Automated steering system aims to improve directional drilling across multiple US onshore basins
To shorten learning curve when deploying system in new areas, drilling ‘recipes’ were created to capture best practices from different basins
By Stephen Whitfield, Associate Editor
In recent years, automated directional drilling solutions have become much more acceptable to operators seeking to improve performance. However, these systems are often primarily configured for basin-specific challenges. Such configurations have helped companies like Nabors to deliver high performance, but the company also recognizes that developing a system to work across multiple basins could lead to a step change in directional drilling performance.
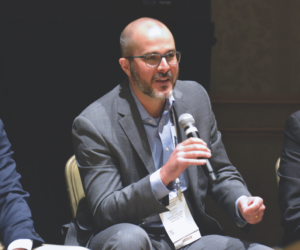
At the 2020 IADC/SPE International Drilling Conference in March, Scott Coffey, Technology Manager of Drilling and Automation at Nabors, discussed the implementation of a system that automates slide drilling to improve rates of penetration and the work that was done to configure it to work across different basins. Key to this achievement was the development of drilling “recipes,” or complex aggregations of sequences and tasks that can be adapted to the differing conditions of given basins.
Automated slide drilling
Slide drilling is a practice in which a steerable bottomhole assembly with a bent housing and bit, driven by a downhole motor, is used to deviate the wellbore while the drill string to surface is stationary. The automated system replaces the slide drilling execution sequences traditionally managed by a directional driller on location.
With an automated system, “we’ve got granular control of a lot of small functions in the slide drilling process,” Mr Coffey said. “When we take away the variable that is human execution of a slide, we can better assess performance. We can attribute performance differences between basins to differences in equipment.”
If the best practices for slide drilling among directional drillers within a basin are codified within the automated system, it is simpler to replicate those best practices on other rigs, he added. This effectively removes much of the operational variance that comes from humans interacting within a drilling system.
Automated systems are also capable of consuming and acting on new information much faster than a human, so they can maintain more precise toolface control throughout a slide. With that improved toolface control, the driller and directional driller can spend more time focused on optimizing drilling parameters for the highest ROP.
The primary challenge in implementing directional automation, however, is the translation of human decision making into computer-executable code, Mr Coffey said. Humans consciously understand and adjust to various dynamic operational factors, but an automated steering system needs to identify, comprehend and respond to those factors in order to replicate human behavior. In addition, experienced directional drillers can forecast future downhole behavior based on unclear or incomplete information, and they can develop a reasonable action plan based on that forecast.
“The translation of that human decision making – the experience, the intuition that a directional driller has – is exceedingly difficult,” Mr Coffey said. “This makes sense, because the role of a directional driller is very dynamic. They consume a lot of information from a lot of different sources, and they have to do a lot of forecasting and planning ahead.”
While there is no easy software replacement for human intuition, control systems are good for performing tasks that humans find difficult, like consuming large quantities of data in a short time frame and making quick decisions based off of that analysis.
Cross-Basin Configurations
The automated steering system discussed in the presentation relies on complex task automation, configurable activity sequences, and adjustable responses to drilling parameters to automate the process of a slide. The system was designed to accommodate a wide range of drilling conditions and operations and to minimize the need for software redevelopment when piloting the system in a new field. It was not configured in the field but rather by office-based product experts, who developed aggregations of interdependent operating conditions, activities and sequences.
These aggregations, also known as “drilling recipes,” had to be optimized based on many factors unique to an operation, including wellbore geometry, planned bottomhole assembly, planned drilling parameters and measured depth.
The system required numerous sub-features to be configured in advance of the automated slide drilling operation, in order to match the performance of the system to expected operating conditions in a given basin. Typically, a series of recipes were planned for each operation by interval and by depth, remotely deployed to the rig control system and activated for use as required at a planned depth or based on drilling conditions that were encountered as the well was drilled.
“These recipes really are the DNA of the automation,” Mr Coffey said. “They are what drives the behavior of the system. The configuration of these recipes is really what allows the system to be successful.”
He presented a case study in which drilling recipes were developed for an automated directional drilling operation in the Permian Basin, translated to another operation in the Bakken, and then brought back to a different installation in West Texas. The study intended to determine whether experience with the automated system in one basin could help users succeed in different areas.
Prior to the initial implementation in West Texas, engineering teams conducted an offset well analysis and reviewed best practices with local directional drillers. They focused on the quantity of reactive torque to initiate slides, effective manual steering methods and typical drilling parameters. The typical manual offset curve ROP performance ranged between 30-50 ft/hr, a speed that enabled directional drillers to maintain enough toolface quality to complete most curves in one run.
The resulting configuration allowed the automated system to execute slides with tighter toolface control than typically achieved by human directional drillers, thus allowing the driller to use higher drilling parameters to improve ROP performance for the automated system, compared with manual slide drilling.
The engineers then deployed the automated system in North Dakota, with a pre-deployment engineering study indicating the recipe revisions needed to replicate the quality of steering achieved in the Permian. The study identified several parameters within each recipe requiring revision, including:
- The frequency and magnitude of steering corrections;
- The system’s response to differential pressure changes;
- Steering behavior at a higher sliding ROP; and
- The acceptable tolerance around the target toolface.
The Bakken operation saw increased ROP performance for the automated system with these revisions, as did the next deployment in West Texas. The study showed that operational experience within the system was additive: As the system gained experience working in one basin, it was easier to adjust the recipes to optimize ROP performance in another basin. DC
For more information, please see IADC/SPE 199605, “Achieving Automated Directional Drilling Across US Onshore Basins,” presented at the 2020 IADC/SPE International Drilling Conference, 3-5 March, Galveston, Texas.