Cementing: Taking in lessons learned
Industry engaged in all-out effort to strengthen standards, testing, placement for better wellbore integrity
By Katie Mazerov, contributing editor
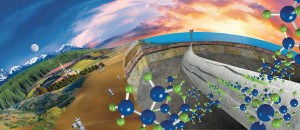
Hydrocarbon production is a risky business, and nowhere is this more evident than in the deepest, darkest waters on the planet, where some of the brightest prospects for the future lie miles beneath the surface. High pressures and temperatures, extended laterals and unstable reservoirs are among critical challenges operators face in this vast frontier that includes the Gulf of Mexico (GOM) and West Africa. With that in mind, an industrywide effort has been under way to minimize risk and ensure that the necessary systems and processes are in place to make deepwater and ultra-deepwater development safe and efficient. A key focus of the effort involves well cementing, everything from design to testing to placement.
Using cement as a viable barrier to protect the wellbore from dangerous influxes of water or gas looms as one of the biggest issues facing the industry as it looks ahead 20 years and beyond. Operators, major service companies, academics, regulators and trade associations are placing significant focus on every aspect of the cementing process, working to enhance current designs, standards and protocols, and engaging in out-of-the-box thinking to develop smarter and more durable methods that will deliver a high degree of integrity in the increasingly complex wells of the future.
One of the key players in this endeavor is the Research Partnership to Secure Energy for America (RPSEA), a nonprofit corporation established by the US Department of Energy that is providing financial incentives for a number of ambitious deepwater cementing research projects ranging from radio frequency identification (RFID) to intelligent casing, and even a study on human error. “We are looking at this issue from a holistic viewpoint and coordinating knowledge-sharing among the various stakeholders,” said James Pappas, vice president of RPSEA’s Ultra-Deepwater Program. “For example, we are taking academic research in nanomaterials and partnering with companies that can turn science into engineering solutions.”
However, much of the push is coming from the oil and gas companies that are leading industry into the deepwater fields, where safe extraction of the huge oil and gas resources is paramount. Well cementing is among the top priorities.
“Cementing is one of the very important elements that well integrity experts take into account in their evaluation of risk and their assessment of wells that have been delivered,” said Dan Mueller, cementing specialist, global drilling engineering for ConocoPhillips. “It is safe to say that the Montara and Macondo incidents forever changed the well-cementing landscape. How we model, design, test, place and verify cement properties are all considerably different than they were pre-2010.” Montara was an uncontrolled discharge of oil and gas off the coast of Western Australia in 2009.

Collaborative effort
An important part of the undertaking has been the collaboration between the industry’s cementing community and API to evaluate and update current well cementing standards. In December 2010, API’s Well Cementing Subcommittee (SC-10) published what is now API Standard 65-2, which addresses the issue of isolating and cementing potential flow zones during well construction.
“This is a landmark document for the well cementing industry in that it is both a recommended practice and it establishes requirements,” Mr Mueller said. “It signifies the cementing community’s attempt to take into account some of the lessons learned from Macondo and take steps to limit exposure in these areas going forward.”
The standard was included in the US Federal Register in August 2012 and is now part of the cementing requirements related to permitting in the GOM under the Bureau of Safety and Environmental Enforcement (BSEE). Standards addressing deepwater cement testing will be published this year, and a standard regarding foamed cement preparation and testing is being revised and expected to be released this year. Foamed cement is designed to address shallow-water flow.
The focus is on testing and evaluating cement under conditions that are as realistic as possible. “We are writing our testing procedures and documents in a fashion so we can, as best as possible, simulate the placement and thermal history of the conditions the cement will be exposed to during the placement process and using that as a basis for evaluation,” he continued. “The testing requirements are now higher, and requirements for simulating placement history are there. Since we depend so much on testing results to move our judgments in one direction or another, it is imperative that the tests be as realistic as possible.” The procedures are being included in recommended practices so service companies can conduct testing under uniform conditions.
Pressure and, especially, temperature also are important considerations in well cementing. “We have a reasonable ability to predict the pressure state of the system. But since temperature is the single most critical factor influencing the behavior of a well cement, we are being very diligent in our thermal modeling,” Mr Mueller said. “We will use multiple thermal models in many cases to ensure temperature is being properly taken into account.”
Oil and gas production companies will be incorporating the new procedures and regulations into their operations while already engaging in more in-depth vetting of cementing proposals and recommendations. Design elements that are being taken into special account include casing centralization, equivalent circulating density (ECD) management and mud displacement efficiencies, which all lead to establishing a quality cement sheath, Mr Mueller said.
“This very necessary work has changed the way we think about cementing,” he added. “As an industry, we have looked at our systems and processes and found new vigor to get these standards in place to avoid any incidents going forward. There are many ongoing joint industry projects and collaborative efforts looking at deepwater technologies to make these operations proceed in a streamlined way. Deepwater is an important part of many operators’ portfolios, and over the past 12 months, we’ve seen a substantial ramp-up in activity in the sector.”
Collaborative industry effort leads push to enhance deepwater cement standards
By Katie Mazerov, contributing editor
In keeping with its historical mission to develop standards and recommended practices (RP) in a collaborative fashion that ensures all stakeholders and interests are represented, API has been at the center of a rigorous, industrywide effort over the past three years to publish a number of offshore safety measures, many of them focused on the critical aspects of deepwater cementing.
“This work, involving all sectors of the oil and gas industry, began with four joint industry task forces that came together in a very short time after Macondo to produce recommendations that the White House used as a basis for its response to the event,” said David Miller, API director of standards. “A number of key recommendations have come out of this coalition, including the Center for Offshore Safety.” Established in 2011, the center promotes and adopts standards of excellence to ensure continuous improvement in safety and offshore operational integrity.
The initial focus of the industry’s efforts was API Standard 65-2, addressing isolating and cementing potential flow zones during well construction. “Following Macondo, an industry group got together and immediately started revisions on API 65-2, taking lessons learned from the incident and really enhancing the document in terms of the requirements needed for offshore safety,” said senior standards associate Shail Ghaey, who is the staff liaison for API’s Well Cementing Subcommittee.
Since then, the subcommittee has engaged in work to revise and develop other cementing-related documents, including API 65-1, now referred to as API RP 65, which addresses cementing shallow-water flow zones in deepwater wells. “Considerations when cementing in the upper section of the well are slightly different than they are for sections farther down the wellbore,” Ms Ghaey explained. “Cement is applied in shallow zones to isolate any potential flow zone from water or gas.”
Cement testing
Another series of documents specifically addresses the testing of well cement. Included in the series are RP 10B-2, RP 10B-3 and RP 10B-4 – testing in labs under simulated in-situ conditions along with general atmospheric and temperature-related factors.
Later this year, API also will publish RP 96, which provides deepwater well design considerations. “This document will address the different kinds of barriers, including cement and mechanical barriers, that can be used when designing these deepwater wells,” Mr Miller said. “This will be a fairly significant step forward for the industry in deepwater applications.”
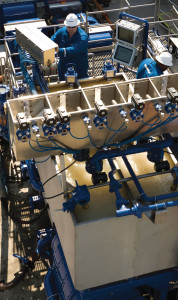
A viable barrier
Much of the ongoing research centers on redefining what is required for cement to provide a viable barrier. “If we want cement to be a barrier, we can’t just go in and cement a zone, we need to define the criteria for it to be successful,” said Ragheb Dajani, senior drilling engineering advisor for Hess Corp. “We need to define how far up in the zone we need to cement and understand if and when a zone has been successfully cemented in terms of placement. For example, we’ve agreed that 50-psi compressive strength is the minimum standard for calling cement a viable barrier. Previously, that was not defined.”
A lot of energy is being put around the operational aspect of ensuring that the practical realities reflect the theory. “If we’re dealing with 100 bbls of cement and 1,000 bbls of placement, for example, we have to do a lot of work to make sure the cement is placed effectively,” Mr Dajani said.
Other issues being addressed include new government stipulations that operators must run a worst-case discharge tie-back, which necessitates that an extra casing be run. Due to wellbore dimensions, that second casing creates an ultra-narrow annulus that must be cemented. “The pressures are enormous, and placement is extremely critical to prevent casing collapse,” he noted. “This is very challenging and new to the industry; only four jobs have been done since the regulation was put in place.”
Difficulties also can occur in situations of low-salt regressions, where lower pressures occur after exiting the salts, creating a drop in pressure and necessitating that mud and cementing weights be changed. “A lot of times that is an issue with lost circulation, and we know that lost circulation is a challenging issue if we can’t place the cement where it needs to be,” he said.
Finally, in the top-hole section, where the surface casing is placed, shallow flow hazards can be problematic, for example, when silty soil contains a high-pressure section. If there is not enough hydrostatic pressure to hold it in place, the formation will start flowing – meaning the wellhead and blowout preventer (BOP) won’t have any soil support. “Choosing the right technology, such as a foamed system, and getting the correct volumes and properties to mitigate that scenario is required, and we need to ensure that the methods we know work are being deployed.”
Hess has implemented the new standards and recommended practices internally and will apply them to the company’s operations in the GOM, including on two of its contracted deepwater rigs and a program that will be launched this year.
“We feel the industry is where it needs to be from a best practices and standards perspective, and we are working on bridging the gap between what has been put on paper and what needs to be implemented operationally in the field,” Mr Dajani said. “I believe the biggest gap is getting the young engineers trained quickly, especially field training and experience, so they can truly understand the intricacies of what happens on a drilling rig.”
Long-term viability

The long-term viability of cement as a barrier is also very much on the agenda. “One of the primary challenges we have as an industry is not just in providing the correct recipe for cement materials to do a proper job of isolating and protecting the wellbore but in knowing what the long-term stability will be,” said RPSEA’s Mr Pappas. “We are searching for ways to gain more confidence that we have the necessary long-term protection while meeting all of our social responsibilities.”
To that end, laboratory testing is tracking the behavior of cement materials, mimicking conditions seen in deepwater environments and subjecting cement to cyclic heating, cooling and other stresses to determine the long-term effects. The history on cement modeling in land environments is being used to extrapolate what can be expected to happen in deepwater.
RPSEA is focusing on niche ideas that aren’t being addressed by anyone else, and on identified weaknesses, including hole-cleaning while drilling and the subsequent cementing process, and annular pressure build-up. One proposal is looking at new methods of detecting cement bonding with both the formation and the pipe. “The cement bond tools do a pretty good job of providing a cement-to-pipe bond but not as good a job at visualizing cement bonding to the rock,” Mr Pappas said. “We review ideas and proposals like these and determine which ones are going to move forward and then monitor the progress.”
Researchers at the University of Oklahoma are working to develop a telemetry system that, powered by tiny batteries, can transfer information about the cement and the flow of production fluids up the pipe. The University of Houston and partners are researching the possibility of placing small RFID chips in drilling fluids to provide a better understanding of hole quality, which is critical for a good cement bond, and even placing the chips in the cement itself.
“We are hoping these tools can work in the liquid stage but also after the cement hardens so we can gain information on the stresses, strains and changes of the cement over time, after the well has been perforated and frac-packed,” Mr Pappas said. “We can use these devices to learn and also theoretically read and measure changes in real time, which would be a leap over what is available now.”
To address the problem of ECD and pressure and temperature changes in deepwater reservoirs, RPSEA has contracted with engineering firm CSI Technologies and partners to develop a novel system of pumping cement down the backside of the well, with tools to lock the cement in place at the bottom of the casing. “The very small gap between the reservoir pressure and the fracture gradient, or breakdown pressure, can potentially crack the rock, causing lost circulation, particularly in subsalt wells,” he explained. “Tremendous pressures occur when pumping cement down the inside of the casing string and circulating it around the back.”

9 5/8-in. is 9, etc). “Y” or “N” means “Yes” or “No” as it applies to the risk identified in each row. Shallow-water flow risk, for example, applies to the first couple of strings in the well; thus, the larger numbers might have a “Y” but an “N” for the rest of the strings where the risk does not apply.
The reverse circulation project will include developing tools to accurately measure friction losses on the backside. The method has been done in land wells where the well is not cemented all the way to the top or when running a small coiled-tubing unit between the casing and the hole, he noted.
Another initiative involves studying human error in the drilling process, including during cementing. “We want to know what makes people tick and what scares them from shutting systems down when they see something is wrong,” Mr Pappas said. The project includes the creation of a database of near-misses in the GOM to try and model human behavior.
Managing risk
Meanwhile, in an effort to ensure safety and minimize human error, service companies have put in place their own risk management procedures regarding deepwater cementing while continuing to develop new technologies and enhance existing services.
Schlumberger has had management of change protocols in place to address issues such as annular casing pressure, temperature variations and last-minute well construction changes that can impact the viability of the cement. This is in line with industry’s overall push to focus on assurance, verification and documentation as it strives for efficiency. “In the offshore sector, dayrates and other costs are quite high, so there is enormous pressure to be efficient every step of the way,” said Gunnar DeBruijn, well integrity domain manager, North America, for Schlumberger Well Services. “But we also need to recognize how efficiencies impact the overall drilling operation and, ultimately, the cement job.”
In that regard, prior to execution of the cement job, well construction documents are reviewed by operators, drilling contractors and third-party providers of services such as cement, to ensure the cement will provide a continuous barrier. “Flawless execution is the key to a good cement job,” he said. Data collected from both the wellbore and the cement unit is important for documentation, and the interpretation of the data must be done for verification to meet industry standards and regulatory requirements.
“As we get into deeper wells, we tend to have bigger wellbores to deliver production, so we have larger casings, more casing strings and tighter annuluses we have to cement,” he continued. “Often, we’re drilling across large salt intervals so we have to manage an ever-tightening pressure window, meaning we have to be very precise in managing the pressure. In wellbores that are very challenging, we have to deliver the rheology and density as we design the cement.”
Data on temperature variation is especially critical. “In deepwater, we have cold temperatures at the mud line and very hot temperatures at the bottom of the well, so we have to tailor the top section of cement one way and the bottom another way,” he explained. “Most other segments of the industry only require a maximum temperature to understand if tools are installed correctly, but cement must be set to a specific temperature environment. For example, for the first casing string, the cement needs to provide structural support and also set quickly to act as a barrier to prevent shallow flow.”

To overcome challenges such conditions present for standard Portland cement, Schlumberger has developed high-performance cement systems and additives to ensure viability and long-term durability. The EverCRETE is a CO2-resistant cement, and the FUTUR, active set-cement technology, is a self-healing cement system that works after the cement has set, from the time it is placed until the end of a well’s operational life.
“As we do more design work on these wells, we also assess the stresses they go through and look at implementing cement systems such as the FlexSTONE advanced flexible cement technology that provides zonal isolation by enabling set cement to conform to the changes that occur during the drilling, production and abandonment phases of a well,” Mr DeBruijn said.
For deepwater, the DeepCRETE deepwater cementing solution isolates the formation and develops compressive strength faster than Portland cement. When combined with Schlumberger’s gas migration technology, the solution provides shallow flow control. The DeepCEM deepwater cementing solution can perform in environments as low as 32°F.
Schlumberger also has added more oversight to its processes, reviewing every deepwater cement program worldwide. “If we see risks we shouldn’t take in an operation, we inform the operator and other service providers so the risk can be mitigated,” Mr DeBruijn noted. “Oversight also helps with continuous improvement and transfer of knowledge from one operator to another.”
A proactive approach
Baker Hughes has developed a matrix that is reviewed for all primary and remedial cementing operations to assess risk, mitigation options and consequences, which are then discussed in a peer review setting. “One of the biggest changes the industry has seen the past few years is increased awareness of risks, with consideration of risk-based decisions and contingency planning,” said Joe Shine, cementing product line manager. “Some of the more important issues we’re looking at as we get into deepwater cementing are top-hole, or riserless, sections and subsalt environments, both of which present unique challenges. Often there are unknowns that are not accounted for in the pre-job planning phases that require us to proactively prepare prior to starting the well. That is where we build in the risk contingencies.”
From a technology standpoint, engineers at Baker Hughes are refocusing their efforts on cement design and methodology, examining what has been done in the past and where they believe the industry will be in five years. For example, the company is working on a new foamed cement system, which adds nitrogen or other compressed gas to the cement matrix to give it the necessary properties to best meet well objectives. The new system is expected to have significant applications in the GOM and other sedimentary basins around the world.
Foamed cement specifically addresses shallow hazards by counteracting the hydrostatic pressure loss that initiates water or gas flow, maintains internal pressure and prevents volume loss as the cement transitions between the liquid and set states. “We’re not only looking at the type of cement but ways to better technologically deliver the product at the wellsite,” Mr Shine said.
Baker Hughes also has developed a self-sealing cement that has the capability to seal a micro-annulus or fissure within the cement sheath itself. Another product being advanced is a synthetic cement, commonly known as a non-Portland cement alternative, to provide better wellbore integrity solutions. “Processes such as temperature and pressure changes affect cement, so with this alternative we’re trying to develop a product that will provide more durability for the life of the well,” he explained.
Mr Shine recently presented a paper, SPE/IADC 163446, on Baker Hughes’ new cement simulator, which uses software to design cement placement, at the SPE/IADC Drilling Conference and Exhibition, 5-7 March in Amsterdam. “We now have advanced modeling software that can account for non-aqueous fluid compressibility behavior and losses before we actually provide the cementing service,” he said.
Going forward, he sees limitations in the availability of specialized bottomhole testing equipment for deeper, hotter and more unknown conditions. “Attaining the temperatures and/or pressures required in these wells is not always achievable,” he said. “Testing is limited to a point, presenting a technology gap that many in the industry have determined needs to be addressed.
“As service companies strive to bridge such technology gaps in the critical deepwater cementing sector, we are taking a holistic approach, looking at the overall delivery of services, including the pre-job, execution and post-job stages, at the well,” he continued. “Everything is more comprehensive, and there is more quality assurance driving the process.”
EverCRETE, FUTUR, FlexSTONE, DeepCRETE and DeepCEM are marks of Schlumberger.