Automation of surface equipment, dissolvable and shorter plugs push efficiency of fracturing operations
Increasing use of water due to longer laterals and higher stage counts are also driving demand for more cost-effective water management solutions
By Kelli Ainsworth, Associate Editor
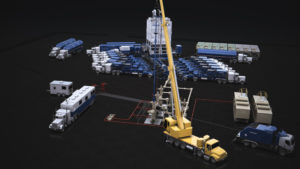
As operators push the number of stages per well to upwards of 75 or even 100 in some plays, they’re also demanding step-changes in the efficiency of hydraulic fracturing technologies and equipment, including associated technologies like water management systems. A significant area of focus has been on reducing plug mill-out time, with more dissolvable technologies coming to the market, as well as the development of shorter plugs with less material to mill through.
Technologies are also emerging to automate the surface operations of hydraulic fracturing. While the industry has made significant progress in automating the drilling process, less effort has gone toward automating completions. That tide is now turning.
“We are giving much greater focus to our surface delivery work flows and technologies in order to maximize efficiency and to reduce completion costs for operators,” Teoman Altinkopru, VP of Marketing and Technology, Well Services, Schlumberger, said. Later this year, the company plans to commercialize its Automated Stimulation Delivery Platform after nearly four years in development.
Water management also remains a major concern, particularly as the volume of proppant pumped into each well increases. “Depending on the data you’re reading, there’s three or four times more water being used now than there was a year or 18 months ago,” said Danny Jimenez, CEO of Gradiant Energy Services (GES), a provider of water treatment technologies.
To address the industry’s water challenges, technology companies are developing proppant transport systems that are compatible with high-salinity water, allowing more produced water reuse, along with systems that can reduce or eliminate the need to dispose of produced and flowback water.
In this article, DC speaks with Schlumberger, Weatherford, Terves, Fairmount Santrol and GES to hear how these challenges are being addressed.
Automating surface equipment

Field testing for Schlumberger’s Automated Stimulation Delivery Platform is continuing through Q2 2017, with full commercialization expected in Q3. The system has been designed to streamline surface operations and reduce HSE risks at the well site, Mr Altinkopru said.
The platform consists of three main components: four bulk delivery silos for storing proppant materials, a process trailer for hydration and blending, and an automated missile for pumping the proppants. All components are operated from a central control cabin. Sand-hauling trucks pull up to the delivery silos and open a door on their undersides to release their contents onto a belt that can offload a full truckload of sand in 15 minutes. “Instead of blowing proppant into the delivery trucks into the silos with a pneumatic system, we use gravity,” Mr Altinkopru said. “The dust generated offloading proppant into the silos is significantly reduced.”
Because the trucks don’t have to be connected to the delivery silos in any way, any type of delivery truck can be used. “And because it’s offloaded by gravity, we are not impacted due to differences between grain haulers.”
Each delivery silo is built with two individual compartments, which allows for the storage of multiple varieties of proppant. Each platform’s four silos can hold a total of 1 million lb of proppant. To prevent human errors associated with the manual tracking of proppant inventory at the frac site, load-cell sensors are built into each compartment to measure the volume of stored proppant. Measurements are automatically displayed in the control cabin. “It’s a next step of accuracy that you can provide when you are moving around millions of pounds of proppant and sand,” he said.

The second component, the process trailer, serves both as a hydration module that converts guar to hydrated gel and as a blender that mixes the hydrated gel with proppant. Sitting under the delivery silos, it can blend and pump up to 120 bbl/min of fracturing slurry. In addition, the trailer serves as a hydration unit and blends dry polymer powders with water to form an aqueous gel. Combining the blending and hydration functions into one piece of equipment reduces the footprint at the well site, Mr Altinkopru said. “The process trailer is able to replace two pieces of conventional equipment on location so we greatly reduce the number of drivers and the number of people that we take to location,” he added.
The trailer is fully redundant and equipped with a health monitoring system that allows for preventive maintenance. For instance, during one deployment, the temperature sensor on the mixer shaft indicated a potential failure trend. This allowed the component to be replaced prior to failure, Mr Altinkopru said.
The automated missile is the third component of the platform, which provides flow into the well. It has a maximum pressure rating of 15,000 psi and a maximum flow rate of 80 bbl/min. Valves can be opened and closed from the control cabin.

The ability to remotely operate this high-pressure equipment means employees do not have to work in a high-pressure area, improving HSE. Intelligence has also been built in to the system to prevent pumps from accidentally activating if a valve is closed. “This reduces human errors. Further, there’s no need for any personnel to enter the high-pressure area during the job,” Mr Altinkopru said.
Schlumberger began developing the system in 2013, and field tests commenced in late 2015. So far, the system has been deployed in 96 wells on 23 pads in South and West Texas, for a total of 11,640 hours in service. In that time, the platform has managed 844 million lb of proppant, according to the company.
Reducing mill-out times
According to Weatherford, 85% of hydraulically fractured wells worldwide still use the plug-and-perf method, due to the ease of deployment and the lower costs involved. This means that, as the number of stage counts increases, more frac plugs need to be run and milled out. “We’ve constantly been enhancing our plugs to achieve more efficient mill-outs,” Chad Picciotti, Global Product Line Champion-Well Completions for Weatherford, said. This has been done primarily by reducing the amount of material, especially metal, that has to be milled through. “We’re decreasing the length of the plugs and the amount of metal that we have on our plugs,” he said.
In early 2016, the company commercialized the Shorty composite frac plug in 4 ½- and 5 ½-in. sizes, rated for 250°F and 8,000 psi. It has a similar chassis, upper slip and cone to the company’s TruFrac and FracShield plugs but is differentiated by its small size and wicker-style slip. Since the Shorty plug’s original launch, Weatherford has also developed higher-pressure, higher temperature versions of the plugs, rated for up to 300°F and 10,000 psi.
Because of the plug’s shorter design, it has less material to mill out. The 4 ½-in. version is 19 in. long, making it 3 ½ in. shorter than the company’s other 4 ½-in. plugs, while the 5 ½-in. version is 21 in. long, about 4 in. shorter than its other 5 ½-in. plugs, Mr Picciotti said. The plug can be used in any plug-and-perf application. “It complements our TruFrac line of full composite plugs as an economical option with reduced length,” he added.
In 2016, the 5 ½-in. Shorty plug was run on a four-well pad in the Eagle Ford. A total of 24 plugs were set in each well. The plugs were milled out using coil with a reverse clutch mill. On average, each plug took 8.5 minutes to mill out. The 5 ½-in. Shorty was also deployed in a 105-stage well in the Permian in January. In this well, plugs were milled out using a roller cone bit. The average mill-out time was 12 minutes. That compares with an industry average per-plug mill-out time of 15 to 20 minutes, according to Mr Picciotti.
In addition to the Shorty, Weatherford is developing its version of a dissolvable frac plug. The EliteFrac plug is made of a degradable metal that dissolves when exposed to potassium chloride (KCl). Depending on the well’s temperature and the KCl content in completion fluids or produced water, lab tests have shown the plug will fully dissolve in two to three weeks. “We anticipate using this plug primarily for long-reach laterals at the toes of the well,” Mr Picciotti added. Utilizing dissolvable plugs eliminates the need for milling out plugs entirely, saving the operator time and avoiding the risks associated with milling out long laterals.
The EliteFrac plug, which is rated for 250°F and 8,000 psi, is currently in field trials.
Dissolvable materials
As dissolvable technologies carve out a niche in the frac market, equipment manufacturers will need access to improved materials. Terves, a materials science company that produces engineered composites, is releasing a new version of its TervAlloy dissolvable magnesium alloy to equipment manufacturers so they can conduct design and qualification testing. The TervAlloy MMC is not fully commercial yet, “but it is in prototyping for companies interested in incorporating it into their design,” CEO Andy Sherman said. The material can be used in bridge plugs, frac balls and sliding sleeves.
The MMC incorporates ceramic particles to increase its hardness, thereby improving its ability to withstand erosion when sand and proppant is pumped. “Magnesium itself is fairly soft, so the MMC provides erosion resistance, wear resistance and hardness,” he said.
Terves has also been developing fully dissolvable polymers. Last year the company released the Response Element DE 50, which is already being used in rubber elements in dissolvable frac plugs. “The rubber sealing elements in the early dissolvable plugs remained in the well and didn’t dissolve,” particularly in wells with temperatures under 90°C, Mr Sherman said. “They formed a sludge, which can reduce flow after putting the well online.”
The Response Element DE 50 allows for polymer elements that can dissolve at temperatures between 50° and 70°C over a period of two days when the dissolution is triggered by fluids. Terves is currently working to develop another version of the Response Element that can work in temperatures between 110° and 150°C. These temperatures are commonly seen in the Middle East and in the Montney play in Canada. The current iteration would dissolve too quickly at these higher temperatures.
“If they dissolve too fast, they don’t seal and operate reliably. They need to be able to hold the pressure for the four to six hours typically needed during pumping,” Mr Sherman said. “But then you want them to go away so you can get the well into production as soon as possible.”
Improving proppant transport
Handling the produced and flowback water from hydraulically fractured wells continues to be a challenge. Such water can be expensive, and service and technology companies continue to seek solutions that allow operators to reuse more and more produced and flowback water. Some solutions are allowing operators to frac with whatever water they have available, such as high-salinity water.
In January, Fairmount Santrol launched the Propel SSP350 proppant transport technology. It is an expansion of Fairmount’s existing Propel SSP proppant transport technology, which was launched in January 2014. The original technology could only be used with fresh water containing a maximum of 5,000 ppm of total dissolved solids (TDS). The new version can be used with water that has more than 350,000 ppm TDS.
“That’s 10 times the salinity of seawater,” said Brian Goldstein, Director of Oil and Gas Technology Solutions. ”That gives operators the ability to work in most produced waters that have been observed in the oil and gas industry, regarding salinity.” Because the system is tolerant of very high-salinity water, produced water does not have to go through desalination before it can be used with Propel SSP 350.
“The significance there is the ability to reuse both your produced water, as well as flowback water, with the least amount of treatment to be able to pump back into a well.” Operators may still need to treat water to provide microbial control and to remove oil and suspended solids, however.
The proprietary chemistry of the Propel SSP 350 is significantly more cation-tolerant than its predecessor. “You have a lot of cations in water, which is what creates the TDS and the hardness,” Mr Goldstein said. The technology has been tested in the Permian, although results are not yet available. Additional field trials are being planned for the Marcellus and other plays. “The Permian and the Marcellus are two natural fits because those are two markets with fresh water constraints, albeit for different reasons – Permian due to source water quality and Marcellus due to water management costs.”
Like the original Propel SSP technology, the produced water version is a residue-free hydrogel coating that surrounds proppant grains and swells to suspend in water. This allows the proppant to uniformly fill the entire height and length of a fracture. Proppant settling is one of the biggest challenges operators must overcome when designing a frac treatment, Mr Goldstein said.
“If the proppant settles and plugs the wellbore, you have a costly operational challenge. If it settles in the fracture prematurely, you’re missing an opportunity to fully contact the formation for maximum well productivity,” he explained.
Often, operators choose to use a fine mesh proppant, such as a 40/70 or even a 100 mesh, to overcome settling in slickwater. However, this often results in operators sacrificing proppant strength. Another solution is to pump at higher rates, but that requires having more pumps at the surface, which means increased costs and increased space needed at the well site. “With Propel SSP 350, in addition to any mesh, any pump rate, any proppant substrate, we now can pump in any water,” Mr Goldstein said. “If you are able to design your wells based on the reservoir conditions versus your operational limitations, you’re going to have a much better outcome at the end.”
Saving water, saving money

In the Permian, along with the estimated 2 million BOED oil production comes approximately 11 billion bbl/day of water produced, Mr Jimenez of Gradiant Energy Services said. “Everything is pushing the effort to recycle more of this produced and flowback water so that no fresh water is needed for new fracs,” he added.
Citing conversations with operators, GES estimates that it costs operators between $0.28 and $0.60 per barrel to source fresh water, between $0.30 and $0.70 per barrel to transport water, and between $0.30 and $1.25 per barrel to dispose of it.
In Q3 2016, GES deployed its Carrier Gas Concentration (CGC) technology in a pilot project in the Marcellus in Northeast Pennsylvania. The CGC uses evaporation to treat produced and flowback water with TDS levels up to 200,000 ppm. “In places like the Marcellus, there’s no place you can inject produced water into a disposal well. You have to truck the water out of the area, which can be expensive,” Mr Jimenez said. Oklahoma is another potential market for the technology, due to seismicity concerns around water disposal.
After treating produced or flowback water with anti-scalant, the CGC system uses field gas to heat water in a boiler and through a heat exchanger. The produced or flowback water is then passed through a bubble column humidifier, where it flows down into several stacked bubble trays. Ambient air is used as a carrier gas and is pushed up through the bottom of the bubble column. This creates microbubbles in the water, which allows for heat transfer in suspension through the surface of the microbubbles. The airstream is then saturated with vapor, which is released safely into the atmosphere. What’s left of the original produced or flowback water is a concentrated brine that can be used for drilling and completions activities.
The system has been designed to rig-up and rig-down within three days, according to Mr Jimenez. Setup involves filling the boiler with fresh water, hooking up the influent and effluent water storage units, generator hook-up and pump housing hook-up. During the pilot project in the Marcellus, which concluded in Q1 2017, the system treated 500 bbl/day of water, resulting in an estimated 45% cost reduction for the operator. For future deployments, GES says it is planning to expand the system’s capacity to 1,000 bbl/day.
Another challenge around water management in hydraulic fracturing operations is bacteria treatment, as bacteria in water can cause reservoir souring and corrosion issues. GES first deployed its Free Radical Disinfection (FRD) technology in mid-2016 in the Permian. Since then, the technology has been in continuous use for several operators in the area. GES treated 2 million bbl of water using this system over the course of 2016 and has already treated nearly 3 million bbl this year.
The technology is used for on-the-fly disinfection prior to hydraulic fracturing. Water is pumped into the FRD trailer at a rate of up to 120 bbl/min; this rate would allow for 500,000 bbl of water to be treated in approximately three days. Fresh water and salt are blended and then passed through an electro-chemical cell to create a mixture of oxidants, namely bleach and hydrogen peroxide. The bacteria and other contaminants are oxidized and removed. The disinfecting solution is created on site within the FRD trailer and does not require any chemical handling, Mr Jimenez said.
Initial results from the system’s application in the Permian indicate that no bacteria were found in the water even after two weeks, he added.
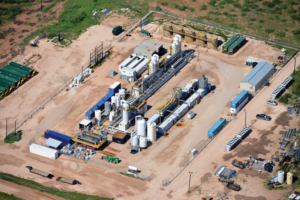
The company is also building and deploying more of its Selective Chemical Extraction (SCE) facilities for water recycling. Two are already in operation, with six to eight additional units coming this year. “It’s probably the service line that has experienced the highest demand,” Mr Jimenez said. “The rig count is increasing, and frac demand for water is high. Operators are looking for a recycling solution.” The bulk of this demand is coming from the Permian, but GES is also seeing opportunities in the Rockies, Oklahoma and the Bakken.
The technology, originally launched in 2013, was designed to provide customized water treatment based on the quality of the produced water and the operator’s specific water quality needs. “Optimizing the amount of chemicals used to treat produced water can eliminate unnecessary chemical usage and lower treatment costs,” he added.
The SCE units can treat 10,000 bbl/day of water. Produced water is piped into the SCE system, where it first passes through an oil-water separator. The oil-free brine then moves to a chemical reaction chamber, where the needed chemicals are added. After chemical treatment, the water is sent to a clarifier, which removes solids from the water. The water is then pH-treated while the solid slurry that was removed is pressed into a cake that can be sent to a landfill. DC
Carrier Gas Concentration, Free Radical Disinfection and Selective Chemical Extraction are registered terms of Gradiant Energy Services.