Digital transformation

Predictive analytics, machine learning and artificial intelligence among emerging technologies being adopted for data-driven innovations in drilling automation, asset integrity, cybersecurity
By Linda Hsieh, Managing Editor, and Kelli Ainsworth, Associate Editor
The drilling industry has always been known for having big iron – from drawworks to iron roughnecks, from top drives to blowout preventers. But in today’s digital oilfield, it’s no longer hardware that’s driving the biggest changes at the rig site. Rather, game-changing technologies on the horizon are now almost entirely digital. Predictive analytics, the Internet of things (IoT), machine learning and artificial intelligence are not just buzzwords. They refer to real technologies that are increasingly being adopted into the drilling industry to improve efficiency and reduce costs.
With this new frontier in technical advances come new challenges, such as cybersecurity, as well as new opportunities that could open the door to completely different business models. “In the oil and gas industry, I think the main catalyst right now is the need to become a lot more efficient, a lot more cost effective and a lot more automated,” said Dr Mehrzad Mahdavi, Vice President, Digital Solutions at Weatherford. “It’s very important to be able to leverage disruptive technologies. It means the difference between being profitable and not.”The drilling industry has always been known for having big iron – from drawworks to iron roughnecks, from top drives to blowout preventers. But in today’s digital oilfield, it’s no longer hardware that’s driving the biggest changes at the rig site. Rather, game-changing technologies on the horizon are now almost entirely digital. Predictive analytics, the Internet of things (IoT), machine learning and artificial intelligence are not just buzzwords. They refer to real technologies that are increasingly being adopted into the drilling industry to improve efficiency and reduce costs.
Digital Technologies Defined
Predictive Analytics | The process of identifying patterns in real-time and historical data to detect trends and determine future outcomes. |
Internet of Things | The network of physical devices that are wi-fi and/or bluetooth enabled. These devices can interact with computer networks, or with one another. |
Machine Learning | The ability of computers to learn without being programmed. |
Artificial Intelligence (AI) | The ability of a computer or machine to act with human-like intelligence, making the same sort of decisions and applying the same sort of reasoning that a human being would. |
There is already a staggering amount of data being generated and captured every day in the drilling industry, but extracting value from data sets requires work. Across all industries, data scientists are already highly in demand. “In a few years, in a typical drilling environment or at an oil company, the number of people that will be required to work with data – to manipulate and analyze data, to create models and to perform statistical analysis – will increase significantly,” Dr Mahdavi said.
Drilling automation
Earlier this year, NOVOS was deployed on 18 rigs for Precision Drilling in North America, reducing connection time by 41% per connection, according to NOV. The time savings were determined by comparing the five best consecutive bottom-to-bottom cycles for conventional drilling to five consecutive NOVOS-enabled cycles. The average bottom-to-bottom time was reduced from 7.91 minutes to 4.67 minutes. “We’ve also seen a lot of improvements on the overall consistency of these tasks,” said Dr Gilbert Chahine, Director of Data Science and Analytics at NOV. “It provides a better quality wellbore.”
Asset integrity
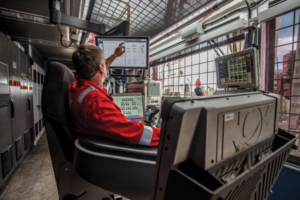
Predictive analytics – in the form of condition-based maintenance – is another application of digital technologies being used in the drilling industry. In Q1 2016, NOV commercialized the Rigsentry system, which provides data on the condition and health of BOPs and topside rig equipment. Sensors provide a constant stream of data from the equipment, which detects patterns and anomalies that are precursors to equipment or component failures. The system can be retrofitted onto existing NOV equipment and alerts users when a fault or potential failure is identified, with some predictive models providing a 14-day notice, according to NOV.
In addition to sending alerts when a fault is detected, the system also “provides prognostics on what will happen if the issue is not mitigated properly and what will be the next level of failure,” Dr Chahine explained. “That way, it provides the user with insight on what will happen if it is not addressed properly and will help make a better mitigation decision to avoid downtime while maintaining performance integrity.” Further, the system allows companies to better plan between-well maintenance of equipment.
Another example of predictive analytics being leveraged in the drilling industry is the SparkPredict software, developed by Austin, Texas-based artificial intelligence company SparkCognition. The software, which incorporates machine learning technologies, learns from sensor data to identify impending failures days or even weeks before they occur, said Philippe Herve, VP-Solutions. The company’s proprietary Artemis algorithm can autonomously identify meaningful relationships in sensor data and find anomalies, while its Pythia algorithm builds models that predict when a piece of equipment or component is likely to fail.

“This allows companies to go from doing maintenance every three months or every 6,000 hours to doing maintenance only when there is an impending failure,” Mr Herve said. “That is orders of magnitude more cost efficient than time-based maintenance.”
SparkCognition recently partnered with Flowserve, a pump, valve and seal manufacturer, to use predictive analytics to identify failures in advance of their occurrence. Using both real-time data and historical data supplied by Flowserve, SparkPredict’s cognitive algorithms were able to predict pump failures up to five days in advance. Previously, the manufacturer was able to predict failures only about five hours before they occurred, according to Mr Herve.
While predictive analytics can be a valuable tool for preventing downtime, he also urged the industry to look beyond it – at prescriptive analytics. “Predictive analytics is just looking at all the data you are receiving to try and predict the future,” he explained. “But if you know what’s going to happen next, then you should ask yourself what to do about it.” A prescriptive analytics platform doesn’t just alert you that a pump is about to fail – it also provides guidance on how to respond to that failure.
A main component of prescriptive analytics is natural language processing (NLP), which refers to a computer’s ability to understand and analyze human speech. Virtual assistants like Siri on the iPhone rely on NLP to function. In the context of prescriptive analytics, NLP capabilities allow a software program to search maintenance reports and manuals – and even emails – to determine how to best address an impending equipment failure and to provide the equipment user with a recommendation. “You can capture all of the knowledge that already exists in many corporations in emails, documentations and drilling reports. All of that knowledge can be queried,” Mr Herve said. SparkCognition has already built NLP capabilities into its platforms, he added.

Beyond even prescriptive analytics, the next step after that will be to allow the machine to take action on its own, rather than just make recommendations. “If the system keeps on giving what seems to be the best answer over time, let’s plug the recommendation straight into the drilling console on an automated system.” This type of artificial intelligence must be implemented in baby steps, however, so that rig crews can have time to build up confidence in the machine. When people see that an artificially intelligent system consistently performs small steps in the drilling process correctly and efficiently, Mr Herve said, they will start to become more comfortable with the system.
New technologies bring new challenges
Even as the drilling industry leverages data to improve performance, the interconnectedness of digital technologies and systems means that new vulnerabilities are also being introduced. To mitigate cybersecurity risks, SparkCognition is again looking to the power of machine learning and artificial intelligence. “Traditional protection systems are not very adapted to the new volume of cyber threats the industry faces,” Mr Herve said. “Artificial intelligence and machine learning are really the only way to block those constantly evolving threats.”
In 2016, the company released its AI-powered DeepArmor cybersecurity platform. It protects endpoints – wireless devices like laptops and tablets, IoT devices, as well as servers in data centers – that are connected to a network. These endpoints tend to be the most vulnerable points in a network. In fact, SparkCognition estimates that 95% of cyber breaches occur at endpoints.
The DeepArmor platform analyzes the DNA of every file that comes into a device and identifies suspicious or potentially malicious components. If a threat is detected, it is quarantined and blocked. Cognitive algorithms built into the platform allow it to learn and adapt to new threats and malware behaviors.

Another way for the oil and gas industry – especially smaller companies – to improve their cybersecurity is by making use of cloud servers, said Jeremy Gilman, Principal at venture capital firm McRock Capital. Although many people are still wary of storing sensitive data on the cloud, Mr Gilman said such servers – especially those that are run and maintained by large tech companies like Amazon, Google and Microsoft – typically provide more robust security than local servers simply because cybersecurity is one of their core competencies. “Hundreds of people at those companies spend all day, every day, making their servers harder and harder to get into,” he said. Meanwhile, companies relying on local servers “have all their data on a box in a broom closet.”
Another increasingly important factor as cybersecurity risks grow is providing personnel with proper training, Mr Gilman added. “Almost all the time, a hack is because of a person… Someone made a mistake, and a hacker was able to access the system.” Employees must be taught how to spot suspicious emails, attachments or files, and training must emphasize securing workstations. “Companies need to take accountability very seriously when security breaches are a result of human error.”
Further, companies must consider roles and responsibilities when it comes to cybersecurity. As an increasing volume of internet-connected sensors are added or built into oilfield equipment, the lines between operational technology (OT) and information technology (IT) become blurred, Mr Gilman added. “There are going to be questions about whether these technologies fall in the domain of IT or OT,” particularly in terms of their maintenance. “Companies need to have a process for who gets assigned to a project and who takes ownership of it,” he said.
New opportunities bring new business models

Leveraging digital technologies will not only help the industry to minimize downtime and improve performance, but it will also open the door to new business models. Look at the aviation industry as an example. The abundance of sensors on jet engines allows manufacturers to analyze the condition of the engine and identify maintenance needs before a plane has even landed. This enables aircraft and equipment manufacturers to sell flight hours, rather than single pieces of equipment. This is already starting to happen in the drilling industry, notably with the Pressure Control by the Hour model launched between Diamond Offshore Drilling and GE Oil & Gas last year.
While that project targets subsea BOPs specifically, the concept can be applied to other equipment, like rotary steerables and MWD systems, Weatherford’s Dr Mahdavi said. “There’s an opportunity for service companies to optimize an operation from beginning to end, providing not only the equipment but also the services for it, and then get compensated for the efficiency of that operation. This is only possible because of things like predictive analytics, sensors and IoT,” he added.
Weatherford’s vision of the oilfield sector’s digital future involves an Intelligent Oilfield Ecosystem that connects advanced surface and downhole sensors with optimization software. The company will introduce these capabilities through integrated services for production, drilling and completion. “We can enable operators to focus on other things by making sure that the drilling process, the completion process and the well construction process are all flawlessly executed using automation. This brings a lot of value to our customers in terms of lowered HSE risk, NPT reductions and overall efficiencies.” DC
DeepArmor, SparkPredict, Artemis and Pythia are trademarks of SparkCognition. Rigsentry and NOVOS are trademarks of NOV.