Drilling & Completion Tech Digest
Pumping equipment for fracturing switched to dual fuels
Halliburton, Apache Corp and Caterpillar have developed dual-fuel technology to safely and efficiently power the pumping equipment used for fracturing treatments with a mixture of natural gas and diesel. With 12 pumps (24,000 hp), it is one of the largest dual-fuel projects in the industry.
G. Steven Farris, chairman and CEO of Apache and chairman of America’s Natural Gas Alliance (ANGA), encouraged Apache and the industry to increase the use of natural gas as a fuel for engines. In response, Halliburton developed a technical solution for converting the pumping equipment used at a typical large-scale fracturing spread to a dual-fuel system that includes natural gas.
Halliburton and Caterpillar teamed up to convert new Q-10 pumps to dual fuel with a technology that would accommodate high-quality liquefied or compressed natural gas. Caterpillar adapted its proprietary Dynamic Gas Blending engine technology to power Halliburton’s pumps.
Separately, Halliburton was selected by Statoil to provide multilateral technology (MLT) for two mature fields offshore Norway. The three-year frame agreement includes two optional periods of two years each and has an estimated value of more than $200 million.
The FlexRite Multibranch Inflow Control junction and the FlexRite Intelligent Completion Interface junction, of which Statoil has installed approximately 150, will form the basis of this frame agreement. Together, these sealed junction MLT systems enable flow control capability of all laterals in multiple legged MLT wells.
ONGC sets drilling record offshore India
ONGC has set the record for drilling a well in the deepest water by an offshore drilling rig with Transocean’s ultra-deepwater drillship Dhirubhai Deepwater KG1. The rig spudded well NA7-1 in exploratory block KG-DWN-2004/1 on the east coast of India in a water depth of 3,165 meters (10,385 ft) on 23 January.
The rig then lowered and latched a subsea BOP and riser on the wellhead on 9 February to drill to TD of 5,625 meters (18,455 ft). The rig has surpassed Transocean’s prior record of 3,107 meters (10,194 ft) of water depth, set in 2011 by Dhirubhai Deepwater KG2 working for Reliance Industries on the east coast of India.
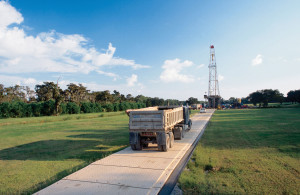
Milestone reached in production of protective mats
Newpark Mats and Integrated Services recently reached a production milestone with the 250,000th DURA-BASE Advanced-Composite Mat. The mats are produced from a non-slip advanced-composite formulation that withstands bearing loads in excess of 600 lb/sq in.
The production milestone also marked the preservation of over 1 million trees (or approximately 1.25 million wooden mats), along with savings in transportation costs and emissions.
The mats provide ground stabilization that minimizes the need for aggregate or gravel and enhances worker safety while preventing soil disturbance and road dust. They are designed as a single piece, with no individual parts requiring bolts or fasteners to hold them in place. The one-piece system prevents spills from being absorbed into the mats and aids in preventing spills from contaminating ground soil.
Maersk Drilling, BP to develop HPHT drilling technology for Project 20K
Maersk Drilling and BP have signed an agreement to develop conceptual engineering designs for a breed of advanced offshore drilling rigs, critical to unlocking the next frontier of deepwater resources.
BP and Maersk Drilling will collaborate on rigs that can operate in high-pressure and high-temperature reservoirs up to 20,000 psi and 350°F. The agreement is part of BP’s Project 20K, a multi-year initiative to develop next-generation systems and tools for deepwater exploration and production that are beyond the reach of today’s technology.
GE to provide HPHT technologies offshore India
Marking its entry into India’s high-pressure, high-temperature (HPHT) drilling sector, GE’s pressure control business has received contracts to supply technology for a new well to be drilled in Cairn India’s Ravva block off the east coast of India.
Separately, GE recently received a contract to supply four complete, variable frequency drive, high-speed electric motor and centrifugal compressor packages for Total E&P Norge’s new offshore production platform on the Martin Linge oil and gas field. The area is located 150 km off the coast of Norway in the North Sea, and production is scheduled to start in 2016.

Statoil to use modular Archer rig to plug, abandon Heimdal gas wells
Statoil will use the new Archer Topaz modular rig for the permanent plugging and abandonment of 12 gas wells on the Heimdal field in the Norwegian North Sea. The rig, which will be built with Max Streicher GMBH in line with current NORSOK regulations, will be operated by Statoil with partners TOTAL, Centrica and Petoro.
Carrying out plugging and abandonment operations on a modular rig is a first for Archer and the industry, the company believes.
The total contract value, including the startup, operating and decommissioning phases, is estimated at US $115 million. Operations are expected to commence in the second half of 2014, and the contract duration is 34 months, with four option periods of three months each.
“The award of this contract demonstrates the attractiveness of our modular rig concept, which combines flexibility, efficiency, short rig-up and rig-down time, making it a unique proposition for our customers both for plug and abandonment services and production drilling from fixed offshore platforms,” Kjetil Bjørnson, president and general manager of North Sea region, Archer, said.
The new rig will follow the design of Archer’s first modular rig, the Archer Emerald, which has been operating for Shell Todd in New Zealand on a production drilling contract since 2012.
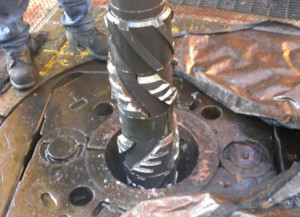
Cleanup system mills 207 ft of cement, removes 500 lbs of debris in deviated well
An operator in the Gulf of Mexico had a highly deviated (78°) and deep (30,200 ft or 9,205 meter) measurement-while-drilling (MWD) well that needed cement milling, casing cleaning, fluid displacement and blowout preventer (BOP) cleaning. The depth and deviation of the well presented an initial challenge for sufficient cleaning. Additionally, the well had been previously displaced to completion fluid.
Baker Hughes deployed a suite of wellbore cleanup tools, mostly made up of the X-Treme Clean XP system. The customer’s workstring consisted of 4-in. and 5-in. drill pipe with high-torque XT connections.
For the milling operation, the X-Treme Clean XP system was run to a depth of 29,993 ft (9,142 meters), where the top of cement was tagged. The system then milled 207 ft (63 meters) of cement at an average of 9.4 ft/hr (2.8 meters/hr), reaching a final depth of 30,200 ft within 28 hrs. During the milling operation, three 70-bbl high-viscosity sweeps were pumped to aid debris removal.
The BOP jet sub was run to a depth of 85 ft (926 m) and made six passes through the stack. A total of 500 lbs (227 kg) of debris was removed by the filters and magnets.
Eni Norge to develop first Barents Sea oilfield, contracts for pre-laid mooring spreads
Eni Norge has contracted IOS InterMoor to provide two complete mooring spreads for development drilling in the Goliat oilfield in the Barents Sea, offshore Norway. “Goliat field is the first oilfield to be developed in the Barents Sea,” David Smith, IOS InterMoor managing director, said.
Recoverable reserves for the Goliat oilfield are estimated at 174 million bbls, and production is expected to plateau at 100,000 bbl/day.
IOS InterMoor will provide two complete moorings spreads for pre-laying in the three-year contract period. This method provides enhanced safety and integrity, as well as significant cost savings, particularly in rig moves, as it eliminates the downtime a rig spends not drilling. The reservoir drainage strategy will include water and gas injection, employing a total of eight well templates with 22 wells.