Competency-driven projects to mark 2014 IADC chairmanship
Jay Minmier aims to direct industry resources, focus to ensure a skilled and credentialed workforce
By Linda Hsieh, managing editor
If he hadn’t gone into the drilling industry, Jay Minmier thinks he could’ve made a good career as a coach. “I like working with people. I like mentoring people, and I like coaching people. I just really enjoy helping and watching young people succeed with their career goals.” This passion has led Mr Minmier to place a strong focus on personnel and competency at Nomac Drilling since he joined as president in 2011. Now, as he takes on an additional role as 2014 IADC chairman, he’s again tapping into that passion for helping people succeed.
“IADC is undertaking wide-ranging and critical projects on behalf of the global drilling industry that can impact every drilling contractor,” he said. From the Knowledge, Skills and Abilities (KSA) project to the Workforce Attraction & Development Initiative (WADI) to the Well Control Institute (WCI), competency-driven projects such as these will be the cornerstones of his chairmanship.
“In the coming year, I will be working closely with IADC staff and our members around the world to ensure the delivery of these initiatives. Once completed and implemented, I’m confident that they will take our industry to the next level,” Mr Minmier said.
In 2012, the drilling industry’s worldwide lost-time incident (LTI) rate reached a record low of 0.26, according to the most recent IADC statistics. Although the industry should be proud of the significant gains it’s made in safety, Mr Minmier also notes that, “with each successive record, it becomes that much harder to make the next incremental improvement. I’m firmly convinced that continuing improvements in safety and operational excellence are only going to occur when we dedicate ourselves to evaluating and ensuring the competency of our crews.”
Industry’s safety journey has been aided in recent years by technical advances, such as iron roughnecks and automatic slip pullers, that have removed humans from high-risk operations. A steady shift in culture and mindset has also supported continuous improvement. “During my career, we’ve gone from a culture of ‘incidents are simply part of our business’ to a culture of ‘maybe it is possible to work incident-free’ to the present, where it’s an absolute expectation. We don’t argue whether it’s possible to work safely anymore. We expect it.”

To continue this journey, Mr Minmier believes further progress will come down to the people on our rigs and ensuring their competency. Nomac alone has hired approximately 700 people a year since 2011, and the backbone of its personnel advancement system is the Rig Crew Development Program. The program includes defined competency blocks for a range of rig positions, from floorman to driller to rig manager, and “anyone who desires to move up through the rig hierarchy must demonstrate the competencies for both his current job and his next,” Mr Minmier said.
This program has allowed Nomac to shift away from the more traditional tenure-based promotion system, where the next driller position often went to the derrickman with the most experience. Under the competency-driven system, only employees who have successfully completed their competency blocks would be considered for the promotion. “It’s all about competency verification, and it ties beautifully into the IADC KSAs. We’re really excited about using the KSAs to improve our own processes at Nomac.”
For companies that don’t already have such a program in place, the KSAs will serve as the blueprint to set up new competency verification programs. “You might omit a few competencies or add some of your own depending on the needs of your specific company, but most of the work is done, and IADC will be giving that to the industry for free.”
Paying it forward
Besides his passion for working with people, the personnel efforts Mr Minmier has undertaken at Nomac and his competency-driven goals as IADC chairman also have roots in the early days of his career. In 1991, after having separated from the US Air Force and armed with an electrical engineering degree from the University of Texas at Arlington and an MBA from the University of West Florida, Mr Minmier set out to find employment at a job fair in Austin, Texas.
He recalls interviewing with 10 companies that day but was quick to take the first offer he received – from Helmerich & Payne (H&P). It was an abysmal time for the drilling industry, but Mr Minmier decided to take the job because the company seemed like a good fit with his personality and career goals. “It just felt right,” he said.

He ended up roughnecking for his first 10 months at H&P before moving through a series of posts – as a division engineer, building rigs as part of the engineering construction group and then overseeing H&P’s offshore group. “H&P deserves a lot of credit for bringing people in during an extended down cycle. Back then, many companies were barely surviving, but H&P had the vision to believe that there’s never a better time to bring young people into the industry. They knew that once the industry recovered, they would have a pool of succession candidates.”
Looking back on those early days, Mr Minmier said, he realized that the training program he went through was smartly structured not only to provide field experience but also to give each employee an understanding of multiple rig types and different aspects of a drilling company. Mentors were also made available to each employee.
“It was an amazing experience and remains very important to me. So when I came to Nomac as president, I knew I wanted to replicate the experience for today’s young people. I sat down with our recruiters and HR people and told them what our program needed to look like. Now we’re hiring young men and women into the industry and providing them the field exposure and development tools to ensure we’ll have succession candidates in a few years when it’s time for me and the leadership team to hand the company off to others.”
Mr Minmier ultimately stayed at H&P for 14 years before moving to Grey Wolf/Precision Drilling, where he served in a variety of roles overseeing HSE, operations, and sales and marketing. He joined Nomac Drilling as president in 2011.
Technology and rigs
The continued evolution of US shale plays will see rigs being employed predominantly on multi-well pads, and Mr Minmier believes contractors must embrace this change
“Much has been written about the horizontal drilling revolution, but it’s still under way. Pad work is simply an extension of that revolution,” he said. “Through horizontal technology and pad application, we can develop the same acreage in a shale resource with 98% less surface interruption. It’s more efficient, less costly and environmentally responsible. And it requires a different mindset.”
Process optimization and repeatability will become critically important for onshore contractors, he believes. “We’re entering a manufacturing mode in this industry, and we need to standardize our processes. Our customers need us to deliver holes in the ground as efficiently as possible and with the greatest amount of consistency and least amount of variance as possible.”
Automation will be key in order to achieve that repeatable process. “There are really just two primary reasons we see variability in our well durations. One is geology, and the other is human factors. As often as not, when a well is delivered less successfully than before, it’s because somebody didn’t do something the same way he did it last time, or the guy who knew how to do it wasn’t there that day. It’s almost always human related.”
The solution, Mr Minmier said, is to automate more of the well construction process. Nomac has been working with vendors to develop drilling control systems that catalogue and transfer human-related decisions into software, applied as automation.
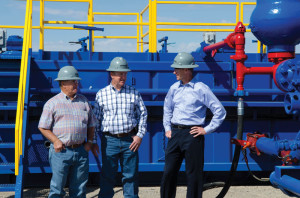
This doesn’t mean humans will be replaced, he emphasized. “It means we’re letting the control systems and machines do the routine, mundane and hazardous tasks, and we’re freeing up humans to use their brains and be innovative. I’ve had drillers ask whether the new systems will ultimately make them obsolete. My response: Every plane you fly in has an autopilot, but you still see two uniformed professionals sitting in the front, right?”
Nomac, industry future
As a subsidiary of Chesapeake Energy, Nomac has felt the impact of the operator’s activity reduction over the past couple of years. In response, Nomac began actively marketing its rigs to other operators and currently realizes approximately 40% of revenues from outside customers. “Nomac was created in 2001, just as the US shale revolution was under way. Shale drilling is essentially all we’ve ever done, and we’re very good at it. Other operators have been eager to tap into that expertise,” he said.
Like many other US contractors, Mr Minmier expects to continue upgrading Nomac’s fleet by building new Tier 1 (AC) rigs and divesting of the company’s remaining Tier 3 (mechanical) rigs.
Overall, he said, this newbuild/divestiture strategy is likely to mean that Nomac will end up with a smaller fleet – but it will also be a more high-spec fleet that can better meet customer needs and generate higher returns. “To me, that’s more responsible than just piling on rigs. Besides, lacking significant policy change in Washington, I don’t see the US onshore industry being able to absorb incremental rigs, which is a shame. Our industry has been a huge contributor to job growth over the last few years, but it appears future growth may be limited by artificial constraints.
“It’s disappointing that our industry continues to be cast in a negative light by various groups when all we do each and every day is employ domestic resources to responsibly deliver a domestic product that greatly benefits domestic consumers.
“The industry as a whole needs to step up and help to shape a healthier debate in the public forum around safe and responsible drilling. If we don’t engage, we’ve lost the battle.”