Highly sour fields push challenges for H2S-resistant pipe
Fit-for-purpose pipe grades reduce SSC risks as industry develops sour-service standards
By Vincent Flores, Vallourec Drilling Products
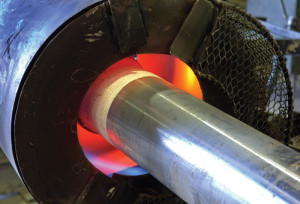
Hydrogen sulfide, or H2S, is hazardous to humans, other living organisms and the environment. Historically, this is the reason wells found with sour gas were often carefully plugged and abandoned. Depending on H2S exposure, symptoms such as coughing, eye irritation, loss of smell, respiratory disturbances, unconsciousness and even death could occur between two minutes and two days.
Steel tubulars, such as drill pipe, could be exposed to H2S during drilling operations in the event of loss of well control. If unfavorable combinations of different factors coincide, this contact can lead to a crack initiation that can propagate and lead to catastrophic failure, even with stresses largely below the steel’s yield limit.
Tubular failures due to sulfide stress cracking (SSC) and increasing HSE concerns around sour gas have led the industry to develop new grades of drill pipe with enhanced resistance to SSC.
Material selection
Material selection for drill pipe in a sour environment is complex, mainly due to the absence of a dedicated international standard. Neither API nor ISO have included requirements for sour service drill pipe in API 5DP, API 7-1 or ISO 11961.
The NACE Material Recommendation MR0175 was written in 1975 but left drilling products out of the scope because such products are supposed to be used in a controlled environment (drilling fluids). Work done by BP and Elf in the early ’90s helped to fine-tune sour service domain knowledge. NACE MR0175/ISO 15156, reviewed in 2004, clearly defines four application domains that provide a range of susceptibility to H2S related to well conditions. NACE MR0175 is considered a reliable selection guide for casing and tubing materials. NACE also defines normalized test methods gathered in NACE TM-0177.
They were created in 1977 and reviewed in 2005. Four testing methods are specified by NACE for oil and gas tubular: A, B, C and D. The testing methods are not equivalent, and each can play a specific role. Method A evaluates the suitability for service through a testing of the material resistance to axial stresses (pure tension), which can be close to the maximum operational stresses that will be applied to the drill pipe.
At a regional level, however, Industry Recommended Practices (IRP) Volume 1 was published in 2004 in Canada. The standard was created with safety in mind and provides material property specifications and guidelines for manufacturers, including quality control, testing and inspection of drilling products intended to be used in critical sour wells.
A decade of H2S-resistant drill pipe use
Sour-service drill pipe as defined in the IRP has been used for a decade in Canada and other regions, along with a variety of proprietary sour-service grades of drill pipe and BHA.
For instance, the development of several gas fields in China’s Sichuan Basin has involved drilling and safety challenges due to the depth of the reservoir and the high content of sour gas (around 14% H2S). H2S incidents during the exploration and development phases led operating companies to select highly engineered drilling products. Examples of major drill pipe failures that occurred in this region prior to 2006 include:
• Blowouts on two wells resulted from SSC drill pipe failures before the well could be killed. In these incidents, 5,030 m of new G-105 drill pipe was broken into 19 parts.
• In Chuandong in the eastern part of the Chuandongbei area, a blowout occurred when the well was drilled at 3,570 m due to improper and untimely treatment of lost circulation. Ten hours later, the drill pipe string near the wellhead failed due to SSC and was lost in hole.
• In October 2005, a well in the town of Maobei, Xuanhan County, was drilled with a targeted depth of 4,840 m. On 24 July 2006, a H2S gas zone was encountered at the well depth of 3,450 m. The drill pipe string that was used was made up of 3,165 m of S-135 drill pipe in the lower section and 608 m of G-105 drill pipe in the upper section. A well kick led H2S gas into the wellbore, and an SSC failure occurred at 2,000 m, resulting in a complete loss in hole. It took more than 40 days to complete the fishing operation.

Fit-for-purpose grades of drill pipe have been selected to resist harsh sour conditions such as these and encourage safe drilling conditions. Such proprietary grades largely exceed the resistance of API grades to SSC and are manufactured using NACE TM-0177 Method A and as per specifications largely inspired by IRP 1.8.
Since December 2006, several critical wells have been drilled using sour-service grades, proving to minimize the risk of failure. No incident has been reported so far.
In the Kurdistan region of northern Iraq, significant amounts of H2S gas lie underground, and reservoir depths easily reach over 20,000 ft. Several drillstring failures due to SSC where standard grades of drill pipe were used were reported during 2010, as a result of loss of well control. Since then, the majority of operating companies in the region have carefully selected H2S-resistant drill pipe. As of mid-February 2014, the tubular inventory in the region largely met IRP requirements.
One operator that switched its inventory to sour-service grades has drilled several exploration wells using two rigs equipped with 5,000 m of IRP 1.8-compliant drill pipe.
The strings have been used in severe environments involving 18-20% H2S and high-pressure conditions. In some cases where underbalanced drilling techniques were used in some well sections, the drillstrings have been exposed to fluids. No SSC failure was reported during the one year of operation.
2014 outlook
With the increasing demand for natural gas in several parts of the world, some highly sour oil and gas reservoirs are being explored with H2S content beyond what could have been imagined a decade ago. To explore, appraise and develop these new fields, which often combine sour and deep/complex well profiles, significant safety challenges need to be overcome, including maintaining drill pipe integrity.
From a normative standpoint, regional initiatives are still active, with the revision of IRP Volume 1 that is expected later this year and the emerging use of IRP Volume 6 in the industry. This volume was published in 2004 and addresses critical sour underbalanced drilling.
The Chinese market has put together its own standard that specifies more stringent requirements toward sour service drill pipe. The standard was issued by the National Energy Administration of China and implemented in 2012. The specification is largely influenced by IRP 1.8 and 6.3 sections and includes high-strength steels and SSC requirements in the assembly zone of the drill pipe.
From a product standpoint, drilling operations in sour wells are more associated with complex well profiles, such as deep reservoirs or extended-reach wells. The use of high-strength drill pipe is essential to achieve such drilling objectives.
However, it does not represent significant technical challenges in terms of drill pipe integrity and operational safety with the current high-strength grades available on the market. Because higher strength is generally detrimental to SSC, innovative chemistries and new heat treatment processes are needed to push sour-service material limits even further.
Additionally, new challenges associated with particularly sour fields require highly engineered drillstring solutions to increase the safety margin related to SSC failure risks, especially in the upset and welded zones. Sour-service drill pipe has long been used with tool joints and tubes fulfilling separate criteria for sour service as defined by the IRP.
Both the upset area and the friction weld present challenges for preserving SSC resistance due to metallurgical factors, such as heterogeneous microstructure, different chemical compositions between the tool joint and the pipe body, and high hardness values close to the weld line.
Conclusions
H2S-resistant drill pipe is an industry-driven technology that has been developed to provide SSC resistance in the drillstring in the event of loss of well control. Some regional specifications have been put together – such as IRP Volume 1 in 2004 in Canada – to provide guidelines to end users for material selection in critical sour wells. Such products have been used in several parts of the world over the past decade and have matured enough to be included within existing international standards, such as API or ISO. Emerging trends will lead manufacturers and end users to look into new grades able to extend the current drilling envelope and push the frontiers of sour gas development in a safe manner.