In new digital ecosystem, considerations for asset integrity must evolve
Physical inspections remain important, but cybersecurity, data analytics now play bigger roles in driving safety-critical decisions
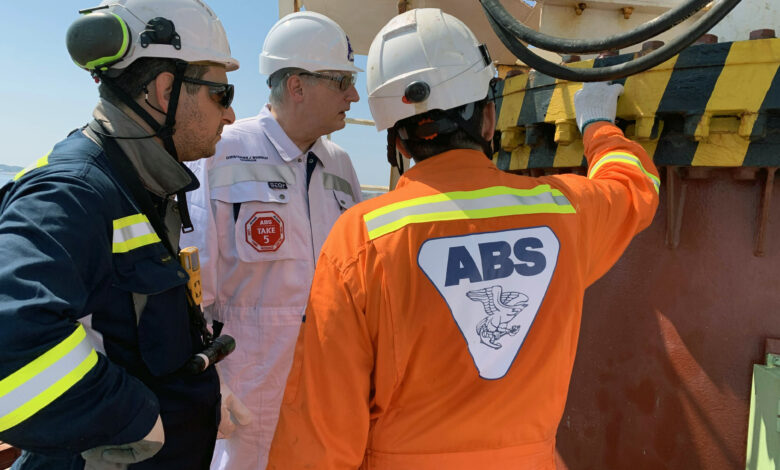
By Stephen Whitfield, Associate Editor
Market and ESG challenges in the offshore drilling industry dictate that companies must operate more efficiently than ever. This includes optimizing maintenance schedules and inventory to always ensure asset integrity.
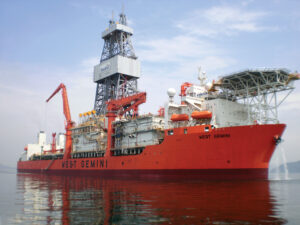
The term “asset integrity” typically conjures up thoughts of rig inspections or equipment maintenance, and drilling contractors are certainly developing systems to better manage their rigs and the equipment on them. However, the digital ecosystem is now one of the biggest concerns among the regulators, classification societies and flag states that make up the rules and guidelines for keeping rigs functional. Like drillers, these stakeholders are also looking for ways to leverage the massive amounts of data being generated from rig equipment to help them better anticipate and manage potential integrity issues.
“When I started at ABS 25 years ago, I can promise you we didn’t have data scientists working for classification societies,” said Matthew Tremblay, Senior VP of Global Offshore Markets at the American Bureau of Shipping (ABS). “Now, we’re bringing an entirely different set of skills into the organization – data scientists, computer scientists, IT professionals – and they’re all tied to the management of data and the development of applications that utilize this data. It’s a real interesting evolution, and this challenge is something that we have to meet.”
As the world of inspections and classification becomes more digitized, the issue of data protection is only growing in importance. Several industry stakeholders cited cybersecurity as one of the biggest areas of focus as they review their procedures and develop data management systems. In fact, cybersecurity has become as important of a factor in asset integrity as the physical equipment on the rig. But without a unified approach for handling cyber risk, organizations are finding it challenging to develop solutions that satisfy everyone.
“Cybersecurity is definitely something that needs to be addressed,” said Cosmin Bozenovici, VP Technical – Offshore at International Registries Inc (IRI) and its affiliates, which provide administrative and technical support to the Republic of the Marshall Islands (RMI) Maritime Registry. “The offshore industry is in need of a unified plan so risks can be managed more efficiently. Without a unified plan or standards, there may be a potpourri of solutions, which will present additional challenges.”
Adapting during a global pandemic
The RMI registry plays an important role in the world of asset integrity. It is one of the leading quality maritime registries in the world, with more than 5,200 vessels registered under its flag. Inspections are part of the RMI’s asset integrity program, and annual inspections focus on the maintenance and operation of the safety systems on the rig, as well as crew awareness, including their competency in executing emergency procedures.
Mr Bozenovici noted that the COVID-19 pandemic has created difficulties for drilling contractors, disrupting layers of risk reduction, which are needed to maintain a safe environment on a rig. These include normal inspection regimes, standard crew change schedules, the ability to obtain spare parts for equipment, as well as general oversight of operations.
The industry’s focus on safety did not wane in the face of these difficulties, he said, and crews continued to work to ensure rigs operated safely. However, increased stressors on the rig crews during the pandemic made it more difficult to identify and address critical deficiencies with common safety items on the rig, which is a key part of the inspection process.
Even though the world appears to be recovering from the pandemic, COVID-19 continues to be present, and Mr Bozenovici said that stakeholders are still dealing with its long-term effects. “The pandemic required us, as a flag state, to be flexible, adaptable, and to support our owners and operators in new ways, especially in crewing and safe vessel operation.”
Adapting through the pandemic required the RMI registry to move to a remote inspection model, with onsite personnel meeting inspectors over videoconference. The RMI then pivoted back to in-person annual inspections as ports around the world began allowing for in-person inspections. Moving forward, the registry will allow condition surveys to be done remotely when conducted by International Association of Class Societies (IACS) members.
Mr Bozenovici said that while annual inspections have a “comprehensive” list of items that need to be checked in person, some smaller problems do not require a physical presence in order to be remediated.
When it comes to cybersecurity, IRI has spearheaded the development of a mobile inspection application. It allows inspectors to collect and transmit data using mobile devices and tablets and produce a report on the spot, without the need to exchange USB sticks/flash drives.
Mr Bozenovici also pointed to IACS adopting two unified requirements (URs) on the cyber resilience of vessels in January 2021, citing it as an example of a potential framework for cybersecurity regulations. UR E26 focuses on the secure integration of Operational Technology and Information Technology equipment into a vessel’s network. UR E27 provides requirements for the cyber resilience of onboard systems and equipment, as well as the interface between users and computer-based systems. Both URs will take effect for new ships contracted for construction starting 1 January 2024.
While the URs provide a framework for handling cyber risk, Mr Bozenovici noted that they have not been endorsed by other maritime organizations. Also, they do not provide guidelines for other areas of cybersecurity, such as vulnerability assessments and incident response plans.
While the RMI Maritime Administrator is actively engaged in the major committee and subcommittee meetings and maintains a permanent representative at the International Maritime Organization (IMO), a UR on cybersecurity has not been published.
Even so, Mr Bozenovici said that URs will both strengthen and protect the industry. “Many operators are not conducting deep vulnerability assessments or implementing practices like perimeter protection against drones,” he said. “Those that do conduct such assessments may not use the results, which could create a gap in their security posture. In the absence of regulations, we’re seeing few cyber training drills or exercises being conducted, which basically leaves people unfamiliar with how to identify and respond to a cyber incident. This emphasizes that we need to get together and come up with a unified plan.”
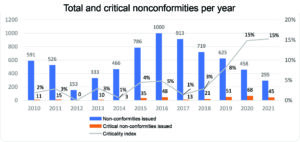
Regulatory framework under review in Brazil
As the Brazilian oil and gas regulator, the National Agency of Petroleum, Natural Gas and Biofuels (ANP) is responsible for supervising E&P activities, including operational safety performance. Brazil first implemented its regulatory framework for asset integrity in 2007, focusing particularly on maintaining mechanical integrity of offshore facilities, including drilling rigs. The framework established procedures for risk management, identifying hazards and implementing safety barriers to reduce the risk of potential events.
Except for updates covering well and subsea integrity management rules issued in 2015 and 2016, the country has made no significant revisions to its rules for onshore installations, originally published in 2010 and 2011. However, the ANP is undertaking a comprehensive review of the framework this year and anticipates releasing an updated framework next year.
Raphael Neves Moura, Manager of ANP’s Operational Safety and Environment Division, said that the updated regulation will likely incorporate more procedures centered around human factors, such as organizational leadership, risk perception, decision-making processes on a facility, and risk communication.
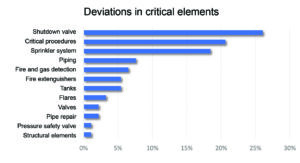
“I think we will develop a more balanced regulation,” Mr Moura said. “We have a really strong focus on the mechanics and some of the major risks, but there are other major risks that weren’t being fully addressed. We identified the safety-critical elements, but you have to understand the performance of each one of those safety-critical elements. The barriers for incidents are safety elements. If you don’t have the barriers available, you have to put them in place.”
The review also involves incorporating regulations from government agencies in other countries. In its 2021 Annual Safety Report, the ANP touted the importance of collaboration with regulators from other countries to establish benchmarks for process safety on offshore facilities. In particular, the report mentioned the agency’s work with Norway’s Petroleum Safety Authority (PSA). In October 2020, ANP and PSA signed a memorandum to establish a work plan to further reduce safety risk in E&P activities, sharing information and approaches to various issues related to asset integrity. This includes cybersecurity, the definition and organization of incident records and performance indicators, and the life extension of aging facilities.
In its 2021 Safety Report, ANP cited several practices applied by the PSA that it may incorporate into its own workflow. One such practice is issuing questionnaires to onsite personnel to assess their perception of various safety elements. For instance, onsite personnel may be surveyed on cybersecurity to assess their company’s level of preparedness in responding to cyber threats, as well as the impact of a cyber attack on operational safety.
Additionally, ANP noted PSA’s practices on monitoring performance indicators (e.g., the number of safety-critical equipment tests and failures) for fire and gas detection systems, BOPs, riser shutdown valves, downhole safety valves, pressure safety valves and automatic diverter valves. Currently, ANP is working on a project with industry participation to monitor specific indicators for safety elements that have a high rate of critical nonconformities (deviations from ANP regulations).
“When you look at us and you look at the international regulators for countries like Norway, the United States, the UK and Australia, our safety records are quite good” Mr Moura said. “The best practices here in Brazil are well implemented, and we have established standards, but we know safety risk is considerable.”
While the regulatory review will likely address newer risks like cybersecurity, Mr Moura said it is unlikely that the ANP will make significant changes to its existing operational safety protocol for handling physical equipment on the rig. This does not mean that safety protocols are not of concern to the agency – in fact, the ANP noted an upward trend of critical nonconformities in its inspections of offshore facilities. Its 2021 Safety Report showed that, from 2010-2018, there was an average of 17 critical nonconformities, yet 68 were noted in 2020 and 45 in 2021.
Further, the ANP noted that the criticality index – the ratio between the number of critical nonconformities and the total number of nonconformities – was 15% in both 2020 and 2021, which means there has been no improvement.
Roughly 3% of critical nonconformities in offshore units were identified during so-called thematic audits, in which ANP inspects specific safety-critical systems. Such recurrence on nonconformities means the results do not meet expectations on continuous improvement. When it comes to thematic audits, it is customary for the ANP to ask operators to carry out a self-inspection and implement action plans to address any issues prior to the arrival of ANP inspectors.
The ANP said it believes the poor result of safety-critical elements managerial practices indicates companies are not planning for and providing sufficient resources for implementing their safety management systems. The 2021 Safety Report emphasizes the need for companies to ensure the availability and reliability of critical systems and equipment, as well as to implement immediate contingency measures in case of failure, degradation or absence of such barriers.
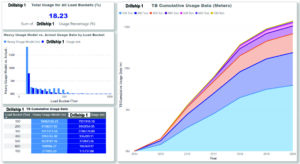
Managing the asset’s lifecycle
Asset Lifecycle Management (ALCM) is a program designed to provide Seadrill with a quantitative measure of the lifecycle of its rig equipment, as well as a continuous condition monitoring program. Launched in 2018, the program is a means by which the company performs disassembly inspections of the drilling and hoisting equipment according to the load cycles accumulated by the equipment, and by the equipment’s physical condition.
Previously, Seadrill performed disassembly inspection of all drilling equipment in five-year intervals, according to the alternative inspection guideline table established in API RP-8B.
John Dady, Director of Technical Services at Seadrill, said a time-based inspection frequency has proven to be ineffective in recent years. Insight into the actual condition of a drilling equipment system has been traditionally limited to existing maintenance records, which often have limited information. There is usually a lack of baseline information, such as vibration data, and organized failure data.
“Time-based inspection frequency does not reflect the additional inspection criteria required for equipment that has spent all of its time in operation under the most extreme working conditions, close to its operating limits,” Mr Dady said. “Conversely, more robust equipment that has only been lightly used can be over-inspected, and that could impact the operation with unnecessary time out of service. With Asset Lifecycle Management, we are looking to address these issues and provide equipment-specific inspection requirements.”
The ALCM program began with the overhaul of Seadrill’s first TDX-1250 top drives, which had been operating in the US Gulf of Mexico (GOM) for the previous five years. The critical load-bearing components were found to be in as-new condition during the disassembly inspection, and a calculation of the equipment usage compared with its design revealed lower usage values than expected. Since that initial inspection, Seadrill has not removed a TDX-1250 for overhaul and has only overhauled one crown block that was identified through condition-monitoring tests to have defects. Its planned target for this equipment is for it to operate through 2024 before evaluating further lifecycle potential for the equipment. Under the time-based inspection protocol it had previously employed, the company would have taken the top drives out of service in 2019.
The next phase of ALCM development will focus on expanding Seadrill’s analysis capabilities to additional equipment and enhancing its maintenance planning. This year, the company brought online additional toolsets enabling the condition monitoring and independent lifecycle analysis of an expanded subset of equipment components on its current rigs. It is also developing lifecycle analysis for BOP control systems and drill through components, as well as new data models for its existing equipment to enable predictive estimations of equipment usage in future drilling campaigns.
Digital systems are also playing a role in Seadrill’s asset integrity management protocol. In early 2019, the company partnered with a third party to develop a tool that could identify potential duplicates in its item catalog based on prioritized search criteria. The platform provides a systemized workflow for reviewing, updating and migrating changes to Seadrill’s Item Master in Maximo, allowing subject matter experts to verify duplicate parts, confirm manufacturer part numbers, clean up parts descriptions and remove duplicates.
Russ Daniels, Head of Global Materials Management at Seadrill, noted that the company has realized a 30% consolidation in its parts catalog, driving a more efficient process to find the right parts to put on order. By cleaning up the catalog and inventory on the rig, the company is now able to avoid buying parts twice due to having the wrong naming conventions, since they all have the same part number and description on every rig.
All purchase orders generated from Maximo are routed through Seadrill’s proprietary Rig Inventory Optimization (RIO) system, which reviews the inventory of the requested item on each rig in its fleet to see if it has any of the requested material available in overstock. If so, the RIO system puts a link containing the required data on the buyer’s procurement workbench in the company’s enterprise resource planning (ERP) system to help the buyer make a decision on whether to utilize its internal inventory or go to a supplier for purchase.
The RIO system has helped the company to realize a net savings of more than $30 million through the optimization of its internal inventory, according to Seadrill.
Leveraging advances in digital twins
ABS has a number of programs designed for asset integrity management, including risk-based inspection programs and condition-based inspection programs. ABS also issues guidelines (“Rules for Building and Classing Mobile Offshore Units”) for building and classing drilling rigs covering, among other things, requirements for machinery and equipment; the design requirements for safety systems; and the design, testing and survey requirements for the certification of equipment, machinery and system components. Its latest edition of the guidance was released in January.
Lately, ABS has been looking at ways to better incorporate digitalization into its protocols. One area of interest is digital twins, a tool Mr Matthew Tremblay said could be valuable both for conducting surveys and assessing problems on a vessel. The ABS Offshore Enhanced Rapid Response Damage Assessment expands the scope of the society’s traditional Rapid Response Damage Assessment by maintaining an asset-specific condition model and operation within a digital twin. The system has the potential to provide valuable information in the event of an emergency needing rapid response and technical support – a model of the affected areas can be extracted quickly from the maintained digital twin for analysis.
ABS is also looking at ways digital twins could be used as condition models regularly updated by data coming from the vessel to enhance system safety and environmental protection, Mr Tremblay added. ABS could then utilize that condition data to measure asset-specific survey requirements. However, developing a unified system that could work with varying types of digital twins is a challenge because of the different data formats operators use.
“It is too soon to drive the industry to common practices since that will stifle innovation,” he said. “Instead, we are building a system and process that can manage all of that information diversity and be adaptable to change. What we would love to be able to do is import any 3D model, allow our engineers to do our design approval with the 3D model and push it back to the operator without having to print 2D PDF drawings that we need to approve. As a class society, we’re now challenged to build systems that interact with everything, and that’s a massive challenge, but one we are up to meeting.”
ABS has also been focused on making data easier to access and understand for its clients. In July 2020, it launched a suite of advanced analytical fleet management and vessel compliance services, available through the ABS mobile application. The services aim to simplify access to operational, technical and compliance fleet intelligence and ABS Class services to manage the operating health and performance of fleets. The services include:
- ABS Smart Scheduler, which leverages real-time automatic identification system data to maintain fleet compliance, tracking survey status for all vessels in a fleet and issuing alerts when surveys are due;
- Custom Checklist, which combines port state data from ABS-classed vessels to provide a port-specific checklist for crew and fleet managers prior to the vessel’s arrival at a port;
- Post State Control Risk, which provides customized port state control analytics by vessel or fleet; and
- International Safety Management (ISM) findings, customized to individual vessel performance, allowing companies to view a destination port’s top ISM-related deficiency items against their vessel’s matching findings from ABS class records.
The services are designed to augment ABS MyFreedom, a software program launched in November 2019 that provides an interface for survey, compliance and maintenance reporting.
Mr Tremblay said that, as operators have improved their processes for collecting data around maintenance and operational performance, class societies must figure out how to align the classification process with a new paradigm of condition monitoring. Digitization, he said, provides an opportunity for the industry to utilize more granular data about asset condition to make more informed decisions for inspections and maintenance. DC