Drilling & Completion Tech Digest
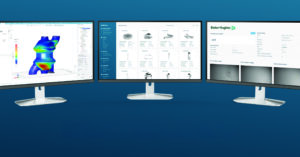
Baker Hughes adopts software to enable additive manufacturing at scale at its Houston facilities
3D Systems achieved a milestone in commercializing Oqton Manufacturing OS, a software designed to enable on-demand additive manufacturing (AM) in regulated markets by providing full factory-floor workflow integration. Baker Hughes is now in full production with Oqton Manufacturing OS in its central manufacturing facilities in Houston. This marks a milestone in the commercial software agreement Baker Hughes entered with Oqton, a subsidiary of 3D Systems, in March 2023. The successful implementation demonstrates the software’s ability to accelerate the design and production of additively manufactured parts across the manufacturing workflow to increase efficiency and facilitate regulatory compliance.
Baker Hughes began using Oqton Manufacturing OS and the Oqton operating system in June 2024 to scale the role of AM within its manufacturing workflow. The system integration enables Baker Hughes to efficiently scale its production output while minimizing investments in the support structure. Additionally, the end-to-end system facilitates the monitoring of key performance indicators through the production workflow. For build monitoring alone, Baker Hughes realized a 98% reduction in active monitoring engineering time, saving 136 engineering hours per printer annually. Root cause analysis has also decreased 98% through Oqton’s automated reporting. Additionally, Baker Hughes realized an 18% reduction in costs associated with scrap due to real-time actionable alerts during part production.
Oqton Manufacturing OS helps companies move from prototyping to a repeatable, high-quality production additive manufacturing process, with full traceability from raw material through finished component. When combined with AM solutions, it reduces time to final components designed to meet or exceed design criteria.
DrillDocs delivers real-time cuttings data to Aker BP
DrillDocs, a provider of digital rig surveillance technology, recently delivered real-time drilled cuttings size distribution data to Aker BP. The company’s camera-based computer vision technology was deployed on a contracted jackup while it was drilling a 1,000-m, 12 1/4-in. hole section on the Norwegian Continental Shelf.
DrillDocs’ CleanSight system deploys cameras for hazardous environments. They feature onboard processing capability for real-time image analysis. Its proprietary image-processing algorithms continuously monitor drilled cuttings exiting the rig’s solids control system, calculating the amount and size distribution of recovered drilled solids. This provides valuable information about hole-cleaning performance, borehole stability and solids control equipment operations.
Prior to this, the shale shakers were monitored periodically by drill crew making visual inspections. The new approach allows the rig team to react in near real time to events happening in the wellbore.
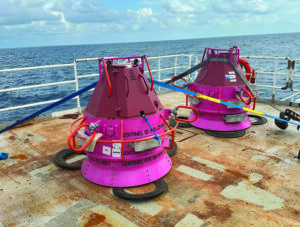
Well monitoring system aids decom of remote assets
Sentinel Subsea recently installed WellSentinel systems for two projects in Australia, supporting the decommissioning of subsea assets.
In one remote field, two WellSentinel Coral systems enabled the continuous monitoring of temporary suspended wells. They were installed on two 18¾-in. wellheads from a vessel of opportunity, ensuring a streamlined operation that required no in-well intervention.
In another project, two WellSentinel Coral-Frond Hybrid systems were deployed to monitor two suspended wells. They feature a Coral design enhanced with a Frond-type gathering structure. This enhancement allowed for monitoring an area approximately 5 meters external to the wellhead.
Expanded partnership targets AI-driven solutions for the energy industry
Honeywell and Qualcomm Technologies announced an expanded collaboration to develop new AI-enabled solutions for the energy sector. Honeywell intends to incorporate Qualcomm’s connectivity and AI capabilities into its existing AI-powered applications, such as the Honeywell Field Process Knowledge System (PKS). By integrating these capabilities, the Field PKS will be able to better help provide connectivity to remote plant and manufacturing facilities and enable greater data capture and analytics at the edge.
Qualcomm’s AI-enabled processors with native wireless connectivity, software and computer vision, combined with Honeywell’s sensing technologies, will enable the development of a family of industrial sensors used for monitoring process parameters, asset parameters or environmental conditions. These capabilities will help deliver more information to field and service technicians.