Multistage stimulation pushes Chinese well over production target
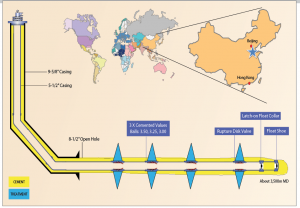
Ball drop system, horizontal drilling among key enablers to boost DaGang field output
By Liu Guang Hua and Cui Hui Kai, PetroChina DaGang Oilfield Company; Jeremie Fould, JS Lee, Wang Hai Long, Zhang Xing Guo, Isaac Aviles, and Jason Baihly, Schlumberger
New production goals issued by the Chinese government of more than 6 million tons of oil equivalent per year in one field created a challenge to more quickly deploy new industry technology. In the DaGang field, PetroChina DaGang Oilfield Co leveraged a new methodology and streamlined the use of technology to quickly and economically ramp up production.
New drilling and completion techniques used include completing horizontal wells with multistage hydraulic fracturing in some fields. New methods of isolating and stimulating wells were also examined in some low-producing areas. The outcome of the study allowed the operator to realize production nearly 10 times greater than a conventional vertical offset well and three times greater than the production expected from an unstimulated offset horizontal well.
The nZone ball drop multistage stimulation system was introduced to stimulate a horizontal well in the DaGang field, where cemented vertical completions are common and require artificial lift to produce.
Horizontal cemented completions were recently introduced as a means to increase field-wide production. The completion design called for a standard cement job. Although plug-and-perforate methods are applicable in these wells, PetroChina DaGang turned to a different solution to reduce time to production.
A key factor in achieving the production goal in this field has been to achieve incremental production gains in newly drilled wells.
Ball drop multistage stimulation method chosen
Prior to running ball drop multistage stimulation systems, standard methods were used to complete wells in the DaGang area, mostly drilling and completing vertical wells. The target zone was perforated on these wells, then stimulated from surface. A rod pump would be installed. To boost individual production in new wells, it was decided to drill horizontal wells. Based on the drilling-versus-production risk/reward, new technologies that decreased the risk of completing horizontal wellbores while allowing them the flexibility to fracture-stimulate the well and mechanically isolate in between stages were explored.
The plug-and-perforate technique was considered as an option; however, after quick analysis, it was determined that the necessary extra steps required by this technique would increase risk beyond an acceptable level.
The nZone system was considered because it virtually eliminates risks associated with plug-and-perforate operations and would result in an easier and faster completion.
No perforations for cemented-in system
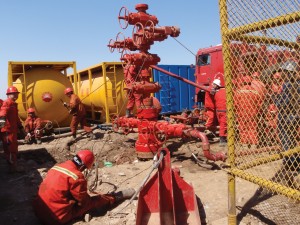
The nZone system is a combination of a pressure-activated initiator valve and a series of sliding sleeve valves that are made up as part of the final completion. Not needing any special considerations when being run in hole, ball drop valves are run as part of the casing string and are cemented in place. Cementing operations take place without any changes to procedures or chemistry.
It is also important to note that the ball drop multistage stimulation system requires no perforations, even though it is cemented into place. Fracturing through the cement sheath without perforating has been a concern in the past with cemented sliding sleeve systems. Having a cement sheath around the valve with no perforations to allow communication from the wellbore across the cement sheath to the reservoir rock can create elevated fracture initiation pressures. Cemented nZone valves have been optimized to reduce fracture initiation pressure.
Diverting in between each fracture stage is an immediate process. In the case of a screen-out and if the ball/seat size combination allows for coiled tubing to go through, the contingency plans are similar to those in plug-and-perforate operations using flowback or coiled-tubing cleanout methods. This combination of ease of operations, simple contingencies, and no changes to the running-in procedure for the final completion resulted in a suitable option for the operator, who was looking to expedite fracturing operations while minimizing risk.
DaGang application
The final completion design for this well had a 5 ½-in. monobore casing configuration and an 8 ½-in. hole in the horizontal section. The total measured depth was 3,475 meters, and the true vertical depth was 2,902 meters. The drilling plan called for a kickoff point at 2,330 meters, where they would drill a pilot hole into the reservoir (45° tangent section). Then, after identifying the final targets, the hole was plugged and kicked off again to land in the proper reservoir zone.
The stimulation design called for a four-stage fracturing treatment. The original fracturing design called for five individual stages, but a final decision during drilling was made to shorten the horizontal section and remove one stage. The KickStart pressure-activated rupture disc valve for cemented multistage fracturing was used on stage one, and ball drop valves were used for stages two through four. Each valve was placed at a strategic position along the horizontal section based on the logging data. In this particular well, the valves were not equally spaced. The well schematic can be seen in Figure 1.
For the first stage, the rupture disk valve was set to an opening pressure that did not interact with the cementing operations. Although it is possible to pre-set this valve in the workshop, in this case it was set up on the rig after gathering and agreeing upon all information relative to the cement job.
The rupture disc valve was set to activate 3,500 psi above the cement plug bump pressure test after the cement job. The ball drop valves’ seats were installed on location once the total number of stages to be completed was determined. The desired opening pressure of the ball drop valves was selected by modifying shear screws based on the expected fracturing parameters. Once the system was run to the desired depth, cementing operations were performed without incident.
Two days before the main fracture treatment and before mobilizing the full fracturing crew, the lower-most zone with the rupture disk valve was opened using a single fracturing pump. Fracturing operations were performed continuously for 10 hours; all four stages were successfully fractured (Figure 3).
After finishing the fourth stage, the well was flowed back immediately for several days. Unlike many other wells in the area, this well was able to flowback naturally without any pumping equipment (surface or downhole) installed. The well flowed naturally for five weeks before the operator decided to install an electric submersible pump (ESP).
Although rod pumps are commonly used in this area due to low production rates in vertical wells, the operator determined that an ESP was more appropriate in this case due to the higher production rate of the well. A long monitoring period started at this point, with the well choked on surface, to stabilize production and extend longevity of the well.
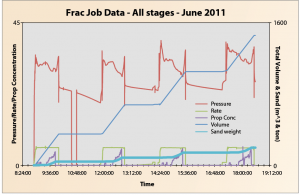
The system performed as expected, and four zones were treated successfully in a single day. Significant time savings where achieved during this operation, which ultimately translated into cost savings and more efficient operations. Further, production was improved significantly compared with offset wells of all types.
Most recently, PetroChina DaGang has gone in to mill out the seats to gain full inside diameter through the valves. Following this successful installation, similar production results and the same operational efficiency have been experienced on five additional wells that were completed and treated using this design. Several other wells are planned to be completed in the near future following the same completion design to sustain and eventually increase production in this mature field.
With the application of the ball drop multistage stimulation methodology, PetroChina DaGang’s desire for an alternative technology that would enable a fast return on investment and allow higher production rates while limiting risk exposure and system cost was realized.
nZone and KickStart are trademarks of Schlumberger.