, an initiative we launched in 2007 to train our industry’s experts. These colleges train workers to repair and maintain a lot of the new and high-tech equipment that’s going into the industry. Along the way, we’ve opened colleges in Houston, Singapore, the UK, South Africa, South Korea, Brazil and other markets that we serve.
NOV sends new-hires into the program for either six months, nine months or 12 months to prepare them to go out and take care of our equipment. Since the downturn, we’ve started an extension to the program where technicians are brought back to the colleges after they’ve worked in the field. This helps to lift their overall level of training and to develop new skill sets.
This downturn has already lasted longer and has become more severe than some predicted. Do you believe the industry is in a bust similar to the 1980s?
First, this is a cyclical industry, and it always cycles down from time to time. While this is a very severe downturn, I don’t think it will ultimately be as severe as the 1980s because there are some key differences. One is that OPEC was holding 10 million barrels a day off of the worldwide market as we entered 1986, which was about 16% of global demand. That was partly caused by the fact that global demand actually fell in the early 1980s due to the recession and a lot of initiatives around conservation. The supply and demand picture was much more out of balance than it is today, wherein we have very little excess capacity – less than 2% of global demand and maybe even less than 1%.
The other key distinction is that more of the global supply is coming from lower-quality reservoirs like unconventional shales that decline at a faster rate than conventional reservoirs. Once the slowdown in activity translates to declining supply, we should see a steeper decline curve.
In this industry, you have to be optimistic. I think the fundamentals point to a recovery, but I can’t tell you exactly when it will come. Nevertheless, we certainly have significant challenges ahead of us.
What lessons can be learned from previous downturns that can be put to use in this downturn?
First, I think all of us in the industry share the view that we have to reduce cost and respond to the market realities that we’re in. Beyond that, we need to continue to invest in technology and improve the efficiency of our operations. If you look back at the history of this industry, necessity has always been the mother of invention. A lot of great advancements came out of downturns. Reduced margins really underscored the requirement to try new technologies and improve operations. The result is we all got better. I think downturns are the places where the industry gets better technically.
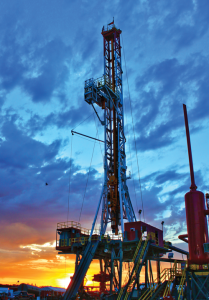
For our organization, it means that we want to invest in new technology and new products. We have seen lot of interest in these technologies despite the downturn. In fact, we see more interest for some of the things that we’re doing than we saw a couple of years ago when oil was trading north of $100 a barrel. When commodity prices are very high, it’s all about execution – making sure that the rig gets the well drilled. When you move into a market like this, with a lower commodity price and more economic pressure, oil companies realize they have to do things differently. They become a little more creative and a little more expansive in their thinking.
For instance, we’ve received a lot more interest in closed-loop automated drilling – something we’re pioneering at NOV. It’s used in conjunction with our NOVOS control system, where sensors are placed at the bottom of the hole that utilize our IntelliServ wired drill pipe to transmit data on a microsecond basis to the rig, and we let software control the operations of the surface equipment.
What we find is the software can see more accurately what’s happening downhole and make microsecond adjustments based on that. This results in drilling the well at a much faster rate. The oil companies that are drilling with NOVOS see closed-loop automated drilling as an opportunity to learn to drill a particular stratigraphic column faster and more efficiently.
More and more we’re seeing that oil and gas companies are looking to this closed-loop technology to speed up the learning curve in some of the shales that are being developed to make those drilling operations more efficient.
Will the changes that result from this downturn be sustainable in the long term?
As long as we continue to work with our customers to advance these changes, I think it’s possible. Both onshore and offshore, the industry is learning the potential of standardization and the industrialization of the drilling process. Over the past decade, the industry has migrated toward standardization of operations and of rig equipment. That has brought about many benefits. In the area of training, for instance, rig crews see basically the same rig layout while traveling from rig to rig, and they can learn from other crews how to perform more efficient operations on the standardized layouts. By applying more fit-for-purpose assets and more modern industrial techniques, I think those sorts of improvements are likely to be permanent.
When do you see the newbuild market coming back, and what will contractors focus on when the next build cycle begins?
It will be a while before drillers get back to building. In the short term, there’s still interest in specialized rigs for the harsh-environment offshore, such as 20,000-psi rigs. Longer term, we’re more focused on introducing the next generation of offshore drilling assets that will include things like configurable drill floors, which will provide a way to bring all the different types of tools that may be required to work at a well center in and out of the drilling operation on an as-needed basis.
NOV is also using big data to help with preventive maintenance and remote monitoring of equipment to reduce downtime. I think industry interest in that will increase.
For onshore specifically, I think we still have a long way to go in terms of bringing high levels of automation that were pioneered offshore. We’re likely to continue to see evolution amongst the land fleet in terms of automation. Since 2014, we’ve been working on our land rig of the future, which incorporates higher levels of automation and brings together technologies such as big data and closed-loop drilling.
Likewise, we’ve been working on our drillship of the future with a configurable drill floor and, with semisubmersibles, we’re looking at new ways of construction to reduce costs. These are all part of a 10-year strategy we launched in 2014 across our business units.
The main thing for NOV is to continue to be innovative. We recognize we’re in a downturn, and there’s a lot of pressure to reduce costs, but we also need to continue to invest for the future and the eventual recovery of the industry. We will be there when the industry does come back to upgrading its equipment and ordering new rigs again.
Five or 10 years from now, how do you envision rigs and equipment will be different from the way they are today?
There will definitely be higher levels of automation. As we evolve to more pad drilling onshore, I think land rigs will likely undergo another round of fit-for-purpose evolution. There will be a lot more data monitoring, predictive maintenance and more flexible configurations.
How is equipment changing to provide better well control?
We’re specifically focused on advancing our retrievable pod for subsea BOPs, with new pipe-centering technology, as well as ram designs that can cut thicker and heavier pipe. We’re looking at more data monitoring of BOP operations. There’s a lot of focus on improving BOP reliability and effectiveness.
You’ve mentioned big data a couple of times. What opportunities do you see for NOV to support better data management at the wellsite?
There are quite a few challenges in regards to bandwidth and transmitting data off of rigs. There are a lot of data collected on rigs that aren’t necessarily transmitted elsewhere for analysis. I think both onsite processing on the rig, as well as expanding the bandwidth of data transmission capabilities of the global rig fleet, can offer a potential for using the data more effectively and driving more insight from the data.
A lot of offshore rigs have a limited bandwidth, and there are many vendors vying to transmit that data. It’s a finite resource, so I think continuing to expand data transmission bandwidths on rigs will help a lot. With our eHawk monitoring service, for example, we frequently find limitations in terms of ability to send data off of the rig.
For younger people who have joined the industry within the past decade and haven’t lived through a downturn like this one yet, what advice would you give to encourage them to stick with it?
It will get better. Although this is a hard time, it will make you better. If business only ever goes up, none of us would ever learn how to make difficult decisions and shepherd our businesses through downturns. The adversity brought on by this sort of downturn has made great managers in this industry.
By my count, this is my sixth downturn. We’ve learned over the years and through the cycles that you have to act swiftly. It can be very painful and difficult, but it is the time to learn good leadership and management skills. The folks that see this through and emerge in the prosperity that’s waiting for us on the other side will emerge as better leaders and better managers.
It’s a wonderful industry, and it’s a tough industry. Very few industries see downturns like this. It’s breathtaking how quickly the floor can drop out, and it always feels terrible when you’re going through these downturns. However, you’ve got to look at the fundamentals. You’ve got to look at supply and demand for oil and recognize that it has to get better. This is not sustainable, and it will get better. I tell our folks that every week that goes by means that we’re a week closer to recovery. DC
NOVOS, IntelliServ and eHawk are trademarked terms of NOV.