Trend analysis, cross-audits part of safety management system under Keppel’s WSH 2018 vision
By Linda Hsieh, managing editor
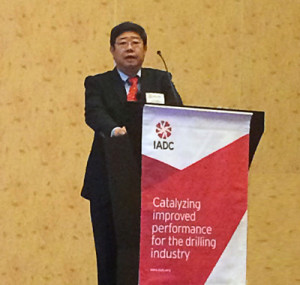
Four key strategic thrusts – framework, system, ownership and partnerships – are driving sustained safety improvements under Keppel Corp’s “Workplace Safety and Health 2018” program. Workplace Safety and Health (WSH) 2018 is “a comprehensive framework for the needs and requirements of (Keppel’s) different business divisions and their workforce,” Keppel Offshore & Marine CEO Chow Yew Yuen said last week at the 2014 IADC HSE&T Asia Pacific Conference. “Our vision is for everyone in our workplace to go home safely everyday. We believe that this can be achieved through a strong and cohesive workforce where each stakeholder, employee and subcontractor alike plays a part by sharing the safety, knowledge and experience, as well as look out for one another’s well being,” he said.
Mr Chow noted that one the biggest challenges Keppel faces is the multitude of nationalities and cultures that can be found within its global workforce. “Besides Singapore, we have shipyards located in places such as Azerbaijan, China, Brazil, Qatar, Philippines, Netherlands and the US. Very soon we’ll probably have one in Mexico, too,” he said. “Each country has its own regulations, systems, culture and language, not to mention they all have their unique challenges.”
Globally, Keppel manages more than 70,000 workers who hail from 65 countries, creating a significantly diverse multinational and multicultural work environment. “In our Singapore yards alone, there are at least 35 different nationalities working together, so you can imagine the challenge to communicate to them effectively,” he said.
The first key part of WSH 2018 is building a framework to guide all of Keppel’s businesses and yards. This includes having a Board Safety Committee to review and examine the effectiveness of the company’s safety management system, as well as a corporate HSE policy to set the direction for business units in chartering their respective safety road maps. “Based on lessons learned, safe work procedures and guidelines are then developed for critical activities, aligning safety practices across the group and helping to benchmark safety standards,” Mr Chow said.
To monitor and share safety best practices, a common reporting system has been established to help relay critical information quickly and efficiently when an incident happens, he added.
With a framework established, the second part of WSH 2018 calls for the implementation of an effective safety management system. The company identified eight factors vital to this system:
- Safety leadership. “Our management and officers lead by example and set the tone for safety. That is why safety performance is included in the KPIs of the heads of our business units and section heads,” Mr Chow said. “They chair weekly safety review meetings with safety and operational personnel and regularly conduct walkabouts of the yards.”
- Training and infrastructure. An integrated safety training center was set up to train employees and subcontractors, aligned with a set of guidelines that was developed to be understood by a multinational workforce. “We continuously upgrade our infrastructure, leveraging technology to increase automation and mitigate risk at the workplace by reducing human exposure to hazards.”
- Trend analysis. Mr Chow noted the importance of identifying the most common and high-risk incidents through the reporting of incidents and near-misses. “This leads to campaigns that target things like falling from height, dropped objects or safe material handling.”
- Cross-audits in overseas yards. These target safety initiatives and practices, including the maintenance of major equipment.
- Safety workshops and site visits. Keppel engages Dupont to visit its yards and assess its safety performance. “Safety workshops held in our overseas yards are also important platforms to encourage sharing of information and alignment of Keppel Offshore & Marine safety culture,” Mr Chow said.
- Communication and cross-sharing of safety. As part of this effort, Keppel identified high-impact risk activities and continually reminds its workforce of those risks.
- Safety campaigns. “Regular safety campaigns such as HSE Day also help create awareness of specific initiatives. We organize regular HSE sharing sessions at the various yards and our workers’ dormitories.”
- Safety innovation. Keppel employees are encouraged to form safety innovation teams to generate ideas to improve the workplace; many ideas have already been implemented, he said. “Examples include a device which helps to significantly lower the risk of finger injury and back injury when installing pipe spools on the vessels, as well as improve productivity and efficiency.”
The third and fourth strategic thrusts of WSH 2018, Mr Chow said, are enhancing ownership and strengthening partnerships. Both involve communication and coordination with the various stakeholders. “Empowerment is an important aspect of ownership,” he stated. “We have created various platforms for our different stakeholders to take ownership of safety and empower them to intervene whenever there is at-risk behavior and provide feedback on ways of improving working conditions.”