Caspian Drilling, Keppel overcome myriad challenges to construct Heydar Aliyev semi in Azerbaijan
An estimated 1,000 shipments were required to construct country’s first modern semisubmersible, which is set to begin drilling on Absheron field by year-end
By Kelli Ainsworth, Associate Editor
Getting an offshore rig into the landlocked Caspian Sea is no small feat. The only method of entry is through the narrow Volga-Don canal, which cannot accommodate any vessels greater than 54 ft wide. This means drilling rigs must be shipped in small pieces, requiring multiple time-consuming and costly trips, before being assembled at a local shipyard.
For Caspian Drilling Company (CDC), constructing what it calls the country’s first modern semisubmersible to be built almost completely in Azerbaijan also proved to be a herculean task. CDC estimates that 1,000 shipments – made via air, the canal, trucks and trains – were required to build the rig. “Construction of a semisubmersible in-country had never been done before,” Vladimir Shlimak, Deputy General Director – Projects for CDC, said.
Caspian Shipyard Company (CSC), a subsidiary of Keppel Offshore & Marine, undertook the fabrication, integration, testing and commissioning of the Heydar Aliyev rig. Baku Shipyard, a joint venture between Keppel and the State Oil Company of Azerbaijan Republic (SOCAR), fabricated the pontoons. From Singapore, Keppel provided engineering, procurement and technical support and fabricated the columns and bracings, which were shipped to Baku through the canal.
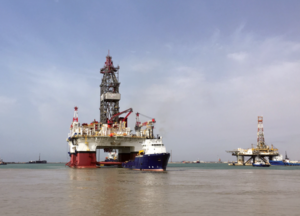
The drive for the project was clear. “The Caspian Sea region has huge natural resources, with limited rig availability to carry out exploration work,” Mr Shlimak said. There are an estimated 48 billion bbl of oil and 292 trillion cu ft of natural gas in proven or probable reserves, and major projects have been ongoing in this region despite the difficult downturn. BP, for example, is the majority operator in the Shah Deniz gas and condensate field, located in the deep waters of the Caspian Sea east of Baku. This year, the operator launched a new subsea construction vessel, the Khankendi, that will install the biggest-ever subsea production system in the Caspian Sea as part of Stage 2 of Shah Deniz. BP expects Stage 2 to add 16 billion cu m of gas production per year to the 9 billion cu m per year already being produced by Stage 1. First gas from Stage 2 is expected in 2018.
Another major project under way is on the Absheron gas and condensate field, located 35 km east of the Shah Deniz field in the Caspian Sea. It is operated by TOTAL in partnership with SOCAR and expected to produce 35,000 BOED, along with a significant portion of condensates, by 2019 or 2020. The sixth-generation Heydar Aliyev is set to begin drilling on this field by year-end.
Work on the Heydar Aliyev began back in 2011, when CDC kicked off a feasibility study and invited design proposals. The company ultimately selected Keppel’s DSS38 design due to the flexibility it offered, for example, with machinery and accommodation layouts. By June 2013, CDC and Keppel had jointly finalized the rig design, which would be for a 106.5-m long, 69.5-m wide and 130-m tall semisubmersible with a maximum water depth of 1,000 m and a maximum drilling depth of 12,000 m.
Although the rig has been built for relatively shallow waters, it has BOP handling and foundations rated for 20,000 psi.
Additionally, the rig is equipped with a dual-gradient riserless mud recovery system to allow for better management of gas and water flows during drilling of the top-hole section. Historically, managing the gas and water flows in this stage of drilling has been a challenge in the Caspian Sea, Mr Shlimak said. Wells have had to be abandoned in the past after the BOP began to submerge due to gas and water flows around the conductor, he noted. Another incident involved a pre-drill template that had to be abandoned and re-drilled after drilling the top-hole section conventionally with water and mud sweeps.
After these incidents, dual-gradient systems were installed on CDC’s two existing semis – the Istigal and the Dada Gorgud. “The system allowed the top-hole sections to be managed with mud weight and without any environmental issues related to venting mud to the sea.”
High winds is another common challenge in the Caspian Sea, so CDC equipped the Heydar Aliyev with a knuckle boom-type crane, in addition to two conventional cranes. “The knuckle boom crane will allow operations to continue when the standard rig cranes may be shut down due to wind speed,” Mr Shlimak said.
Construction of the Heydar Aliyev began at the Baku Shipyard in September 2013. All raw materials were imported into Azerbaijan, as were the large equipment components, including the BOP, marine riser, cranes and crown compensator. The columns and braces were shipped in from Singapore. “The Volga-Don is closed from November to April, so pre-planning of shipments was essential in order to meet the project schedule,” Mr Shlimak said.
At the shipyard, the rig was assembled in blocks. Each of the two pontoons is composed of 12 blocks, and each of the four columns consists of two blocks. The installation of the columns and braces to the pontoons was completed in January 2015. The upper hull, which consists of 10 blocks, was installed between March and August 2015.
Following the installation of the upper hull, the shaker house, accommodations block and drill floor were built. The derrick was then installed in three sections.
CDC took delivery of the Heydar Aliyev in May 2017. The construction came in 10% under its initial budget due to optimization of the supply chain, Mr Shlimak said. Approximately 2,400 workers spent more than 9 million man-hours to design and build the rig, and nearly 80% of the people involved with the rig’s construction and design were Azerbaijani. DC