Training must keep up as well complexity rises
Technology gaps must also be addressed in ERD, geosteering, BOP control systems, hydraulic fracturing efficiency
By Katie Mazerov, contributing editor
Graham Brander is director of worldwide drilling for Apache Corp.

With oil prices moving higher and the increased focus on liquids-rich plays, what are some of the key technical drilling and completions challenges operators face in this arena?
I would like to break this question into two parts. There are certainly several technical challenges in these plays, but there have also been significant operational issues. For example, as rig counts in North America have remained high over the last two years, we have seen costs for all equipment and services increase significantly. All operators have had to address these cost challenges as best they can in order to maintain profitability.
If you combine this cost-pressure challenge with the general dilution of work force skills that the industry is experiencing, you have a challenging work environment. I believe we are very lucky at Apache as we have a set of leaders who encourage their employees to take accountability for managing the assets of the company. This has driven our successes in the current climate, where there are undoubted challenges.
With regard to technical challenges, one example we’ve seen recently relates to directional drilling. We have several liquids-rich plays that require short-radius directional-drilling technology. By building angle to horizontal with a short turn, we can significantly reduce the amount of hard rock drilling and therefore the time to drill overburdened formations. Having a suite of rotary steerable tools that can be used on these types of wells would help address some of the challenges we have seen in liquid-rich plays.
I also believe extended-reach or ultra-extended-reach drilling solutions will become more relevant to our industry. And, the challenge of having a suite of tools and equipment packages aimed at delivering cost-effective, extended-reach wells also will need to be addressed.

How is the industry responding to the need for more personnel, training and safety to develop these resources?
I think many companies in our industry have taken a traditional approach to addressing the need for more personnel, such as hiring new staff from schools and training them, or advertising positions and recruiting from the market.
Unfortunately, I see two critical issues associated with these approaches. First, the complexity of drilling projects has increased over the last few years as access to hydrocarbon resources has become more limited. If we hire new staff at a time when the complexity of drilling projects has increased, we must provide them with more thorough and robust training programs. My worry is that the training programs from the past are not sufficient to address the needs of our industry in the future.
Within Apache, for example, we have seen this complexity transition happen very quickly over a short period of time. We have several regions that were drilling simple vertical wells 18 months ago that are now drilling complex directional or horizontal wells. Within Apache, we have addressed this complexity issue in several ways so that we can stay competitive.
The second critical issue I see relates to the issue of recruiting from the market. We are seeing experienced staff finally retire for good. The pool of experienced drilling engineers that we have been relying on for decades is finally diminishing in size at a time when demand for those skills is reaching peak levels. I can pull 10 resumes for folks who were looking to work four years ago who are now off the market through retirement.
At Apache, we have been fortunate in that our attrition rates of staff have remained very low at a time of intense activity in the drilling engineering market.
What are some of the newer advances in hydraulic fracturing, and what is on the horizon in this area?
We have a number of folks in our organization who specialize in fracturing technologies. I am not an expert in this area. However, I would make a general comment that improving the efficiency of multistage hydraulic fracturing is an area in which several companies are investing. With most of the resource plays in North America, it is generally the case that the more fracs you put into a wellbore, the more chance you have of increasing production from the well. However, it is not an exact science.
We have also heard that a number of pump manufacturers are redesigning frac pumps in order to reduce the footprint of the frac spread and improve pump efficiencies.
Do you see the industry moving toward more automated and/or factory drilling?

We are aware of several companies that are looking to deliver automated solutions for drilling rigs. It certainly offers some advantages, if it can be delivered effectively. Indeed, there are several automated solutions already on the market, if you are prepared to pay for them and your project can carry the economics of those automated solutions. I’m not sure that we will ever be able to replace human oversight of our operations, but I have no doubt that many manual, repetitive tasks could be replaced with more investment in automation systems.
We have seen a significant number of automation technologies being incorporated into fifth- and sixth-generation offshore rigs. I believe it will just be a matter of time before some of those technologies are adopted into the land rig market.
How will the current US regulatory environment, particularly as it relates to deepwater Gulf of Mexico (GOM), impact the industry near term and for the future?
I think the key point to address is that of regulatory certainty. We have undergone significant change in the Gulf of Mexico over the last 18 months. With regulatory certainty, we can plan to meet or exceed the regulatory rules. We can plan our capital investments with certainty, and mobilize our equipment to deliver a known scope of work. Without regulatory certainty, the confidence to make capital investment and utilize equipment comes under question. As a company, we invest in projects we can deliver – our shareholders expect nothing less. Regulation stability will be one of the key driving forces to enable the return of a stable GOM deepwater industry.
What are the two or three biggest technology gaps in drilling and completions in the deepwater sector?
I think fantastic steps have been taken over the last 10 years to address deepwater technology gaps. The industry has invested billions of dollars to build a fleet of deepwater rigs to use in all metocean (applies to offshore structures being designed for combined forces and loads relating to meteorological and oceanographic conditions) environments around the world, and these rigs have incorporated many new surface equipment technologies.
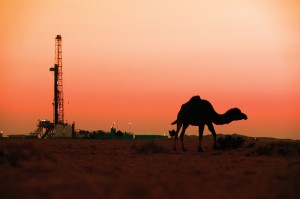
However, I think we still have some technology improvements to deliver with regard to automation on offshore deepwater rig equipment.
With regard to downhole systems, I am a big fan of high-speed data acquisition tools. A couple of years ago, Apache used wired pipe in our offshore Van Gogh field development. The difference in data acquisition quality was significant compared to conventional systems. Unfortunately, the economics for using the current generation of tools have limited their widespread utilization. We would welcome the opportunity to make use of an economic, high-speed, real-time data acquisition system for logging while drilling data.
Several other technology gaps I believe should be addressed in deepwater include subsea blowout preventer control systems. These have become extremely complex as we have moved into deeper and deeper waters, and I believe there are control system technologies that could simplify the operation of these large equipment packages and increase their reliability. I also believe that we have significant steps to take in relation to the reliability and mechanism of subsea shear rams.
In the field of mud engineering, we still rely on drilling fluid properties readings being taken manually several times a day. I think the digital age could provide multiple solutions to address more accurate fluid property measurement.
What technologies are operators looking for to access mature fields in regions such as the North Sea?
We have had eight years of tremendous success in the North Sea, revitalizing the assets of the Forties field by making use of multiple technologies. Extended-reach drilling, to access remote reserves, will be a feature of future North Sea platform operations. In order to make use of this technology, rigs will have to be upgraded and or rebuilt for this type of operation. Many of these platforms were built in the 1970s, prior to the use of top drives, VFDs, PLC controls, 5 ½-in. pipe, cuttings injection systems, etc, all standard items in the modern world but not standard items on these older rigs. I believe there will be continued interest in upgrading older rig equipment in order to make it more capable of delivering challenging drilling projects.

Another critical technology that I believe will be necessary for future mature field development is 3D seismic technology – 4D if the field has sufficient data. Identifying clear target structures with modern 3D seismic can mean the difference between success and failure on these types of projects.
Egypt is an important market for Apache. What are main challenges you face in that region, particularly in the wake of the Arab Spring?
Egypt is a remarkable place, and we have some tremendously dedicated and educated staff working for us in the Western Desert and Cairo. Throughout the Arab Spring, we continued to work and service our operations in Egypt. Indeed, because of the talents of our employees, we did not drop a barrel of production through this period of political change.
Like many Egyptians, we are looking forward to the future, working and prospering in Egypt. We can offer a future Egyptian government investment and employment opportunities as this region reorganizes itself politically. It is a tremendous location to work in, and there is significant exploration potential left in the country.