SLB secures service contracts for up to 35 Petrobras wells
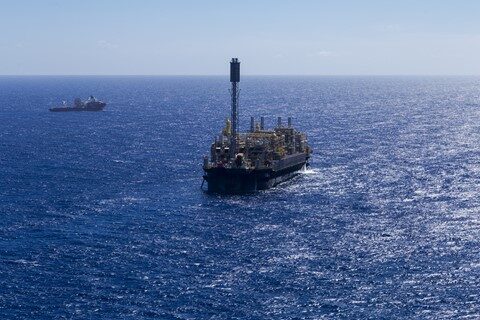
Petrobras awarded SLB three contracts for completion hardware and services for up to 35 subsea wells in the development of Petrobras’ Buzios Wave II oilfield, offshore Brazil. The contract includes SLB’s fullbore electric interval control and electric subsurface safety valves. The award is a catalyst toward full production system electrification for Petrobras, improving production availability via more reliable completions.
By converting to electric completions, Petrobras can control a more sophisticated system in the subsurface reliably. Full electrification of completions enables maximum production control across multiple reservoir drains, potentially requiring fewer wells and limiting heavy workovers during the productive life of the Buzios field wells.
“By leveraging the electrification and digitalization of completions from SLB, Petrobras will increase its field recovery efficiency in complex and challenging pre-salt reservoirs,” said Steve Gassen, President of Production Systems, SLB. “This contract award represents a critical milestone on Petrobras’ journey to digitally integrated offshore electric production systems. It will improve efficiency and deploy innovative technologies in Brazil.”