Petrobras reports new oil discovery in the Santos Basin
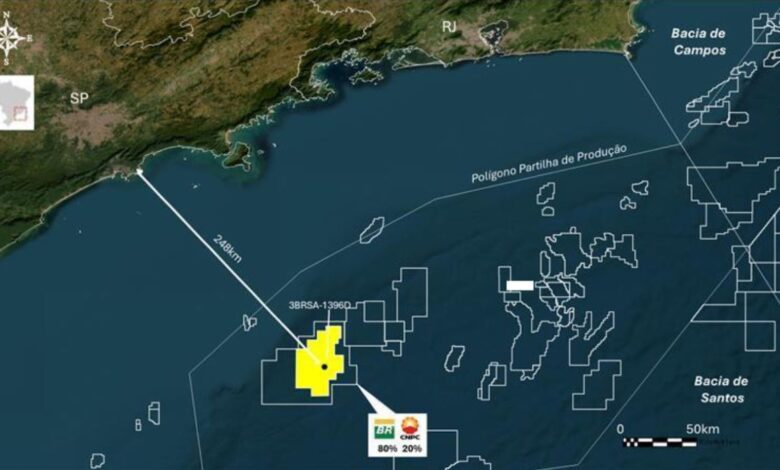
Petrobras reports that it has identified the presence of excellent quality, contaminant-free oil in the Santos Basin pre-salt layer, in an exploratory well in the Aram block.
Well 3-BRSA-1396D-SPS is located 248 km from the city of Santos, São Paulo, at a water depth of 1,952 m. Drilling of this well has already been completed, and the oil-bearing interval was confirmed through electrical profiles, gas traces and fluid sampling.
The consortium will begin laboratory analyses to characterize the conditions of the reservoirs and fluids found, which will allow them to assess the potential of the area. In addition, two more wells will be drilled and a formation test will be performed as part of the Discovery Assessment Plan (PAD).
The PAD has an end date of 2027 and additional data acquisition activities may be carried out, according to planning and contractual obligations established with the National Agency of Petroleum, Natural Gas and Biofuels (ANP).
The Aram block was acquired in March 2020, in the 6th bidding round of the ANP, under the Production Sharing regime, with Pré-Sal Petróleo SA (PPSA) as manager. Petrobras is the operator of the block and holds an 80% stake, in partnership with the company CNPC (20%).