Industry builds circular water economy as it leans into recycling and reuse
Water management companies investing heavily in treatment technologies and transport infrastructure as E&Ps continue to shift away from disposal wells, reduce reliance on freshwater
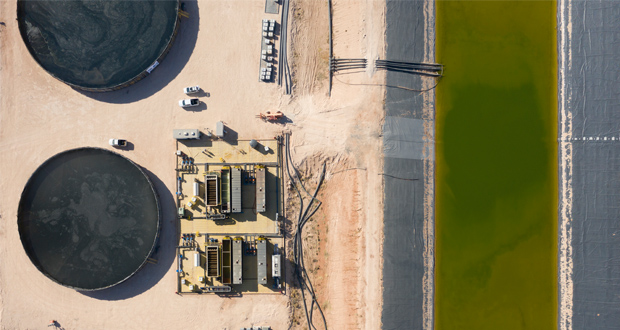
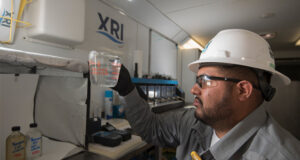
By Stephen Forrester, Contributor
The use of water in oil and gas operations has long been necessary, but water scarcity in many parts of the
world — and growing scrutiny on environmental and social considerations for energy companies — has led the industry to refocus its attention on minimizing freshwater use and finding better ways to work with produced water sourcing and delivery. Fortunately, the industry is well-positioned to take advantage of advanced technology and engineering solutions, which are already a critical piece of their operational success, to improve water sustainability and optimize water efficiency. In doing so, there is outsized potential to strengthen the industry’s public perception and relationship with stakeholders.
Eliminating freshwater use by expanding water recycling
XRI, a full-cycle water management and produced water midstream company founded in 2013, began installing its first long-distance buried pipeline infrastructure in 2014. In the years since, the company has seen broad growth within the water management sector, said Vice Chairman and Chief Sustainability Officer John Durand. “We’ve been watching as the market has transitioned away from water management as a function largely handled internally by E&P operating companies,” he remarked.
For the industry to continue to advance, Mr Durand said it must wean itself off freshwater. “After the difficult drought situation in West Texas from 2010 to 2015, there surprisingly were not a lot of people dedicated to using non-potable water to serve drilling and completions,” he explained. XRI, however, maintains its philosophy that the E&P sector must transition away from using freshwater for completion activities.
“We believe that the future of produced water and the handling of produced water, in the Permian Basin and elsewhere, must lie in recycling and reuse,” he explained. “There is simply too much water resource being produced, between produced water and flowback, to not lean into efficient and cost-effective water recycling and reuse at scale.” This means a step-change was needed to build a circular water economy based on recycling and reuse, where an injection well would only be the last resort.
To help the industry achieve that change, XRI acquired Fountain Quail Water Management in 2019 and integrated that company’s treatment and recycling capabilities into its existing water distribution midstream infrastructure. Additionally, the company now has approximately 450 miles of permanent, large-diameter buried pipeline infrastructure throughout the Midland and Delaware Basins.
In February, XRI also brought into service the Evolution Pipeline System in the Midland Basin. The system, which is underwritten by long-term contracts with Chevron, XTO Energy and Pioneer, is designed to alleviate overpressurization of deep disposal formations and mitigate seismicity risks throughout the basin. It maximizes produced water recycling and reuse by enabling E&P companies to tap into XRI’s interconnected water distribution networks and large-scale recycling and water treatment facilities.
Establishing an extensive network of pipelines and treatment facilities is a key step to creating that circular economy of water management, which can help to reduce the need to draw from freshwater aquifers.
“What the Evolution Pipeline System allows XRI to do is move approximately 500,000 barrels of water per day from the central Midland Basin — where there remain seismic concerns and defined seismic response areas — down to Reagan County and Uptown counties, where XRI owns and operates full-cycle water infrastructure in the southern portion of the Midland Basin,” Mr Durand explained. “When we move water to those counties, where there’s been minimal disposal injection historically, we are transporting significant water quantities up and down XRI’s pipeline infrastructure, treating the produced water and moving treated recycled water to operators who want to minimize or avoid disposal throughout the basin.” The company is currently developing a similar set of projects in the Delaware Basin.
Further, it also hopes to provide financial incentives for E&P companies to move away from water disposal, by providing treated produced water for its operator clients at a lower cost per barrel than the injection of water into disposal wells. “At XRI, we have always viewed disposal of water as a last resort only, and that philosophy and practice is not going to change,” Mr Durand stated. “It is critical that industry continues to embrace recycle and beneficial reuse as technologies continue to emerge.”
Today, XRI handles almost 1.5 million bbl/day of produced water, which is treated at one of 30 water recycling facilities throughout the Permian Basin. “Disposal avoidance will continue to gain importance as a key metric of success,” he said.
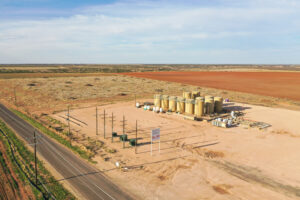
Disposal wells will likely still be important in foreseeable future
Gravity Water Midstream is the water management business of Gravity Oilfield Services, which also runs a power rental solutions business. Its water management solutions include high-volume sourcing, pipeline transport, reuse and disposal through a network of fluid logistics assets and infrastructure. That includes fresh and brackish water storage pits, produced water gathering and freshwater sourcing pipelines, and saltwater disposal wells.
The company owns almost 300 miles of pipeline, 53 saltwater disposal wells, and 12 fresh and brine water facilities with over 6 million bbl of storage capacity. Gravity also has multiple produced water recycling assets, some of which are mobile and can be moved around within its system based on E&P activity.
The business is operated in three parts, said Trace Hight, Chief Commercial Officer of Water Infrastructure. The first is a sourcing segment that delivers frac water to the field; the second focuses on gathering produced water into a disposal network; and the third is a produced water reuse business. It’s the reuse business that is growing strongly, he said, with E&P customers requesting to recycle more of the produced water that Gravity gathers before treating and transporting it back to the field.
In fact, that reuse business now constitutes more than half of all sourcing the company does. Year to date, 53% of the water the company has provided for hydraulic fracturing has been gathered and recycled by Gravity within its own systems before being piped back out to the field.
The company says it is also working to maximize water usage between operators. “If we have additional water volumes in our systems where we can identify a beneficial use for that water with other customers, we will move those volumes to them instead of disposing of the water,” Mr Hight explained. “We are always trying to optimize that water within our systems before running out of options and having to inject it back into the formation.”
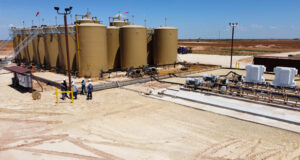
Still, Mr Hight said he believes disposal wells will continue to be important for the foreseeable future. “Injection back into the formation is sometimes the most cost-effective solution for this water,” he noted. “With something like evaporation, for example, we can’t come close to managing the barrels we process each day. The more reuse we perform for our customers, the less freshwater that has to be pulled out of the ground for a hydraulic fracturing job or injected back into the ground. This is a win-win for everyone.”
This doesn’t mean that the industry shouldn’t continue to examine beneficial reuse for produced water, a practice that is still in its early stages. “We continue to look for other ways we can use this water that are beneficial to all stakeholders,” he explained. “Can we, for example, treat the water sufficiently, recycle it and use it for irrigation for farming? As we look at droughts, water shortages and population growth in Texas, can we use this water to help with the state’s water problems?”
A willingness to invest will be critical, as will open-mindedness to looking at the water management discipline differently. “We need to find those opportunities to run pilot projects to fully gauge the impact and long-term viability of beneficial reuse,” he remarked. “It will be difficult to determine the economics of transporting the water from where it’s at to where it may be beneficially reused, and which party or parties are able to bear that financial burden.”
The key for now, Mr Hight concluded, is finding a balance that allows E&P companies to advance sustainability while achieving their economic goals — mostly through lowering their drilling and completion costs — and rising to meet the ESG mandate of creating positive impacts in the communities where they are active.
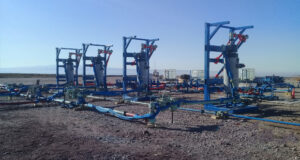
Integrated water management process
TETRA Technologies, an energy services and technology company, believes that water management in the upstream oil and gas industry requires an integrated solution uniting capabilities in sand management, automated water treatment and recycling, and water transfer.
One of the company’s patented technologies for water management is the TETRA SandStorm, an advanced cyclone technology that separates the solids and sands from the fluids during flowback. The proprietary design provides centrifugal action to accelerate and capture smaller particles while remaining under erosive velocities of the multiphase flow, with no flow restriction. Sand in the flow stream has long been an industry concern, as it can cause damage to everything from the casing to downhole equipment and even to downstream facilities, resulting in potential loss of or delay in production. The technology is designed to increase the frac sand and solids capture with higher efficiency than traditional sand separators and cyclonic sand traps. It also captures much smaller particles, down to lower-single-digit micron size.
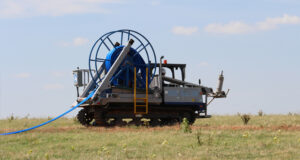
“We’re eliminating over 99% of the sand and proppant that’s coming back from these produced wells using the TETRA SandStorm system,” explained Jon Malone, Director of Business Development. “This has a great benefit for our customers because, by significantly reducing that sand content, we’re effectively eliminating the risk of it damaging their production and topside equipment.” Further the system can be automated through a series of values and chokes to reduce personnel exposure and HSE risk by reducing the need to manually disconnect components and clean them.
Another critical step of the integrated water management process is water reuse or recycling, which involves treating the produced water to a certain key performance indicator so that it can be used during completions and hydraulic fracturing operations. Because of the industry’s need to reduce freshwater use and the wide variance in water quality and consistency across subsurface saline water, produced water and effluent water, the company has seen substantial growth in this business. In fact, it hit a milestone of 8 billion gallons of treated and recycled water within 2022.
One technology that recycles and treats the produced water is the SwiftWater Automated Treatment system (SWAT). It encompasses a combination of technologies and processes, including automated chemical injection into the influent produced water stream; a clarification process that uses dissolved air flotation technology to remove suspended matter from the water; and a low media consumption filtration technology that polishes the water.
Once the produced water has sand removed and is treated, the company looks at how to transfer the water most effectively from the reuse facility to the completions site. Its TETRA Steel, a double-jacketed lay-flat hose that was introduced to the market in 2012, has a higher pressure rating than that of conventional lay-flat hoses to enable a faster rate of water transport.
“TETRA Steel lay-flat hose was our entrant into that premium product space, as we saw that the industry was transferring more and more water via lay-flat hose versus buried pipeline infrastructure,” Mr Malone explained, noting the HSE benefits for operator personnel by eliminating the need to bury pipeline in the ground.
The company is also working on new upgrades for the TETRA Steel hose to make it lighter and to make its couplings more resistant to corrosion. Additionally, construction of the hose material will be more robust and resistant to wear, Mr Malone said.
“With more water being moved through lay-flat hose, we see that market growing, so we want to ensure we provide a technology that reduces operational and environmental risks for our customers.”
The final piece of the puzzle is automation. The company has a web-based real-time monitoring and control system called BlueLinx that customers can use to view their treatment and recycling operations, providing immediate insight into chemical processes and quality objectives. It is also used internally to monitor flowback operations and sand management for produced water recycling and treatment, as well as automated pumps that transfer water through the lay-flat hose.
“All of that is integrated into the system, which is allowing operators to reduce safety risk and the occurrence of service quality errors,” Mr Malone said.
BlueLinx will, for example, synchronize with the hydraulic pumps that are delivering water along the length of lay-flat hose, telling the pumps when to shut down if there are issues and optimizing individual pump performance for fuel consumption.
Mr Malone highlighted that TETRA is working on integration with other companies’ systems and equipment, like water transfer pumps and valves used for emergency shutdowns, especially as operators look to bring disparate third-party service and technology providers’ offerings into their own internal systems.
The future of water management for TETRA, Mr Malone remarked, will involve the use of more and better technology solutions to ensure that more rigorous operational and financial performance metrics can be met. In addition, there will be nascent areas of innovation related to achieving ESG objectives.
For example, the company has been vetting technologies for desalinization and has exclusive licensing agreements with KMX and Hyrec. KMX uses vacuum membrane distillation technology for high-total-dissolved-solids (TDS) levels, while Hyrec uses osmotically assisted reverse osmosis technology for lower-TDS applications. Both technologies are already commercial in other industries but are now undergoing field trials and lab-testing to determine how they can be scaled in oilfield applications.
“We see the future of water management in oil and gas as being a multi-pronged approach,” Mr Malone said. “There will still be disposal wells, but we need to tackle issues like seismicity and overpressurization in the reservoir pore space. Treatment and recycling of water for completion operations will eventually allow the water to be reused for much longer, reducing the burden of disposal.
“We also know that with water use increasing, drought conditions persisting and the need to minimize the use of freshwater resources, there will be a need for desalinization and the beneficial reuse of oilfield produced water moving forward.” DC