Drilling & Completion Tech Digest
Xtreme Drilling introduces 23,500-ft capable land coiled-tubing well intervention unit
Xtreme Drilling and Coil Services recently unveiled the XSR200, a land coiled-tubing well intervention unit with a depth capability of 23,500 ft. It is the largest such unit for land operations, according to the company. The unit is designed to aid North American operators as they push horizontal drilling to record lengths in shale plays.
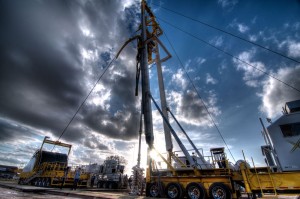
“Most of the units in the market can only get to about 14,000 ft or 15,000 ft,” Tyson Seeliger, vice president of sales and marketing for Xtreme Drilling, said at the unit’s December debut in Houston.
With the XSR200, which uses 2 5/8-in. coil and has an 86-ft mast, Xtreme Drilling has been able to remove the surface equipment limitations of conventional coiled-tubing units and allow for the completion of deeper wells.
“We built the rig around the most aggressive well depths, which were 23,000 ft. The Eagle Ford is already starting to push out further and further,” said Reg Layden, general manager of international operations. “The weight of the string (on our surface equipment) is 110,000 lbs to 120,000 lbs and our injector pulls 200,000 lbs. We’re only limited by what our coil can do now.”
Saudi Aramco develops downhole drilling microchip to acquire data
Saudi Aramco’s EXPEC Advanced Research Center (ARC) Drilling Technology Team (DTT) recently achieved the first major field test of its four-year project to develop industry’s first downhole drilling microchip.
“This important stage of the microchip technology development has proven that the project is on the right track to deploy such a miniature device for practical and useful applications in the near future,” Nasser Al-Khanferi, DTT chief technologist, said. EXPEC ARC worked with Tulsa University on the project.
The microchip has the potential to change the way downhole data is acquired. Such data can help drillers more readily diagnose hole problems while drilling to optimize and improve rig operations.
“Our dream was to develop a low-cost and alternative downhole data acquisition system capable of recording measurements such as pressure and temperature along the circulating path of drilling fluids,” Shaohua Zhou, DTT technologist, said. “Such a technology would optimize mud and cement formulations while drilling and further reduce well cost.”
A microchip is pumped or dropped into the drill string and, acting like a robot, is capable of recording in-situ data and stores it on board the chip while traveling downhole, eventually returning to surface with the circulating drilling fluid. Once recovered at surface, the recorded data would be instantly downloaded wirelessly at the rig site or transmitted to an operations center.
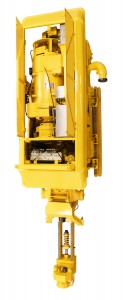
GDM 850 top drive built for the future
Global Drilling Support (GDS) recently unveiled the GDM 850 top drive at its Houston facility – a Serial No. 1 top drive that will be installed on a newbuild 3,000-hp inland barge to drill offshore Nigeria for Mega Drill. The concept behind the design focuses on reliability and equipment longevity.
“We wanted it to work not for today’s drilling parameters but for future drilling parameters, with enough speed and torque to withstand what operators will be drilling in five to 10 years,” said Keith Holliday, president of GDS International.
The GDM 850 features a 1,500-hp motor with a self-aligning coupling, a solid drive pinion, a helical gear assembly and forced-spray lubrication. Submerged thrust bearings also extend operational life.
The GDM 850 operates at 1,570 continuous hp and delivers 64,000 ft-lbs of continuous torque at 0-116 RPM up to 250 RPM. A comprehensive maintenance module provides for proactive servicing of the unit.
Additional information about the GDM 850 can be found at dev4.iadc.org.
Woodside pushes total section depth to 6,250 ft
Woodside Petroleum recently reached a total section depth of 6,250 ft on the Tidepole East-1 exploration well offshore Western Australia with the help of AGR’s riserless mud recovery (RMR) technology.
It was the first time that Woodside had used the casing while drilling (CWD) method on one of its wells, and the company believes the depth reached sets a record for the technique. RMR enabled Woodside to use the type of drilling mud needed to maximize the wellbore smearing effect that CWD provides.
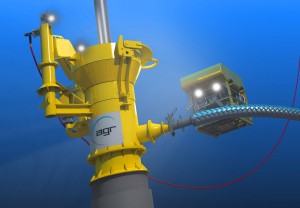
The system allows top holes to be drilled using weighted mud, with fluid and cuttings returned to the rig and with no discharge. It is also able to supply the low pump rates and good hole-cleaning capability required to drill efficiently despite the relatively narrow annulus that was a feature of this project. There were no losses to the formation during that stage.
Standard internal or external wellhead adapters could not be used on this project for the RMR’s suction module (SMO) without extensive modification to the permanent guide base, or without causing difficulties when it came to landing the high-pressure wellhead on the low-pressure wellhead later in the operation.
AGR provided a solution involving an internal adapter being devised that could be split. This meant that the casing could be drilled down with the SMO.
The operation went smoothly, achieving a rate of penetration of approximately 197 ft/hr.
Aker Wirth marks delivery of 250th TPK 2200 mud pump
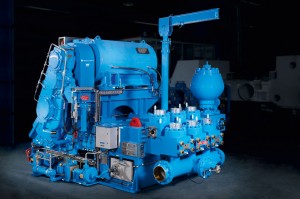
Aker Wirth recently delivered its 250th mud pump in the TPK 2200 series to the Daewoo Shipbuilding and Marine Engineeringshipyard in South Korea.
The jubilee pump will be one of four pumps in Vantage Drilling’s Tungsten Explorer deep sea drilling vessel. The drilling vessel will go into service in 2013 and will be capable of drilling in water depths up to 3,600 meters.
The TPK 2200 can pump up to 1,640 liters of drilling emulsion per minute at a maximum pressure of 517 bar. It can operate from -40°F/°C to 140°F (60°C).
FMC sets deepwater completion record at 9,627 ft on Tobago field
FMC Technologies’ enhanced vertical deepwater tree (EVDT) system has set a deepwater completion record of 9,627 ft (2,934 meters) on the Shell-operated Tobago field in Perdido in the Gulf of Mexico. The record, achieved in November 2011, surpasses the previous milestone of 9,356 feet (2,852 meters) that was established in 2008 at Shell’s Silvertip field, also part of Perdido. The previous record also was achieved with an FMC-designed EVDT.
Ulterra bit drills Eagle Ford well at record pace
Ulterra’s 8.75-in., six-bladed matrix bit with 16-mm cutters recently drilled from surface casing to a total depth (TD) of 9,953 ft at a record pace of 93 ft/hr in the Eagle Ford Shale. The new U616M drilled to TD in 107 hrs, a time savings of 37.5 hrs over the fastest offset of 144.5 hrs. All three intervals – the vertical, curve and lateral – were drilled with the same bottomhole assembly. The U616M bit incorporates technology to maintain the high rates of penetration required in the drill-out, as well as the ability to track straight in the lateral section. The combined directional and performance advantages of the U616M increase slide efficiency and motor yields to reduce slide percentage and on-bottom drilling hours.
Smith Bits’ Kaldera drills record 77 hours in single run
Smith Bits’ recently introduced Kaldera advanced roller-cone bits has set a drilling record with 77 hrs in a single run, marking a 37% increase in on-bottom drilling hours compared with offset runs. The bit is made for geothermal and high-temperature drilling applications using advanced materials technology for an engineered sealing and lubrication system.