Extended life, quicker make-up and gas tightness among key innovation areas as operators seek larger tubulars, lower costs of ownership
Additional R&D under way for lightweight, high-torque connections for long laterals in unconventional wells
By Kelli Ainsworth, Editorial Coordinator
In a market where operators and drilling contractors alike are analyzing every nickel and dime in their operations, drill pipe manufacturers must ensure tubular technologies are providing the required performance at an accessible cost. “What we’re doing right now is helping companies to reduce their cost of ownership,” said Guillaume Plessis, Director of Global Marketing for Grant Prideco, a National Oilwell Varco (NOV) company. “We will still see optimization of the product, but we also want to make it a very affordable possibility.”

Cost reductions are being achieved, for example, by extending the life of drill pipe and connections, or by designing connections that require fewer turns to make up. Operators are also turning to larger drill pipe, for both onshore and offshore projects. “They want to reduce their drilling days. For offshore, one day could equal up to $1 million,” said Leianne Sanclemente, Global VP of Engineering and Technical Development for Workstrings International, a pipe rental and engineering company. “Onshore, one day doesn’t represent quite as much savings as offshore, but if they can save one day on multiple wells, it starts to add up, and they can drill more wells per year. It could really define the economics of whether or not to drill a well.”
However, as pipe diameters increase, well control equipment is affected. Manufacturers will be challenged with developing BOPs that can shear pipe larger than 6 5/8-in. diameter. “If you find a solution to one challenge, it almost inevitably creates a challenge somewhere else,” said John Tritz, Global Vice President of Business Development for Workstrings International.
Partnering with the operator earlier in the well planning process can also lead to cost reductions, particularly if the operator wants fit-for-purpose designs.
However, earlier involvement can be challenging as operators often perceive drill pipe as the drilling contractor’s domain, Marta Lafuente, Product Champion for Threaded Connections at Vallourec, said.
Similarly, she added, it often takes some convincing by manufacturers for drilling contractors to send their rig crews to technology-specific training for pipes and connections. “Very often, drilling crews don’t realize that a part is functional and that, if they damage it, it will need repair,” Ms Lafuente said. For instance, the pin nose of an API connection is not functional. However, in the case of gas-tight connections, the pin nose plays a vital role in ensuring gas tightness. If the pin nose is mishandled, the seal ability can be lost, and the connection may require repairs, which could lead to downtime.
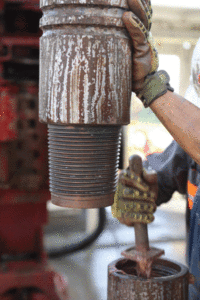
In the onshore segment specifically, R&D efforts are under way to fulfill operator requirements for lightweight and high-torque connections. This is driven by the longer laterals being drilled in today’s unconventional wells. “You need connections that are able to transmit torque along the length of the lateral, above 30,000 ft at times,” Ms Lafuente said. “You can imagine the strength of the connection needed to be able to transmit torque to move the bit at 30,000 ft from the surface.”
Offshore, particularly in remote regions where logistics are challenging, casing is increasingly being replaced with drill pipe. Traditionally, casing was the go-to tubular for completions because it’s gas-tight and meant to be used in high-pressure environments. “Drill pipes didn’t used to be rated for high pressure,” Ms Lafuente said. “Then we started developing drill pipes that were pressure-rated, and some companies started looking at using drill pipe for completions.”
Reducing the cost of ownership
In December 2016, Grant Prideco commercialized the Delta connection, which aims at reducing the cost of ownership of a premium drill-pipe connection. The Delta connection features 130-ksi-rated tool joints – compared with standard 120-ksi rated tool joints on API connections – to deliver increased torque performance. The connection also requires only half the number of turns to make up compared with the eXtreme Torque (XT) connection, Grant Prideco’s second-generation connection commercialized in the late 1990s. Depending on the connection size, the XT connection requires 10 to 13 turns for makeup, compared with six to seven turns for the Delta connection. This reduces both running time and wear on the connection.
In addition, the Delta connection uses a balanced thread form to more evenly distribute its inner loads. “The thread geometry has been designed to optimize connection performance,” Mr Plessis explained. Grant Prideco estimates that the Delta connection will require 50% fewer repairs compared with the XT connection. “If you can keep your pipe in service longer, you basically save money,” Mr Plessis noted.
Even when repairs and refacing are needed, less material loss will occur because the Delta connection requires only 7/8-in. of material in a normal chase-and-face operation, compared with the 1 ¼ in. required by the previous-generation connection. For seal damage, the Delta connection also has 50% more room for refacing before a recut is needed, with a total cumulative reface removal of 3/32-in. compared with 2/32-in. for other connections. If the damage to the connection sealing shoulder is severe, the Delta connection can be refaced three times before it has to be recut, according to Grant Prideco, while the XT connection can only be refaced twice before recutting. This improvement means that drill pipe with the Delta connection can be cut and refaced more times before it must be replaced.
The Delta connection was deployed early this year in both the US offshore and onshore markets in various drilling locations, but field performance data are not expected to become available until mid-2017.
Besides onshore drilling, another market segment that Grant Prideco is focusing on is offshore interventions. Although offshore exploration has “pretty much vanished because of the market conditions,” Mr Plessis noted, “we still see interest in anything that relates to interventions.” In early 2016, NOV delivered the first 7 5/8-in. intervention and completion landing string with a new MaXit connection. The technology was developed in response to a major operator’s request for such a string, with a 6 ¼-in. ID connection so that a larger crown plug could be run through it. “It is a very large ID for drill pipe,” Mr Plessis commented. “Before we built this product, the largest size of pipe was 6 5/8-in., and the largest ID we were offering was 5 ¼ in. for the connection.”

Because most handling equipment on drilling rigs typically cannot provide more than 100,000 ft-lb of makeup torque, Grant Prideco also had to design the connection so that it could be made up below the 100,000 ft-lb torque limit, despite its size. Other technical requirements from the operator were for the connection to be gas-tight and to have a pressure rating of 20,000 psi.
The new intervention 7 5/8-in. pipe size and its mating connection, which took a year to develop, were deployed in late 2016 in the Gulf of Mexico. Not only did the connection meet all specified requirements, but the operator also was able to reduce slip-to-slip times by 62% while tripping. Additionally, overall completion time was reduced by 3.5 hours, according to Mr Plessis.
Combined with a second deployment, the only repairs needed for both jobs combined were 12 redressing of the seals. No connection recut was needed at all. Further, by using this pipe/connection combination to replace casing, the operator did not need to bring out a casing crew to the rig. “The rig crew assembled stands of the intervention string during flat time,” Mr Plessis said. “When it was time to deploy the string, it was ready to go.”
Incorporating flexibility
In mid-2015, Vallourec developed the VAM Express-M2M connection for deepwater drilling, interventions and completions. This double-shoulder connection is very similar to a drill pipe connection but has a metal-to-metal seal in the pin nose, which guarantees its gas tightness. The need for drill pipe-based gas-tight connections is being driven, especially in the Gulf of Mexico, by the need for gas-tight products that are able to be run several times without repairs for drill stem testing, high-pressure interventions and completions operations, according to Ludivine Laurent, Sales Manager GOM at Vallourec.

The VAM Express-M2M connection has been qualified for up to 25,000-psi internal pressure and 30,000-psi external pressure. Lab testing has shown it can withstand up to 100 make and breaks, according to Vallourec, compared with approximately five to 15 make and breaks that casing connections can generally withstand. During lab testing, the connection was made up 100 times with the recommended makeup torque. After the 100th make and break, a hydrostatic test proved that the connection’s integrity was still intact.
The connection was deployed for the first time in the Gulf of Mexico in mid-2016 and is expected to be deployed for Petrobras offshore Brazil in early April, Marta Lafuente added.
Another innovation from Vallourec over the past couple of years has been the incorporation of a forge into its pipe manufacturing process. The tool is now used to manufacture drill pipe with diameters of 6 5/8-in. and above. This has been driven by operators’ need to land heavier casing strings and to remove larger crown plugs for offshore completions, Ms Lafuente explained.
Although larger-diameter pipe allows operators to land heavier strings and remove larger crown plugs, they are also more difficult to manufacture using the typical friction welding process. Using a forge has helped to address this challenge, with the pipe being held and rotated on a cylindrical mandrel while it’s heated and shaped by four hammers. Shaped bars of varying diameters are used to shape the ID. The end product is weld-free, meaning there are fewer points of potential failure on the drill pipe. Vallourec said it believes it is currently the only company using a forge to manufacture drill pipe.
Protecting equipment
In offshore wells, the exposure of pipe to salt – both from seawater and from completion fluids that contain salt compounds – can cause the metal to corrode and pit. “When it dries, it starts to look as orange as a rusty swing set,” Leianne Sanclemente of Workstrings International said. Once pipe reaches this state, operators and/or contractors have to send it onshore to be cleaned, repaired and inspected before it can be shipped back out to the rig. Sometimes, pipe might be too damaged to reuse. “We have seen instances where the pipe is used for years and others where it is downgraded on the first job,” she said. A combination of parameters, including the length of the time pipe is on the rig and in the wellbore fluids, as well as the type of drilling and completions fluid used, can accelerate the corrosion process.
In 2011, the company began researching external coatings with improved durability and protection from salt exposure. Out of 10 coatings that were screened and tested, the company selected five for field trials in the Gulf of Mexico. “We had a testing criteria that included repeatability, cost, durability and ease of application,” Ms Sanclemente said. Testing revealed a compound that is commonly used to protect bridges and ships from corrosion provided the best protection for pipe, while meeting all test parameters, as well.
The resulting coating, RustGrip, was launched in late 2015. It is applied to pipe as an airless spray at the company’s Broussard, La., worldwide headquarters in a dedicated coating facility. To date, the coating has been used in 15 intervention operations and eight deepwater completion jobs, all in the Gulf of Mexico. In these applications, RustGrip-coated pipe has stayed in use for up to three consecutive completions and up to 8 months before sending it in for cleaning and repairs, according to Workstrings. There have been no downgrades due to corrosion in these operations. Previously, pipe would often require cleaning after just one well, according to Ms Sanclemente. DC
Delta and MaXit are registered terms of National Oilwell Varco. VAM Express M2M is a registered term of Vallourec. RustGrip is a registered term of Workstrings International.