Taking industrial, rule-based approach to drilling can improve repeatability, aid deepwater project economics
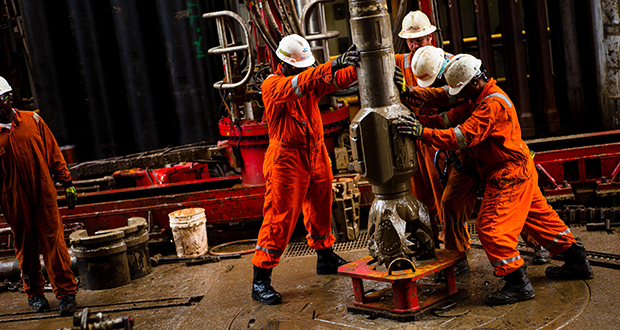
Total’s Xavier Rouzeaud: Digital applications also hold significant potential, but they must be designed from the rig, for the rig and support people on the rig
By Linda Hsieh, Editor & Publisher
Xavier Rouzeaud is Deputy VP Drilling & Wells for Total.
What is the biggest challenge that you see on the horizon for the drilling sector of the oil and gas industry?

There is not a single challenge but multiple challenges, and one of the biggest is finding ways to be successful in an unpredictable oil price environment and a fast-changing world. We are being affected not only by market forces but also by the evolution of society’s expectations in terms of energy and the climate. We must be resilient and adapt to these changes.
Within Total, this means that we must be responsible, profitable and sustainable.
When we talk about responsibility within the drilling discipline, safety is the focus area. We have to make all of our wells and rigs a safe working place, and we must completely eliminate fatalities and blowouts from our operations. Lastly, we must also consider our environmental impact and work to reduce emissions.
Next, in terms of profitability, this means we have to reduce our costs. The more we can reduce drilling costs, the more resilient we can be when the oil price fluctuates and the more we can keep on making new projects economical. To achieve this, the whole industry needs to leverage its spirit of innovation and develop new approaches that allow us to be more efficient and more profitable.
The third factor I mentioned is our commitment to sustainability. One important challenge here is to have technically competent people who can run our operations. We’re seeing that this is not as easy as we thought, so we must do more to attract, train and retain our professionals.
What are the barriers that you face at Total to deliver drilling projects on time and within budget? How does the company try to remove these barriers?
This is a subject that I’m very passionate about, because delivering on time and on budget is the essence of operational performance and of project economics. Being able to keep within estimated duration and cost affects credibility. If investors or other stakeholders cannot trust you to deliver within the allocated budget and the time given, they will be reluctant to launch new drilling projects.
One barrier that I see is the lack of standardization. When you go from one field to another, you often see very different equipment, and you always have to adapt your drilling unit, tools and practices accordingly. Clearly, the more we can standardize, the better knowledge of the equipment and of the program we will have, and the more efficient we can be. That will definitely help to stay within timing and budget. It would also positively affect stock reduction and equipment lead time.
Another associated barrier is that we’re not sufficiently taking an industrial approach to drilling. When it comes to offshore and deepwater project development, we are not systematic enough, and we don’t have enough repeatability. The more you repeat the same type of well or development, the more cost effective it will be. I would like the drilling industry to apply what you see in the automotive industry. We need to take a factory approach to all our operations.
You know, there are two big categories of industries. One is rule-based industries, like airlines, where everything is systematic. Then you have adaptive industries, which respond based on specific situations. Today, I think the drilling industry is more adaptive, but if we want to deliver our projects on time and on budget, we have to become more rule-based.
This doesn’t mean that we would eliminate all adaptive approaches; there are very positive aspects of an adaptive organization. But if we can become more rule-based, I think we will be able to become highly reliable and high-performing organizations, which will help us to deliver projects safely, on time and on budget.
Is there a particular part of the well construction process that needs standardization the most?
Everything would benefit from being standardized, from well architecture to casing types to the well completion. But I would say that we really need to do something with subsea production systems.
Is it hard to standardize in deepwater environments because, unlike the Permian Basin, for example, there are just not that many wells that are the same?
Of course, we are not talking about the same numbers in deepwater, but eventually the number gets bigger. Globally, the industry needs to have some kind of minimum compatibility standards that will make it easier to go from one field to another, or one system to another. Today, those standards are not sufficient.
Total has integrated climate change into its corporate strategy. Can you tell me how this will impact your investments into drilling projects in the coming years?
Total is a leader in terms of integrating climate change into our strategy. We have committed to reducing our emissions by 15% between 2015 and 2025. We have also committed to eliminating flaring from our installations by 2030. And we will do it.
For drilling and wells, we are in the process of precisely mapping our emissions and evaluating all the greener technologies emerging in the industry. That will allow us to have a better understanding of where our emissions come from, so that we can adjust our roadmap for reducing them.
We’ll soon likely be taking things like CO2 emissions into consideration when we perform competitive analyses of our contractors. Eventually we’ll also set maximum acceptable emissions for them.

Our commitment is ambitious, and we will need all the drilling contractors working alongside us. We expect them to look at what they can do to reduce their own emissions and propose new solutions. For example, there could be more efficient power-generation systems on the rigs, or the rigs could run on electricity when cabling is available.
I can say that the status quo will no longer be an option, and soon we will be communicating precise expectations.
I understand that Total plans to create a digital factory in 2020. Can you tell me more about this project?
Yes, of course. We recognize that digital holds big potential for improving safety and efficiency in our industry. We have already launched several digital projects, but we realized we had no central organization for digital that would help us to be even more efficient and transverse in developing our digital solutions.
Secondly, we also recognized that we need to attract new talents that are not currently part of the company. To attract those talents, our digital factory will be built in a part of Paris where big digital players like Google are located.
At this factory, we will have data scientists and software developers who will work with technical engineers to accelerate our digital transformation.
We estimate that, by 2025, the digital factory will allow us to save, for both upstream and downstream, $1.5 billion per year.
Can you talk about Total’s DrillX project, how it got started and what you’ve been able to achieve so far?
The genesis of DrillX was our real-time support center, which is now collecting data from sensors on all of our rigs and BHAs. We have been collecting and saving data for several years, but we realized that we weren’t using much of that big data potential beyond monitoring our operations in real time.
So we started in late 2018 to develop and deploy our own artificial intelligence algorithms, or machine learning, trained on our legacy data sets, to do predictive analytics. The goal was to be able to anticipate operational events like kicks and stuck pipe.
One year later, this became a reality. This is now something that’s up and running on our rigs. We are able to use past data we’ve accumulated, and artificial intelligence can tell us with close to 80% confidence – and low levels of false alarms – when we have a risk of having a kick in a few hours.
Our algorithm was developed in this case with the objective of anticipating the risk of kicks three hours in advance, so that our people on the rig can react and take necessary actions; the main risk factors are automatically provided by the algorithm.

There’s a universe of possibilities for additional development with DrillX, like loss prediction and ROP optimization. This is a very exciting project.
Within this digital transformation, what is the role you see for drilling contractors? How can they help you?
First, I think data should be shared. They need to make rig data available, both real-time and contextual data. This includes contextual data from the BOP or safety reports, but videos can also be considered when working on digital solutions. We need to have this data available and in a format that we can use.
On the other hand, I think we also need to share our data with them. Indeed, we also expect contractors to develop their own digital applications, especially in areas like predictive maintenance of drilling equipment.
Another role that contractors have to play is to jointly educate our workforce on the new digital solutions. One of the most successful aspects of DrillX was that we developed it along with people on the rigs. We didn’t want to give them a tool that they don’t take ownership of.
This applies to any of the digital applications. It will have to be designed from the rig, for the rig and support all the people on the rig.
Some E&P companies have reduced their investments in deepwater because they’re long cycle and require significant capital, but Total has said that it will continue to invest in deepwater. What drives this confidence in deepwater?
First, it’s common knowledge that more than 60% of the world’s deepwater resources have not been discovered yet. There is clearly potential in deepwater, and we cannot ignore that. Secondly, Total believes that our technical experience in deepwater is better than the competition, and it is value adding for us as an operator.
But to be clear, deepwater only works if we can bring in new technical solutions that make these projects cost effective. That will support the profitability of our assets and allow us to sanction new projects.
Today we have five work streams for deepwater. First is subsea tiebacks. For satellite fields where development would not be profitable with standalone production, we can make that kind of field highly profitable if we can tie it back to an existing facility. So we’re trying to push tieback limits further and further. A few years ago, we were talking about hundreds of meters, but today we are already talking about 50 kilometers.
We are also working on marginal fields by proposing a standardized approach that would lower the cost of development.

And we want to be able to develop big new fields cheaper than we have done recently, or as cheaply as we did when we developed Girassol in Angola back in 2000 when the oil price was around $20 a barrel. We managed to do it at the time, so why shouldn’t we be able to do it again?
Next, we continue to focus on frontier drilling: harsh environment, ultra-deep, HPHT.
And lastly, we’re looking at mature fields. Some deepwater fields are starting to become more mature, so we need to find cost-effective solutions for workovers, interventions and P&A.
Lastly, I wanted to ask specifically about well control. Where will we find improvements in the coming years?
First of all, any well control incident in Total, however minor, is reported, analyzed and communicated throughout the company so that we can all learn from the incident.
Further, we are working to improve the well control competency of our employees by concentrating on human factors and human performance. We’re adopting an approach of continuous well control training. This includes things like eLearning and simulator modules, which are spread throughout the year so individuals always stay trained. They don’t just go to training for one week every two years to get their certifications. We’re also looking at putting our employees through training where they get tested on the first day, then they spend the rest of the week working on much more challenging well control exercises.
Something else we’re working to develop is what we call the verification loop. On every operation that we run within Total, we want to perform an audit of well control readiness. This is something that we’ve performed for years with well control equipment, people and procedures. But we want to go beyond that, so we also look at other blowout prevention aspects, share more experiences and good practices with contractors, review what the contractor and other service companies, like mud loggers, are doing. We want to verify that – on the ground – everybody is concentrated on well control.
Lastly, we’re looking at introducing new tools to improve prediction or detection of well control situations, including what I talked about earlier with DrillX.
We are committed to continue to be transparent and systematic in our approach to well control. DC