New automatic drilling concept uses multi-input multi-output control loops
University of Houston lab experiment shows the new drilling control methodology can lead to improvements in both ROP and stick/slip mitigation
By Mahmoud Hadi, University of Houston
There are two key factors that contribute to the minimization of on-bottom drilling cost: high rate of penetration (ROP) and the elimination of downhole drilling dysfunctions, such as stick/slip. Currently, the automatic driller and stick/slip mitigation systems work independently and sometimes even compete against each other. To maintain ideal drilling conditions, an advanced automatic drilling system would simultaneously suppress disturbances due to changes in geological formation and mitigate stick/slip vibration, all in one control loop. Stick/slip vibration can be induced from automatic driller dysfunction that fails to maintain a steady downhole weight on bit (WOB).
A research project at the University of Houston has presented a novel drilling control methodology that restructures the automatic driller control loops from a single-input single-output (SISO) proportional-integral (PI) controller to a multi-input multi-output (MIMO) state space controller. The MIMO controller also separates between the automatic driller disturbance rejection and setpoint tracking properties so they can be designed independently.
The MIMO automatic driller simultaneously sends commands to both the drawworks and the top drive to maintain the WOB while regulating top drive torque, which helps to mitigate stick/slip. Speed commands to the drawworks and top drive are synchronized by a linear quadratic regulator controller, which ensures that both pieces of equipment work together to attain the optimal drilling condition. Lab results for the MIMO automatic driller have shown improvements in ROP and stick/slip mitigation compared with traditional control methods.
The control philosophy of existing automatic drilling systems consists of multiple control loops, where only one is active based on the drilling condition. The control loop that becomes active is the one where its drilling parameter is getting closest to or exceeds its setpoint. To achieve this control structure, multiple PI loops (WOB, differential pressure and top drive torque) are programmed as SISO controllers. Collectively, they all work to hold multiple operating points.
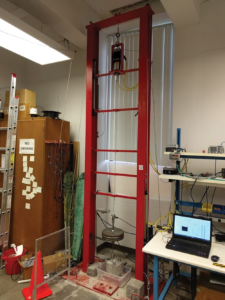
Due to the switching between different PI control loops, the gains of the controllers are tuned for setpoint tracking properties that minimize overshoot of the control variable over its setpoint. These gains are not ideal for disturbance rejection performance because they are relatively lower gains to protect from overshoots. This will degrade the performance of the automatic driller in formations that are not uniform. This can be clearly seen while drilling surface formations.
Stick/slip mitigation systems are designed independently from the automatic drilling system, even though axial and torsional drilling dynamics are coupled. There are two primary control philosophies for existing stick/slip mitigation systems. The first is to de-tune the top drive speed control loop gains to make the top drive power source match the mechanical impedance of the attached drill string. The second is to rectify the surface torque using a feedback control loop that has a PI structure, or something similar to it. Both control philosophies are based on the SISO control philosophy that only controls the top drive system.
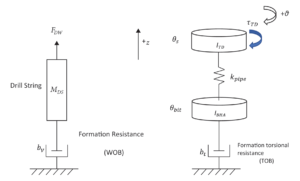
Ideally, on-bottom drilling is a multi-variable process that requires the monitoring of ROP, WOB, torque, RPM, differential pressure, stick/slip vibration, tool face angle and equivalent circulating density (ECD), then responding to those factors by commanding the drawworks, top drive, mud pumps and chokes simultaneously. A proper design of an automatic drilling system requires the understanding on how each actuator will affect the variables in control, develop a system of differential equations for the system dynamics, then utilize modern control theory state feedback control to develop a true MIMO control algorithm.
The research that was done at the University of Houston is a simplified version of this ideal multi-variable automatic driller where only ROP, WOB, RPM, torque, and stick/slip vibration are controlled by actuating the drawworks and top drive simultaneously.
To test the novel MIMO automatic drilling control methodology, an experimental setup was built at the school’s Smart Material and Structure Laboratory. The setup (Figure 1) consisted of six major elements:
- An axial displacement motor, used to provide the same functionality as the rig drawworks system and control the descent rate of the drilling assembly. A linear motor is used due to space restrictions in the laboratory.
- A rotary motor, used to provide the same functionality as the rig top drive system. A high-torque motor with a gearbox is utilized to provide rotary power to the drill string and the drill bit.
- A torsional stiffness element, which is critical to simulate stick/slip vibration, and the torsional spring will accommodate twisting of a drill string during stick/slip, similar to long drill pipe in a real drilling environment. A thin long rod was used to achieve the same properties of drill pipe.
- An inertial element, used to simulate the behavior of a bottomhole assembly. This is required to put weight on the drill bit and to simulate stick/slip vibration. Cylindrical metal disks stacked over each other are used to simulate a BHA.
- A structure to support all of these elements, similar to a rig mast, was used, with two I-beams connected to a metal base that is bolted to the ground. The final structure of the drilling lab setup is around 3 m long.
- Instrumentation: The MIMO control methodology for the automatic driller is implemented on the lab setup as control software programmed into a digital controller, which is a National Instruments Compact RIO automation controller. This controller is interfaced with the linear and rotary motor drives using a fast deterministic ethernet communication protocol. Different sensors are utilized on the drilling setup to sense the performance of drilling control algorithms, either by sensing the ROP or stick/slip vibrations. The sensors are interfaced with the Compact RIO controller using either analog signals or digital lines. A load cell to emulate the rig hookload sensor is interfaced as an analog input. A linear position sensor is also connected to the analog input line to measure the block position. A rotary encoder interfaced as a digital input is used at the drill bit to sense its RPM. To operate the drilling setup, a Windows tablet is used as a human-machine interface that is connected to the controller using wireless ethernet.
Axial, rotational dynamics
The first step for developing the automatic driller MIMO control methodology is to produce a mathematical model for the axial and rotational drilling dynamics, which must be simple enough to be utilized for developing a state feedback controller yet comprehensive enough to capture the main drilling behavior that needs to be controlled. The lumped parameters modeling technique is used to realize the mathematical model. This technique regards the drill string as a system of spring-mass-damper that can be described using ordinary differential equations and is limited to a finite degree of freedom that is used to study the drill string dynamics.
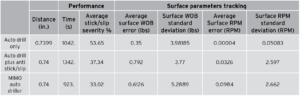
The axial dynamics of the drill string contribute to its motion downwards to go deeper in the ground. The axial dynamics are controlled by the drawworks feed-off mechanism, and the result of that feed off is a linear increase of WOB. This can be described using the lumped parameter system shown in Figure 2, where FDW is the hookload, MDS is the drill string mass, and bv is the formation hardness coefficient. This model is tailored for the lab drilling setup, and it would be slightly different on a real drilling rig.
The rotational dynamics of the drill string contribute to its rotary motion along the total length. The rotational dynamics are controlled by the top drive, and the result of that rotation is an increase of drilling torque all the way to the drill bit. The lumped parameter model of the rotational dynamics for the lab setup consists of two inertias that are connected with each other using a torsional spring as shown in Figure 2 , where ITD is the top drive inertia, IBHA is the BHA inertia, kpipe is the drill pipe torsional stiffness, and bt is the rotary formation resistance coefficient.
The axial and rotational drilling dynamics are coupled and must be considered in the overall multi-variable mathematical model. The two simple facts in the coupling between the axial and rotational dynamics are:
- When the drill bit rotates faster, ROP is higher, in most cases; and
- If more weight is applied on the drill bit, it will result in more torque on the drill bit.
These coupling relationships can be described as a linear relationship for simplicity of the mathematical model.
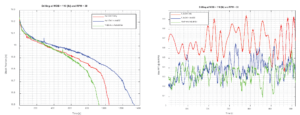
Another important behavior that must be captured in the multi-variable mathematical model is the motor drives speed PI control loop. The inclusion of the speed control loop dynamics is critical since the PI gains affect the dynamic behavior of the axial and rotational dynamics. Combining all dynamic equations from the axial, rotational, coupling and drive dynamics, the resultant multi-variable mathematical model is a state-space system with seven states, two inputs and six outputs. The two inputs are the speed reference commands to the drawworks and top drive.
Parameters such as top drive inertia and BHA inertia need to be identified before developing the exact multi-variable mathematical model. White box and grey box modeling techniques were utilized to identify the parameters in the mathematical model of the lab drilling setup. White box modeling is used whenever the physics law is clearly identified and can be easily computed, such as inertia of a cylindrical hollow disk given its mass, inner and outer diameters. Grey box modeling utilizes physics laws combined with data collected from the drilling setup to identify the unknown parameter.
The MIMO automatic driller control architecture consists of an inner control loop that is designed for disturbance rejection. This loop is a state feedback controller with gains that are computed using optimal control theory, which optimizes the performance of the controlled variables given restrictions in the actuator effort. This is known in modern control theory as a linear quadratic regulator controller. The MIMO automatic driller also has an outer control loop that is designed to make the automatic driller track a given setpoint to the system. This loop is basically multiple integrators that minimize the error in a controlled variable using any actuator available.
To compare the performance of the MIMO automatic driller, two separate SISO control systems were developed using the same integral gains from the MIMO outer loop. The two SISO controllers are a WOB hold and a torque rectification controller. These two SISO controllers are very similar to existing automatic driller and anti-stick/slip systems already in use on drilling rigs.
Three variations of drilling control strategies were compared in this research:
- SISO auto-driller only;
- SISO auto-drill + anti-stick/slip control; and
- MIMO automatic driller (multi-axis).
All three strategies were simulated using Matlab/Simulink software for initial analysis. Simulation data show a slight improvement in drilling speed on the MIMO automatic driller; it also shows that it has the best damping properties for torsional oscillations at the drill bit.
The same three drilling control strategies were also developed on the digital controller of the lab drilling setup. Different experiments were performed, and a consistent result to the simulation is shown using actual drilling data.
Data was collected and analyzed through drilling performance metrics that are designed to analyze the effectiveness of an automatic drilling and anti-stick/slip system. Table 1 shows a summary of comparison of the three controllers.
The data analyzed from different experiments conclude that not having tight control on the surface operational drilling parameters will improve the overall drilling performance. This is the same theory presented by the soft torque system, where having a soft surface RPM controller improved the drilling condition by mitigating stick/slip vibrations. Soft torque was applied on one dynamics axis of rotational control of the drill string. The new methodology of the MIMO automatic driller creates a soft controller on both the rotational and axial control while coordinating between the two axes. This new controller is designed with the objective of improving drilling, rather than tracking surface operational setpoints.
The design of an automatic drilling system needs to follow the same procedure of developing any control system, which is modeling, analysis, estimation and control. Ad-hoc methods of always using a PID controller and tuning it on-site do not guarantee the design requirements.
For an automatic drilling system, the design requirement should put more emphasis on disturbance rejection, rather than setpoint tracking. This is due to the continuous and sudden changes in drilling, specifically in the geological formation.
Drilling is a multi-variable control problem due to the coupling between different dynamic domains in the drilling process. The most efficient controller for a MIMO system is using a state feedback control algorithm. Using SISO controllers for each domain can isolate each domain and result in a lack of coordination between the different domains while they are dynamically coupled. This will disturb the overall drilling process. DC
This article is based on a presentation at the 2020 IADC Advanced Rig Technology Conference, 1-2 September.