Value-driven innovations will stand out amid focus on fiscal caution, efficiency improvement
Expanding adoption of AI, automation can lead to additional gains, but new ways of working may be needed around sharing of risk, reward
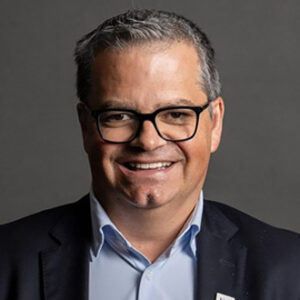
By Stephen Whitfield, Senior Editor
Alen Corak is VP of Well Construction Technology Delivery at SLB.
One of the big messages we’ve heard from industry leaders post-COVID is the need to create a more sustainable business environment where E&Ps and service companies deliver value to shareholders. Why do you think this is going to remain a priority heading into 2025, and how has this environment of capital discipline affected the way SLB operates?
Yes, capital discipline will be front and center when it comes to priorities in 2025, but it’s really nothing new. We’ve been very disciplined for several years now. At the end of the day, lower CAPEX availability is at the heart of the challenge. This means that we’re all going to collectively focus on making investments with a higher return. Specifically, for SLB, that means looking at digital solutions that will deliver improved and consistent results.
SLB is always trying to push the technological envelope in well construction, but doing that requires capital investments. How has that balance between discipline and innovation affected your business and the industry as a whole?
The industry can balance capital discipline with investment in new technologies by prioritizing value-driven innovations. These innovations will enhance efficiency, as well as reduce the total cost of ownership and carbon emissions. This involves leveraging partnerships, focusing on provider-agnostic solutions, and integrating digital solutions within a comprehensive digital ecosystem for better interoperability.
The perfect example of this is the Neuro autonomous geosteering system that we announced in December. That’s a system that dynamically responds to subsurface complexities to drill more efficient, higher-performing wells. It has already shown results – in Ecuador for our client (Shaya Ecuador), we had a total of 25 autonomous geosteering trajectory changes over a 2,392-ft lateral in an onshore well.
In this particular case, each decision cycle took only seconds to execute, and we were able to remain in the most productive layer of the reservoir. This well has now become one of the country’s best producers. This is what the future looks like.
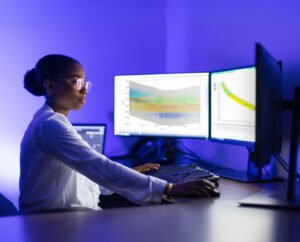
SLB is obviously working with E&Ps and drillers on trialing and running these digital solutions. How important is collaboration overall to innovating within this industry?
It’s very, very important. Collaboration with operators and with drilling contractors is crucial for driving innovation. Cross-disciplinary teamwork will help address pressing challenges and align efforts toward efficiency and sustainability. This can help us overcome historical silos and focus on common benefits, which can lead to more effective technology and business model advancements. We must acknowledge that no one company has all the answers, and we can only achieve maximum value by working together.
That’s interesting that you bring up silos, because there are some who would say that competition breeds innovation, that being too open isn’t necessarily the best thing. SLB does a lot of work with open-source and promoting an open ecosystem overall. What steps do you take when you encounter silos?
It all comes down to communication on the value drivers and, more importantly, what each company can bring to the table. We cannot operate as our own entities. We have to focus on our common goals and sharing value whenever possible.
With digital tools, our industry has traditionally been quite risk averse. As a result, we’re pretty slow when it comes to adopting these tools into our workflows. But as we start to see the improved efficiency, the improved safety and the overall cost reduction from digital solutions, that adoption is going to increase.
At the end of the day, we’re all looking to maximize returns, and that means we need to overcome some of these legacy system challenges by ensuring operability. Different skill sets will be required to do this, so we also need to invest in workforce training and enhance data management. We have to leverage advanced capabilities like LLMs (large language models) and GPT. We cannot do any of these until we break down the organizational silos.
How much enthusiasm are you seeing from drillers and E&Ps around adopting LLMs and generative AI into their workflows?
AI and automation are already transforming the world all around us. In our industry, we are transforming the role of the human and addressing personnel shortages by automating routine tasks and enhancing operations.
A lot of benefits can come from this, but perhaps we need to remind everyone what those benefits are. First and foremost, it’s a story of knowledge retention. AI has the capability to store and recall very detailed operational data, pre-surveying insights from experienced personnel.
It’s also a story of performance optimization, because AI continuously learns and suggests improvements for more efficient processes. It gives us consistency, because AI applies best practices consistently by reducing variability and enhancing quality. It helps to predict the maintenance we’re going to have – before issues occur. That allows for proactive maintenance, which then reduces downtime. Enhancing automation to cover routine tasks also reduces complexity and improves workforce efficiency.
In reality, we’re enabling the human on the rig to focus on performing higher-value tasks in a process. As an example, in cases of remote operations, we are reducing the need for travel, which enhances safety, provides a better work-life balance for people and reduces our carbon footprint.
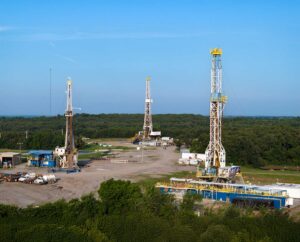
You’ve alluded to AI changing the role of the person on the rig. How dramatic of a shift do you see is taking place?
I think this next step change for improving rig safety, in particular, is really going to be around automation and reducing interactions with equipment and materials. We’re going to see a shift where fewer people will be required on a well site and where some of the more repetitive tasks are going to be done by machines. As alluded to earlier, this will allow people to perform the higher-value tasks that result in better outcomes and make our operations safer.
Sounds like you think automation and digitalization are the next step changes for safety on the rig. But do you see anything else pushing us forward in that area?
I think robotics will also have a role to play. We already have some examples of that, especially with the rig contractors. Innovation on that front will continue in the years ahead, but at the end of the day, technological innovation is at the heart of all this. So we’re going to have to work hand in hand to make sure that we are actually developing technologies that are going to bring the biggest step change in performance and safety.
It sounds like you’d agree that we are seeing an effective return on investment in these digital systems that we’re seeing on the rig. So what do you see as the things that will ensure even greater returns in the future? Are we getting everything we can get out of digital systems now?
We can push even further with data integration, data analysis and machine learning, so that we can see faster and more efficient drilling. These things are already revolutionizing drilling performance, and we can see examples where we use automation to optimize rig operations and reduce invisible lost time. This is a prime function for the Internet of Things, which is obviously a big story for the industry.
Then there is the use of AI and automation for well design, execution and placement. There is a whole series of technological advancements ongoing that improve their ability and robustness and improve telemetry, and there are technological advancements to optimize well designs and operational strategies, such as MPD and various integrated offerings. And I’ve already mentioned earlier how the predictive maintenance capabilities of these systems reduce unnecessary downtime.
In short, the industry has seen significant efficiency gains over the years, but there is potential to expand these even further. More importantly, rather than focusing solely on the time needed to drill a well, we also need to ensure that every well is placed in the most productive part of the reservoir so that it delivers optimum production. I also think that, as an industry, we need a different definition of efficiency going forward.
What do you mean by that?
Well, our ultimate customers, the operators, are in the business of production. I think we need to have more alignment on how we can help them get more production. Faster drilling time alone is not going to give us more production.
So how close are we to seeing that kind of alignment? Can these bridges be crossed easily, or are they very difficult to cross?
I think these are the bridges that we’re not crossing today, but they can be crossed. The service companies often have performance contracts, while the rig contractors work on dayrates.
Obviously, these are two different things. I think the incentives should be aligned for all parties to work toward the same goal and share in the value created. If we do that, we’ll continue to push for innovation simply because we’ll all be equal owners of the risk and the reward.
At SLB, we see other benefits to that kind of balance, such as improved HSE performance. But first we have to work together as an industry to get a better commercial environment.
So would you say the dayrate model is obsolete, and performance-based contracts are the way to go? Or do you think that we need a third way?
That is a tricky question. I think we all need the mindset of creating more value and developing a model that allows us to share more of that value for the benefit of all. That means we should be willing to try different models, whatever they might be, to create win-win outcomes for all of us.
You talked about performance. Do you think that there’s a point where we will see diminishing returns as we push for higher ROPs and shorter drilling times? Are we getting close to the limit of how fast we can drill a well?
I think we should first recognize that the industry has come a long way when it comes to drilling efficiency. Let’s just look at the example of drilling laterals in the US. In the Midland Basin in particular, the average lateral length has increased from 3,000 feet to over 10,000 feet since 2010, and the drive toward even longer laterals continues.
In my opinion, this trend is going to continue because operators will continue to optimize drilling and completion strategies for efficiency and cost effectiveness. When you look at these 3-mile wells, they actually show economic advantages with breakeven prices that are approximately $4 per barrel, which in turn drives the cost savings per foot by about 20%.
This can only be achieved through continued investment in technology in order to improve the tool design and ruggedness. And this is really something that SLB is investing heavily in, because we want to continue pushing the boundaries.
Just to quote one example, very recently we helped a major IOC drill its longest well in the Permian – it was 20,500 feet in total, or almost a 4-mile lateral – in a single run. This was enabled by the PowerDrive Orbit G2 RSS, utilizing our Neuro autonomous directional drilling system. Overall, our ambition is to continue pushing these boundaries, and technology is the answer to get there.
You brought up improving tool design. We’re hearing E&Ps and drillers talk about pushing past the 3-mile lateral and drilling 4-mile laterals or longer in a single bit run with regularity. Do you think our current downhole tools are equipped to enable such efforts? If not, how far away are we?
First and foremost, a lot of homework needs to be done ahead of time. You need to have a very detailed reservoir characterization for the optimal lateral and well placement. You need to have advanced well designs in order to be able to optimize the wellbore trajectory.
It’s also very important to have enhanced rig capabilities in order to generate the increased power output that you need to drill these laterals. This may mean installing more powerful top drives. You may need higher pressure mud pumps. You may need higher torque wrenches. You need to have a very robust data analysis system and the ability to make real-time adjustments.
On top of that, the equipment has to be able to survive downhole. This is where the efforts around tool redesigns and ruggedization really come into play. These are the key things that are going to drive the ambition for 4-mile-plus laterals in the future. I think they are very much within the realm of reality.
You think we’re going to start seeing 5-mile laterals in a single bit run happening regularly in the near future?
I would not discount that completely. It is in the realm of possibility. DC
Well said—I couldn’t agree more. I’m also a strong advocate of value-focused decision-making. The gap between customers and service providers often lies in how value is perceived and measured. A business is generally willing to pay more if it leads to a higher ROI, but outdated and poorly designed KPIs can obstruct value creation. After all, what’s the point of drilling the fastest well if it fails to meet production targets? When companies engage in this conversation, it’s a strong indicator of their maturity—because it requires input from experienced professionals across different disciplines (service and operators). to capture value. How many O&G companies have this level of flexibility, with engineers able to understand the impact of their work across multiple disciplines? My guess is not many, so what about a system that can integrate all the multidisciplinary aspects of value creation?