Simplified requirements reduce potential to overwhelm humans’ short-term memory capacity
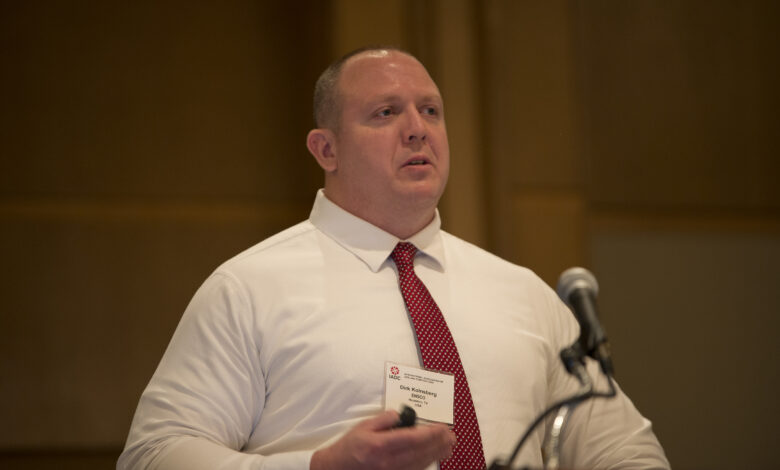
By Alex Endress, Editorial Coordinator
When rig crews experience lost-time incidents, a common reaction from management is to question why rig supervisors and crews didn’t follow procedures, or possibly why they didn’t even know the correct procedure to begin with. According to Ensco Performance Assurance Director Dirk Kolnsberg, the answer may be that offshore personnel have become overloaded with the vast amount of safety requirements crews now face. These requirements may stem from new regulations, new industry standards or even new company policies. “It is the current reality, and there’s a potential for the person offshore to become overwhelmed,” Mr Kolnsberg said at the 2015 IADC Human Factors Conference in Galveston, Texas, on 21 October.
While there is good intent behind each safety requirement, there is also a limit to how much a person can recall from memory and perform well. The short-term memory capacity of an average person will allow him or her to memorize only four or five tasks at a time. “It is just human nature. There’s a finite capacity,” Mr Kolnsberg said. He advised companies to identify truly safety-critical tasks for rig crews to follow. These tasks should be committed to a worker’s long-term memory, and verification should be done to ensure each task has been completed correctly.
Looking at toolpushers as an example, Mr Kolnsberg noted that these employees can be tasked with more than 200 competency assurance requirements – far too many for any employee to memorize and perform reliably. “It turns out to be quite a lot that we’re expecting that person to have a good level of knowledge about,” he said. “Do we expect them to memorize all of that and put that into long-term memory?” Additionally, many crews have “tribal knowledge” or undocumented responsibilities, which he said were gaps in the risk management process.
To reduce complexity for the toolpusher, Ensco reassessed the 200-plus requirements, then simplified processes, consolidated steps, eliminated duplication and distributed safety-critical tasks equally among personnel. Mr Kolnsberg said his group was able to narrow required tasks down to what is truly safety-critical for the toolpusher to carry out in order prevent hazardous events. He listed the toolpusher’s required attendance during man-riding operations as an example. “If the toolpusher isn’t present on the rig floor during man-riding operations, in our business, we know that bad things can happen because they have.” Ultimately, Mr Kolnsberg said, the company was able to boil down the toolpusher’s requirements from 240 to 17 critical tasks.
These 17 requirements are truly safety-critical and would require self-verification from the toolpusher that each task has been correctly completed. To understand self-verification, employees are trained to personally recognize how these 17 requirements are paramount to safety during the drilling operation and to recognize when tasks haven’t been sufficiently completed. “(I’m) not saying that they don’t need to do anything else, but this is what we want them to verify that they’ve done because we want to give them a mental checklist of the things that we say are so important that we want you to verify that you’ve done them.”
With a simplified list of requirements, employees are better able to keep track of safety-critical tasks. Therefore, it is also easier for them to personally verify task completion – creating more accountability and more effective self-verification. “We want to give them every opportunity to be successful, (and) to make it easier for them to succeed than it is for them to fail.”
Always enjoy the articles and videos.
It’s on target with what we’re trying to accomplish at our workplace.
The accountability aspects are always a good read for me.
You guys are on top of the issues.