Industrialized processes, scale efficiencies can mitigate high cost variability of shale wells, lower risks
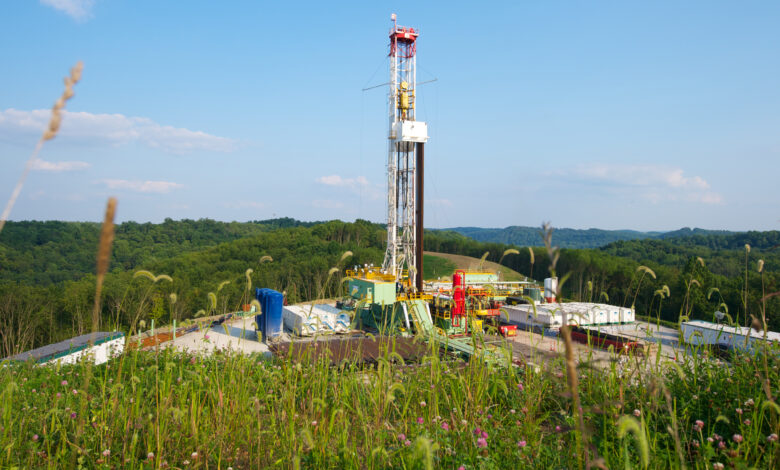
Precision Drilling’s Gene Stahl: Drilling contractors can help operators improve cost efficiency of unconventional projects through consistency, repeatability
By Stephen Whitfield, Associate Editor
Gene Stahl is Chief Marketing Officer at Precision Drilling. He also serves on the IADC Executive Committee.
We had a difficult year in 2020 with COVID-19 and the downturn. How would you gauge the US onshore drilling market?

Everybody’s been through a roller coaster, going from 800 rigs to a low of around 250 – an unprecedented drop. We’ve seen the oil price recover somewhat since then and stabilize in the mid-$40s range. We’ve also seen natural gas prices move up, and we’re seeing the onshore rig count work its way toward 400 rigs. Things have somewhat recovered, but the full rebound has yet to develop, and we have to recognize that E&P priorities have shifted a little bit. We’re pivoting away from a decade of investors rewarding production growth to where they’re more strictly prioritizing shareholder returns and free cash flow. That spending discipline is going to limit new investments in drilling assets and tighten the industry’s focus on cost efficiency.
Overall, from what we know today and looking at the current macro backdrop, we’re expecting a modest gradual improvement in the US rig count in the first half of the year, and there’s potential for a more pronounced rebound once we head into 2022.
What do you think drilling contractors can do to help improve cost efficiency in the unconventional space?
As far as we’re concerned, saving well costs is not some future ambition. It’s a current reality, and we’re constantly striving to do more on this front.
One of the biggest risks related to shale wells is their relatively high cost variability. I think this can be successfully mitigated by what’s been happening over the last decade in the broader industry – primarily the application of industrialized processes and scale efficiencies, coupled with digital technologies, to lower drilling and completion costs.
We’ve seen industrialized drilling really take hold, with the rig representing a big part of that industrial drilling process. The traditional downhole reliability issues have essentially been addressed, and the well designs and approaches have been streamlined by the operator. What’s left is a fine-tuned recipe that’s executed to perfection, from a drilling standpoint. These processes are now, with technology, able to be automated a lot better, creating a consistent and repeatable process.
High-definition data is also available to highlight any process inefficiencies and performance variations. We are getting better and better at using algorithms, rather than just relying on personal experiences, to push the performance envelopes. I believe drilling contractors are uniquely positioned to bring all of this together, more than anyone else involved in the industrial drilling process. All of these technologies and processes are significantly improving efficiency and consistency to deliver safer and faster wells, which translates to lower overall well costs.
What markers are you looking for to indicate that a recovery from the downturn is under way?
US shales are an important piece of oil production to help meet global oil demand as it rebounds post-pandemic. There are several favorable investment characteristics with shale drilling; namely, its low geological risk, low political risk, sunk cost infrastructure and short-cycle production response.
Even with that, we don’t expect to see a return to 850 active rigs in the near term. Normalized rig activity will likely be down from pre-pandemic levels. However, the quality, capability and digital technology component will be much higher, with fewer rigs drilling more wells on larger optimized pads. The super-spec rigs – digital-AC, 1,500-horsepower, equipped with x/y pad walking systems, 7,500-psi pressure systems, large pumping capability, high racking capacity masts – are the rigs that will dominate development drilling. There’s a much tighter available supply than most people believe, and it’s essentially consolidated within a handful of drilling contractors.
Precision Drilling is heavily involved in a number of basins in the Lower 48 and Canada. In which basins do you anticipate an earlier recovery in drilling activity? Which basins are garnering the most attention right now?
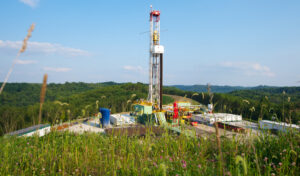
In the US, the strength in natural gas prices has provided a bit of baseline activity for us, specifically in regions like the Haynesville. Activity in the Rockies is also emerging, and then as you move to the Permian, you’re seeing recovery across the board. The recovery in the Permian is being driven by several recent M&A transactions that are really focused on scaling and cost efficiencies. That will drive synergies and drilling opportunity.
With that said, we expect sourcing new capital will remain a significant challenge at least through 2021, and maybe for the next several years. Industry participants will need to rely on their own cash flows as a primary source of funding for drilling plans.
In Canada, it’s a similar story on the gas front. Over the longer term, additional pipeline capacity from the Trans Mountain, Line 3 and potentially the Keystone projects will reduce the oil differentials that have challenged the industry over the past decade. In addition, the LNG Canada project is expected to be in service in 2023, and that should provide an additional market for Canadian gas and generate new opportunities for drilling contractors out there. In our view, activity in the Montney, Deep Basin and Duvernay will be the drivers of growth and avenues for recovery.
How well do you think drilling contractors make use of data at the rig site?
Traditionally, the oilfield has been very focused on geological data and very unstructured surface data, but this dynamic of data-rich exploration and data-poor drilling is changing fast. It’s really becoming all about data literacy. It’s about what you do with the high-speed, content-rich data once you get it. It’s about one’s ability to understand that data and adapt the workflows, which, in turn, make process improvements and drive efficiencies.
Typically, a drilling contractor relies on EDR data. These have data tags that are put into simple analytics buckets to provide the contractor with visibility to the rig. The contractor’s expectation is that the EDR providers, or other analytics providers, will take on the responsibility to provide analytical solutions to the operator in real time and that the drilling contractor would measure and monitor their rig machine data to provide them with equipment insights – how to manage what’s wearing out, what needs maintenance and so on.
At Precision, we’re trying to come up with something deeper. We want to use EDR and machine data to provide operators with deeper insights, while also using this data to manage economics. The EDR and machine data is also used for our closed-loop automation system through the edge servers that we have on our rigs. We feed that data through the servers to feed in drilling parameter roadmaps and app-based solutions in real time.
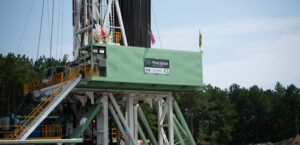
Has the downturn affected the adoption of digital and automated technologies on the rig? Has it accelerated that adoption, slowed it or has it had minimal impact?
I believe the downturn has separated the aspirational from the true commercial offerings we see out in the market. If you were offering something that delivered value, it survived. If it was an initiative that only promised to deliver something, someday, it has been mostly placed on the back burner or parked altogether.
From Precision’s perspective, we’ve actually seen an acceleration of adoption through the downturn. I think that coincides with the rollout of our Alpha suite of technologies. Digitally enabled automation, data analytics and scale efficiency will drive efficiency gains, and that also aligns with some of the ESG concerns that are becoming an important part of the world.
What about remote operations? Is that something that’s been on your radar?
We have a remote operating center as part of the Alpha suite. We use it for supplementing data insights and drilling optimization, mostly internally. What we don’t want to do is get into remote babysitting. The best efforts are made where a driller understands what the task is at hand, what needs to be executed and doesn’t wait to be told what to do.
What challenges do you foresee in making sure that automated and digital technologies can be used from rig to rig?
There are a few aspects to this, the most important being the human element – the mindset shift for the drillers, companymen and management on both the drilling contractor and the operator side. The crew has to be competent to take full advantage of and be able to support these newer technologies. The companymen have to be onboard and up to speed on new ways of doing things.
Technology comes second, in terms of de-risking it as much as possible, making it scalable so it can be deployed rapidly and cost effectively across the fleet. And then it’s about evolving both drilling contractor and operator workflows to be able to maximize value creation through these technologies.
Once these foundations are in place, the rest is relatively straightforward. To give you an example, at Precision Drilling we’ve spent more than three years not only helping perfect the technology but, more importantly, getting buy-in from the field. We have not only trained the rig crews, we’ve trained everyone, from the rig to our operations VPs. They’ve all gone through rigorous digital technology training.
We then built a strong well construction optimization organization to maximize value creation for the operators.
How do you look at artificial intelligence and machine learning?
We believe that simpler sequential types of processes will be easy to automate. The full orchestration, including the more complex sequences, will need to incorporate situational awareness, which will be aided by AI, real-time video analytics and so on. Most of the on-bottom processes that are too complex for simple automation routines and automation implementation can be simplified by leveraging AI for things like optimizing ROP and hole cleaning.
Drilling contractors that have rigs in the automation space will, at some point, require AI to take automation performance to the next level. Machine learning needs to be at the core of all the data a drilling contractor collects every day, where data streams into data lakes in excess of 6,000 tags at 1-hz to 5-hz frequency. The sheer volume of data here makes it a developer’s nightmare to create meaningful analytics without the use of machine learning.
At Precision, we have a high data frequency, end-to-end solution deployed on our edge processors at the rig. We’re also developing machine learning parameter roadmaps and algorithms to promote AI to the AlphaAutomation system in real time.
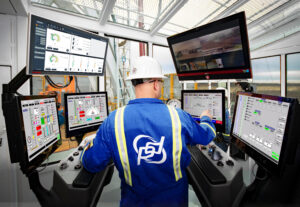
What role do you think technology will play in helping drillers lower their carbon footprint?
Generally, we’ve been very good at finding creative ways to manage risks. Most of the focus in the past has been on the health, safety and surface pollution aspects of operations, which I believe we’ve done a good job of managing, as an industry. Now, we’re adding a much more formal approach on the overall environmental impact, centered around the carbon footprint under the ESG umbrella. So far, most of the efforts we’re seeing on the carbon aspect have been on switching to more carbon-efficient generator fuel types.
I believe technology has the potential to really kick this effort into high gear. If we step back and think about it, most of the wellsite carbon footprint is either related to the logistical support or the rig gen sets. We have a few rigs that are connected to highline, so they’re a lot more carbon efficient, but overall we have to look at what elements or efficiencies we can create to reduce overall output.
An efficient drilling process is not only cost efficient but also carbon footprint efficient. We’ve discussed how technology is helping deliver on the drilling efficiency side. Well, many gains on the carbon emissions side have also been made through the industrialized process, and we’ll continue work on quantifying those gains.
The other aspect of reducing the carbon footprint is how efficiently we run these generators. One of the technologies we’re using at Precision is our power management app, which interfaces directly with each generator to provide real-time fuel consumption, power utilization and engine data for maintenance and engine warnings. These improved insights help us make smarter decisions about fuel efficiency. We are in the process of incorporating the digital drilling plan with this app so the system can proactively bring more gen sets online when required and take them offline in accordance with upcoming drilling activities.
Long story short, the push to a lower carbon footprint is evident from both the operators and service providers, and technology will play an integral role in driving us toward net zero emissions.
What are your thoughts on the current dayrate model? Do you think it’s an adequate way to incentivize drilling performance?
We’ve spent a lot of time thinking about this topic, really searching for creative ways to best align our pricing structure with the operators’ needs while ensuring that we fully capture the value we’re creating for them. One criticism of the current model is that, while efficiencies have been created in terms of faster well times and lower-cost production, the contractors have not been able to capture that value through a standard dayrate. These efficiencies have been further enhanced by the emergence of highly sophisticated digital offerings from service providers and, as a result, the industry is in the early days of trying to establish the best way to get paid for it.
Several variations of the dayrate model and performance contracts are being explored in various ways, and there are positives and negatives to each.
When it comes to performance-based contracts, one thing we’re mindful of is that, as a certain level of performance is achieved, there’s a risk that operators will move the goal post out, gradually increasing expectations and setting that level of performance as the baseline.
We have some agreements with performance-based criteria, but our current digital pricing strategy more closely follows an à la carte pricing model, essentially incremental rates paid outside the rig rate. If an operator wants automation, we charge for it directly, and we’ve set up a distinct pricing structure for the automation and app offerings we’ve commercialized to date. That said, we will continue to explore different alternatives in order to maximize the return on our investment.
The market is going to determine what’s a better long-term solution, taking into account the given risks and full cycle returns. You can expect Precision to stay ahead of this. DC