Hybrid standardization approach can transform geothermal into scalable, factory-style projects
Combining repeatable design modules with flexibility to adapt to local conditions can help operators cut costs, enhance performance
By Steve Nas, Wellspec
Geothermal energy offers a promising pathway toward sustainable and low-carbon energy systems. However, the high cost and complexity of geothermal well construction remain major barriers to widespread adoption. Projects around the globe face similar challenges: expensive drilling operations, variable geological conditions and a lack of standardized design practices.
This article explores a hybrid standardization approach to geothermal well design that combines proven, repeatable design modules with the flexibility to adapt to local conditions. By aligning well construction practices with standardized templates — while maintaining adaptability — developers can reduce costs, increase efficiency and enhance well performance across diverse geothermal settings.
The article details how standardized casing programs, modular drilling practices and uniform operational procedures can transform geothermal projects into scalable, factory-style developments that are both technically robust and economically viable.
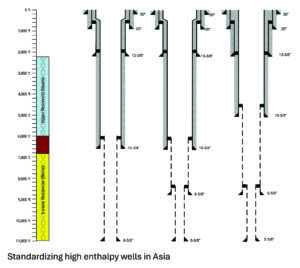
Standardized well design for cost reduction
Implementing standardized well design templates is a key strategy to drive down construction costs and improve reliability. By designing wells using a common framework (casing sizes, well depths, materials) and repeating that template across projects, developers can achieve economies of scale and a steep learning curve.
Common casing and completion programs
Employ a set casing scheme and well architecture as a starting point for all wells, adjusting only where needed. For example, high-enthalpy production wells often use a sequence of surface, intermediate and production casings of standardized diameters, with an open-hole or slotted liner in the reservoir. Using a consistent design reduces engineering time and ensures each well meets proven integrity criteria.
The Netherlands has adopted an industry standard for sustainable well design that operators are recommended to follow for new geothermal wells. This standard, developed from a decade of collective experience, defines the process for achieving safe, robust well construction throughout the well’s life cycle, guaranteeing long-term integrity.
Using standardized design codes not only improves safety but also instills investor and public confidence in geothermal development.
Repeatable drilling plans and best practices
Standardization extends to drilling methodology – using similar bit types, fluids and drilling practices known to work in a given context. Once a “type well” is established, subsequent wells can replicate the plan with incremental refinements.
This iterative learning has already provided dramatic effects in the high-enthalpy Gunung Salak field in Indonesia, where Chevron’s team cut average drilling time from approximately 55 days in 1993 to under 20 days in 2008 by applying standardized well designs and procedures. The campaign’s success – including a record well drilled in 9.6 days – was attributed in large part to a consistent well design template, combined with equipment upgrades and disciplined performance monitoring.
Using a uniform design allowed the team to focus on refining execution.
Standard practices
Geothermal projects can borrow heavily from standard practices in oil and gas well engineering. Many API standards for casing, wellhead equipment and cementing can be directly applied, ensuring compatibility and reliability of components. This interoperability means geothermal wells benefit from readily available, field-tested tools.
For example, standard API casing grades and BOPs rated for high temperatures are used in high-enthalpy geothermal fields, avoiding the need for custom equipment. By using off-the-shelf designs and “plug-and-play” components, integration challenges are minimized and procurement costs drop. Overall, a standardized design approach simplifies the supply chain and reduces construction errors, directly translating to lower well costs and faster project delivery.
Modular approach
A modular approach to geothermal development complements design standardization by treating each well (or well pair) as a repeatable unit in a larger system. Instead of bespoke, one-off wells, a project is built from standardized modules – drilled in sequence and often developed in parallel – to scale up capacity efficiently. This approach has multiple benefits for cost and schedule.
Batch drilling and implementing lessons learned, and drilling multiple wells in a campaign using the same rig and crew, allows lessons from earlier wells to be immediately applied to later wells. This factory-style drilling improves performance with each iteration. Recent US Department of Energy demonstrations for enhanced geothermal systems (EGS) showed that iterative improvements enabled by modular, repeatable operations cut drilling costs by approximately 50% within two years. By standardizing procedures and continuously refining them – similar to a manufacturing process – EGS test wells went from around $13 million to under $5 million per well.
Modularization applies not just downhole but at surface facilities. Designing a standard well pad layout with pre-fabricated components (pipelines, separators, pumps) can significantly reduce construction labor and time on site. In the oil sands sector, for example, a case study on a multi-well pad found that a modularized design cut overall project costs by 32% compared with a traditional approach.
Geothermal developers are adopting similar strategies: Multiple wells can be drilled from a single pad with standardized spacing, and equipment like separators, heat exchangers or pumps can be skid-mounted units. This can reduce field construction time by over a third and improves consistency in quality.
Multi-well patterns and modular reservoir management
In Europe’s low-enthalpy hydrothermal projects, a common modular pattern is the “doublet” system – one production well paired with one injection well for a sustainable loop. Standardizing this doublet module (with fixed spacing, depth and flow rates) allows repeating it across a region.
For instance, Dutch greenhouse heating projects have deployed numerous doublets of similar design (roughly 2-3 km deep, targeting approximately 80-100°C aquifers) with a standard well spacing in the reservoir of around 1-1.5 km. By using a proven doublet template, geothermal developers can streamline permitting and well construction, knowing that each module will deliver the required heat.
Adapting design modules to local conditions
A crucial aspect of a hybrid standardization approach is flexibility – the ability to adapt standard modules to the unique geological and thermal conditions of each site. High-enthalpy wells in Asia and low-enthalpy wells in Europe have different challenges, but both can benefit from a kit-of-parts design philosophy that is tweaked rather than reinvented for each project.
High-enthalpy (volcanic) wells often encounter temperatures of 250-350°C, with low sub-hydrostatic pressures, corrosive fluids (H2S or CO2 content) and fractured formations. Standardization here focuses on robust high-temperature materials and proven well configurations.
For example, a typical module for a volcanic geothermal well might include a large-diameter surface casing to stabilize loose near-surface soils, an intermediate casing set above the loss-prone reservoir, and a production casing anchored in competent rock above the feed zone – leaving the hottest section as open hole. This design module can be reused across many wells, while adjusting depths to match local stratigraphy.
The flexibility comes in materials: In particularly corrosive fields (e.g., acidic fluids in some Indonesian wells), the standard production casing material might be upgraded (e.g., to high-chrome steel or titanium liners) without altering the overall casing program geometry.
Likewise, if a field has severe lost circulation, the standard module might call for known mitigation – like drilling with aerated fluids or adding an extra casing string – as a plug-in sub-module. Notably, a standardized approach does not mean identical well depth – it means using a common blueprint that is scaled to the required depth and conditions.
Asian geothermal operators often establish tiered well design types (shallow, medium, deep) and then select the closest template for each new well, adjusting for reservoir depth. This hybrid standard template combined with site-specific data yields a fit-for-purpose design more efficiently than a fully custom design process.
Low-enthalpy (sedimentary) wells have temperatures typically ranging from 60-150°C, are usually drilled in sedimentary basins and are often used for direct heat supply or binary power. The challenges include moderate temperatures – implying lower energy per well – high water flow required, and the need to protect potable aquifers.
Standard design modules in Europe emphasize well integrity and resource sustainability. For example, a common doublet design might use a steel casing with high-grade cement across all freshwater zones, a production string with corrosion-resistant alloy (if brines are saline), and downhole pumps for fluid lifting.
Well design in the Netherlands encapsulates many of these practices so that new geothermal wells have multiple barriers to protect groundwater and ensure long-term well integrity. There is room to adapt to a specific site (e.g., adjusting casing shoe depths to local pressure regimes), but the overarching structure remains consistent. Additionally, because low-enthalpy projects often require several doublets to meet heating demand, modularity in design is key – it allows regulatory bodies to more easily approve new projects when they conform to a known and safe design, and it allows operators to predict performance based on a standard model.
Hybridizing high and low enthalpy approaches
There is cross-pollination of techniques between the two contexts. For instance, high-enthalpy fields have long used reinjection wells to sustain reservoir pressure; now many low-enthalpy projects adopt the same standardized practice (production/injection pairs) to ensure sustainability.
Conversely, some Asian fields are learning from European oil and gas experiences – adopting liner hanger systems, cementing practices, and logging techniques from standard oilfield practice to improve well reliability in geothermal.
The hybrid standardization approach explicitly encourages this blending: Design modules are not created in isolation for each region but rather built on global best practices with tweaks. An example is the use of aerated drilling to mitigate lost circulation and improve ROP. Pioneered in high-enthalpy fields like Indonesia and the Philippines, this technique is now part of the “standard toolkit” that can be deployed in any geothermal well if needed.
Campaigns in Indonesia and the Philippines credit aerated drilling and other performance improvement processes alongside standardized well design for enabling faster and safer drilling.
In summary, the design and engineering process becomes about selecting the right combination of pre-established modules – casing design, drilling method, completion type (e.g., slotted liner vs perforated casing) – to suit the local resource, rather than starting from scratch each time.
This hybrid method retains flexibility but avoids “reinventing the wheel” for each well.
Optimizing production and minimizing operational downtime
Standardization should extend through the operational phase of geothermal wells to truly realize cost savings over the full well life cycle. By implementing uniform operational practices and maintenance protocols, operators can reduce failures, streamline repairs and maximize energy production from each well.
Proactive maintenance and monitoring
A hybrid standardized approach entails establishing maintenance procedures from the very first well and applying them fieldwide. For example, Mexico’s Cerro Prieto field found it critical that as soon as initial wells were drilled, procedures for cleaning, repairing and controlling wells were established so that all subsequent operations followed a consistent plan.
Key parameters (pressures, flow rates, temperatures) are monitored in all wells using standard instrumentation, enabling data-driven decisions. If scale deposition is a known issue (common in high-enthalpy brines), a standard practice might be to perform scheduled cleanouts every X months, or to continuously dose anti scale chemicals, across all wells. Standardizing these interventions means maintenance teams are prepared with the right tools and spares, and unexpected downtime is minimized. Modern digital tools also aid here: When every well in a fleet is built similarly, operators can create a “digital twin” model of a representative well to predict when performance will decline (due to scaling, pump wear, etc) and schedule preemptive maintenance.
Efficient well intervention techniques
When workovers or repairs are needed, having a standard well design enables the use of specialized, fast intervention methods. All wells having similar diameters and completion profiles means tools and techniques can be developed to service them uniformly. A striking example is the evolution of geothermal well cleanouts in New Zealand. Traditionally, to remove mineral scale or repair a well, operators used a full drilling rig, often quenching (cooling) the well and spending up to 42 days of downtime for a single workover.
A new standardized intervention technique using coiled-tubing units with downhole hammer tools was introduced across multiple fields. This “live well” cleanout method allows wells to be cleaned while still hot and flowing, avoiding quench cool-down. The results have been dramatic: Over 100 wells were successfully cleaned using this method, reducing average workover time to just three days, with as little as 5 hours of actual downhole cleanout time.
By institutionalizing this as the go-to maintenance approach for all similar wells, operators have slashed downtime and quickly restored wells to full output.
Modular replacement and repairs
Standardization also means that critical components (pumps, wellhead valves, instrumentation) are uniform or compatible across the field. This allows a “swap-out” maintenance philosophy – if a production pump fails in a low-enthalpy doublet, a spare unit of the same model can be quickly installed, rather than having to order a custom replacement pump. Downtime for such replacements is minimized because staff are trained on that equipment and inventory is kept. In high-enthalpy fields, wellhead assemblies are often made to a common design – so if one well’s master valve needs repair, the procedure (and any needed parts) is the same as for any other well.
Standardizing also eases the training of operational staff: Crews become highly proficient at a smaller set of tasks repeated across the asset, improving speed and safety. Moreover, data feedback loops can be established – e.g., if one well’s flow starts dropping due to scaling, and all wells use the same design, one can infer that others might soon face the same issue. Operators can apply the remedy to all wells of that standard design.
Improving production efficiency uniformly
A hybrid standard design can be optimized for performance, and those optimizations benefit every well of that design. For instance, if a certain diameter of production tubing yields better two-phase flow lift (reducing pressure losses), that tubing size can be made standard for all high-enthalpy wells, thereby increasing the steam output of every well. Standardized well designs in Asian high-enthalpy fields often incorporate features to maximize productivity, such as big-bore completions and minimal restrictions in the flow path. Once proven at one well, these design choices are applied fieldwide.
Similarly, in Europe’s heating projects, techniques like variable speed drives on standard downhole pumps are used to optimize flow rate from each doublet dynamically – since all pumps behave similarly, a centralized control algorithm can adjust pumping rates to maximize efficiency based on demand, without risking reservoir drawdown. Operational optimization becomes scalable: The operator can roll out a software update or procedure change to dozens of wells in a consistent manner.
Case examples and success stories
Real-world projects demonstrate how hybrid standardization yields tangible benefits in both high- and low-enthalpy contexts:
Gunung Salak, Indonesia (high enthalpy): A multi-well development by Chevron implemented a standardized well design and drilling process across the field. The result was a step-change in drilling performance – average well completion times dropped to one-third of historical durations, and one well was drilled in under 10 days.
This was achieved with no compromise in well quality; rather, standardization improved outcomes by ensuring each new well followed a proven recipe. The lessons learned were fed back into a continuous improvement loop, making Salak one of the most efficiently drilled geothermal fields in the world. This showcases cost reduction and indicates that standard well design did not hinder the flexibility to reach the resource.
Dutch geothermal doublets (low enthalpy): The Netherlands has over a decade of experience with geothermal doublets. By consolidating this knowledge into and standardizing well designs and well construction operations, Dutch operators have already experienced increased well construction efficiencies.
Early adopters report that having a single, agreed design basis streamlines the permitting process (regulators know what to expect) and reduces the incidence of problems like casing leaks or subsidence because best practices (like proper cementing and casing thickness) are built into the design.
This standardization is improving the sustainability and uptime of existing installations – for example, no major well failure has occurred in recent projects built to the new standard, and operating costs are more predictable.
Modular EGS demonstrations (US and Europe): Recent pilot projects for EGS, such as the US Department of Energy’s Frontier Observatory for Research in Geothermal Energy (FORGE) in Utah and a closed-loop demo in Germany, highlight modular approaches. In these projects, multiple similar wells were drilled in sequence, each serving as a test bed for improved techniques.
The modular strategy proved effective – drilling speeds improved by over 500% at FORGE (from the first well to later wells), and well costs fell dramatically.
These examples show scalable engineering solutions in action: by repeating standardized well modules, even novel geothermal concepts can achieve cost reduction through learning and volume. They also demonstrate adaptability: The FORGE wells were standardized in design, yet the team was able to experiment with different stimulation methods in each – a controlled way to innovate without redesigning the whole well each time.
Conclusion
A hybrid standardization approach in geothermal well engineering marries the efficiency of repeatable, modular design with the necessary flexibility for site-specific conditions. By deploying standardized design modules – from well architecture to surface equipment and maintenance routines – project developers can significantly lower drilling and construction costs, by 30% or more in many cases, while also shortening project schedules. Standardization also builds a knowledge base that drives continuous improvement.
At the same time, the “hybrid” element ensures that this is not a one-size-fits-all endeavor. Designs are adaptable to local geology, reservoir pressure and fluid chemistry, using predetermined options and add-ons to handle extremes. Critically, standardized wells are also easier to operate and fix. With common maintenance strategies, operators minimize downtime from issues like scaling, casing repairs and pump failures.
As the examples illustrate, modular and standardized approaches have already been applied successfully in both high-enthalpy and low-enthalpy projects – from Indonesian power producers to European heating networks. Going forward, increasing collaboration and sharing of best practices will further refine these standardized modules. DC
This article is based on a presentation at the 2025 IADC Geothermal Drilling Conference & Exhibition, 25-26 March, Vienna, Austria.