Safety goes hand in hand with performance, must remain top priority even in difficult market
Investments in training, diversifying workforce also must continue alongside efforts to increase digitization, standardization
By Alex Endress, Editorial Coordinator
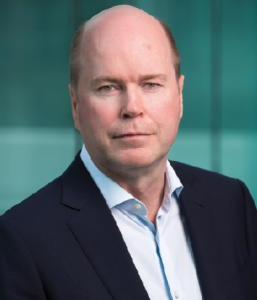
Gary Jones is Head of Global Wells Organization of BP.
What do you see as the most critical challenges facing the upstream oil and gas industry right now?
The number one priority is to keep improving safety. It’s a very difficult economic environment right now, but we find that the same factors that contribute to strong safety performance also lead to strong performance in all aspects. We need to think about how we can work smarter together to take out waste from the system. We also need to think about how to encourage new talent to come into the industry with the current economic climate. In the long term, energy demand is still growing. We need to make sure that technology development is still occurring, so we need our brightest minds working on how we’re going to get after reserves, both conventional and nonconventional.
How can the industry make sure the downturn doesn’t cause a competency gap?
We need individuals working for our industry who are equipped with solid technical and non-technical skills and capabilities. Collaboration is key. We recently supported Maersk Training in opening up their new facility in Houston, which is a state-of-the-art totally immersive training environment. It’s very similar to the one Maersk had already established in Svendborg, Denmark. This is an industry initiative. We’re encouraging all our offshore drilling contractors to use the facility. We think this type of immersive, scenario-based training is the future. We want to train people – not just to learn well control individually but as a team in a safe environment where we can really challenge them. We want to train them such that when they are offshore and they have to handle rare events, they’re fully trained in doing it.
We’ve also made a conscious decision not to stop recruitment. We’re working very hard on diversity – that means gender diversity but also global diversity.
In the BP global wells organization, we have a team that has been working on identifying the barriers to entry. For example, what puts women off to coming into our industry? What keeps individuals of different nationalities from coming to the industry? Have we created a work environment that unintentionally creates a barrier for certain individuals?
For instance, the nature of morning meetings at 6 a.m. and late nights in a 24/7 operation can be difficult for people who have childcare responsibilities. But with today’s technology, do you really need an in-person 6 a.m. meeting?
I believe we need to think about why it is the way it is and how can we open it up so more people can be interested and involved. We want people to get excited about what we can do in this industry.
We need to make sure that in a time when many companies are going through a period of layoffs, we are still attracting new people into our industry, whether they come in through the service companies, the drilling contractors or the operators. The drilling contractors’ drillers and toolpushers are going to be some of the industry leaders in the future. That’s why we’re working with our contractors on training and development programs, such as those at the Maersk Training facility.
What is the status of Project 20K, and how do you see the downturn affecting long-term initiatives like that?
The bottom line is to recover reserves. We have to be able to do it safely and with a reasonable rate of return. What we’ve done with Project 20K is get much more collaborative.
We’ve begun a collaborative agreement with Chevron and ConocoPhillips that creates a new ownership and operating model in the Gulf of Mexico. Working together, we’re more likely to efficiently unlock these high-pressure, high-temperature (HPHT) reserves and to do so earlier than we might individually. Our focus is on how we can work collaboratively to efficiently develop these reserves to meet longer-term demand, regardless of the current oil price.
Why is it important for the drilling industry to continue investing in long-term R&D?
What we’re trying to do is look at how we continue to improve safety and become more efficient. What we all know is that the things you want to put in place to be a safe industry are the same things that deliver great performance – those things go in tandem. What we want to take out is the waste that does not enhance safety or efficiency.
Just as we are continuing to invest in the development of a new immersive training program, we need to keep developing technology.
We need to prioritize our investments and ask ourselves where we are wasting money, because that’s of no benefit to us, to drilling contractors or to service companies.
Also, we have had an inflationary period where costs have risen to levels that threaten profitability even at higher oil prices. We are focusing on being clear with the oilfield service companies on what technologies we need and what we need them to do.
Further, we must consider which service company might be in the best place to develop the technology. We need to invite the appropriate contractors in to hear what the problem is so they can work on a solution, rather than us simply telling them we know the answer. It comes back to really respecting and leveraging the different skill sets brought to the table.
Can you give us some examples of waste?
To give you some perspective on waste, look at how operators currently order and procure equipment. There are many different types of quality assurance requirements that operators can have on products. When dealing with the minor variations of bespoke equipment, those can add schedule delays and higher overall costs. We want to get as standardized as possible. We want manufacturers to build standard components.
We need to sit down with our suppliers and tell them about the level of reliability we require and then work to their quality assurance system. With the drilling contractors and service companies, we’ve been finding that, if you give them that space, then they step up and help provide safe, reliable and efficient approaches.

If we say we want them to provide the solution but then micromanage it, they may not take as much responsibility for its reliability. We can do a better job of listening to the suppliers about the costs that add up and which can be eliminated. If what we are asking them to do adds a lot of cost but doesn’t reduce risk, it should be scrutinized.
Are there any new technologies under development that you think could help make business more efficient?
One area is digitization in the subsurface aspect of seismic imaging. With the super computers that we have now, there are masses of seismic data. We can get better imaging but, on the drilling side, we need the ability to more effectively and efficiently analyze all of this data. Instead of spending 80% of our time trying to get the data and then 20% working on it, with improvements in digitization, we strive for it to take 20% of your time to get the data. Then we can spend 80% of our time analyzing it. I think this is going to be really fundamental.
A lot of what you have talked about is a focus on safety. How can the drilling industry make sure cost-cutting measures don’t hurt safety or operational integrity?
We’ve been very clear with everyone in our organization and our contractors that safety is the priority. What we are talking about here, everything we are asking them to do is to make things better, without an adverse impact on safety. We’re not asking anyone to simply reduce costs to hit cost targets. We’re asking them to improve performance, which includes safety.
In our own organization, we’ve given clearer accountability of who are the ultimate decision makers. With our contractors, especially in an environment like this, we need people to be speaking up. If people are being asked to do something that they are concerned about, we need them to speak up. Simply from a performance perspective in any industry, we know that if people are trained properly to get it right the first time, they will safely deliver optimal performance.
We’ve seen a lot of emphasis from drilling contractors on upgrading the specs of our global rig fleet. Are today’s rigs able to meet the needs of the future?
I think we’ve made great strides. Some of the rigs that are coming out now – with the level of rig floor automation that they have – are taking people away from the hazards. We’re doing work on BOP reliability, working with the original equipment manufacturers, the drilling contractors and operators to improve the reliability of this core safety-critical equipment.
We’re looking at working with service companies, drilling contractors and operators to give input on design of the rigs so they are more efficient. We’ve had instances where actually the dayrate of the rig is higher, but efficiency of the rig makes it a worthwhile investment. If we can show that the cost of the well is lower, then that’s a win-win for everybody.
How can the oil and gas industry improve on completions technology?
For completions, one of the things that really hurts us is early well life reliability issues. You’ve spent all this money to execute the well, you’ve put the completion in the ground, and then you have an issue with the completion early in the well life. There also might be a productivity hit because of skin damage to the well. We need a focus on safe and reliable operations, whether it is the drilling phase or completions phase. You want to avoid having to go back to a well to do a workover. You want to make sure you pick a completion that will provide the productivity and reliability right up front.
How can the drilling industry approach new regulatory requirements to make operations safer while not hurting productivity?
This is an area where we need to communicate, we need to be listening and we need to be thinking from an industry perspective. When you get very prescriptive, you can drive outcomes with unintended consequences. Questions to ask are: “Is the requirement reducing risks? Is it using sound engineering principles, and is it cost effective?”

Industry standards development is an effective way to enhance safety and reliability. For example, API Standard 53 is a great bit of work focused on how to improve subsea equipment with sound engineering.
What more can drilling companies do to earn the social license to operate?
Maintain a focus on safe, reliable and compliant operations. Most important to achieving that is focusing on our people, including our training programs and competency development. We need to be in an environment where people are going on training courses because they want to be the best they can be, as opposed to just trying to get through the test to receive a certificate. We’ve made a lot of progress on enhancing training programs for well control, which we need people to deeply understand.
There’s also a teamwork aspect. Learning about well control is one thing, but we need individuals to work well together as a team – avoiding groupthink, listening to everyone’s input, asking “Do I have the latest data? Could something have changed from when I left the office to go to the drill floor?”
Leadership skills are key, as well. We need to make sure that our procedures are fit for purpose, they’re readable, they’re understandable, they make sense and that people can challenge them if they don’t work.
If we’re utilizing a contractor’s rig, it should be their safety management system being followed and not an operator imposing its own safety management system. We need to understand any differences in expectations and bridge these gaps.
How has BP changed since April 2010?
BP made a commitment to be a safer, stronger company, and it has done that. A lot of my job is to go to the rigs and check that things that we think are being done are actually being done. Making sure that we’re putting the right people into leadership positions who understand how to develop their people. Our leaders are there to make sure that we listen when people speak up. Creating a culture where people report near-misses is a good thing. We are making sure we have a strong safety culture where potential issues are looked for rather than just good news.
We’re creating a culture where people ask the challenging questions, such as “What could go wrong here?” We are making sure risk assessments really are looking for what we understand the risks to be. The atmosphere is that we want to get these reserves online, but we all understand that safety is the number one priority. We hire very good people into the industry, and we need to continue to develop them and listen to them. If they say stop because something might be wrong, we are absolutely listening for that. DC