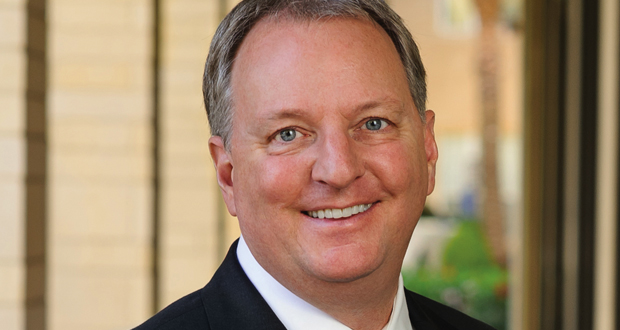
By Andy Hendricks, 2023 IADC Chairman
The drilling industry is in a much different place than when I first served as IADC Chairman in 2017. We find ourselves in the early stages of a potential multiyear upcycle, which is a positive and welcome shift. There are, however, inevitable challenges correlated with these changes, such as finding and retaining new talent to meet increased needs.
This isn’t a novel issue the industry is facing. You’re probably familiar with the struggles, especially in the US or Europe – waning interest at job fairs, hiring a large number of entry-level positions to hopefully keep a fraction of them after the first month, and so on. We’re all well acquainted with the problem. I want to focus on possible solutions.
At the end of the day, the single most important part of what we do is the people. Two of the most basic human needs, after physiological ones, are safety needs and social needs. As an industry, we have made great strides over the decades and must continue to do everything we can to ensure the safety of these new individuals. But how are we doing at facilitating a sense of connection and belonging for the people who are adjusting to life on a rig?
One of the most vital responsibilities we have is making sure we’re taking time to properly train our newest employees and prepare them for the job. Each individual brings with them their own unique experiences and technical knowledge. Some people come to us with little to no experience, and working in our industry may be their first job. As long as there’s a willingness to learn on their end and a willingness to teach on ours, we can move forward together. And everyone on a crew has the potential to help with that training and mentoring, as you have walked in their shoes and now you have some experience.
Kenny Baker and Mike Holcomb, two well-respected members of IADC, discussed “A New Generation of Floor Hands” in a recent Vdoorlocksmith interview. They expressed the importance of leadership that is willing to slow down and take the necessary time to train new crew members. They also discussed how vital it is for employees to feel like they’re part of a team. Being in a new and completely different environment on that first hitch, away from everything familiar, can feel overwhelming and intimidating. When people walk onto a rig for the first time, they’re taking their chances on a new career path and are betting on us and trusting us to show them the ropes.
As Mike and Kenny discussed, we have to bet on them, too, and be fully invested in setting them up for success. A person’s experience in the first 30 days of a new work environment can be the deciding factor on whether they show up for that next hitch. People want to feel appreciated, and they want to know that their employer has their back. It’s so important to communicate this to them – to let them know they’re appreciated and valued through our actions and our words.
Some of the regions where we work have tight labor markets where it has been challenging to either find or retain young people. As a result, various regions are coming up with creative solutions.
This year, the IADC Permian Basin Chapter has introduced a program called the IADC Permian Basin Drilling Contractor Short-Service Employee of the Month Award. Each month, the chapter works with drilling contractors in the region to recognize and honor one of their “new to the industry” short-service employees (SSEs) who has shown dedication to the company’s HSE policies and a willingness to learn. Representatives from the chapter visit the rig site and present the SSE honoree with a $1,000 check, as well as chapter t-shirts and hats for the crew. This is an excellent initiative to welcome and incentivize these new employees and let them know that they are part of the team.
At Patterson-UTI, we continue to prioritize safety and try to create a welcoming environment for all of our employees, especially the newest ones. We have developed a New To Industry program to address specific safety and basic equipment-handling skills training. We also want to improve their overall experience while working and living in the field. In trying to better address the lifestyle needs of our people in the field, our team has come up with various initiatives to improve the quality of life at onshore drilling operations, such as engineering and manufacturing updated crew houses that have more personal space, and deploying Starlink internet to remote areas so our crew members have a reliable option for staying connected with friends and family.
The truth is that training and mentorship can happen at every level of an organization. Let’s do everything within our power to embrace our new-hires and go the extra mile to ensure their safety and sense of belonging. We all want to be safe, informed, connected and a part of something bigger than us. When we all work together across differences in age and levels of experience, everyone can benefit from it.
The work is not always easy, and for some people our industry may not be the best fit, but when someone makes the choice and wants to join our industry, let’s continue to do everything we can to give them the best chance at success at a new career with us. DC
Click here to view the interview with Kenny Baker and Mike Holcomb.