Concave diamond element bits leverage unique geometry cutters to improve ROP, drilling efficiency
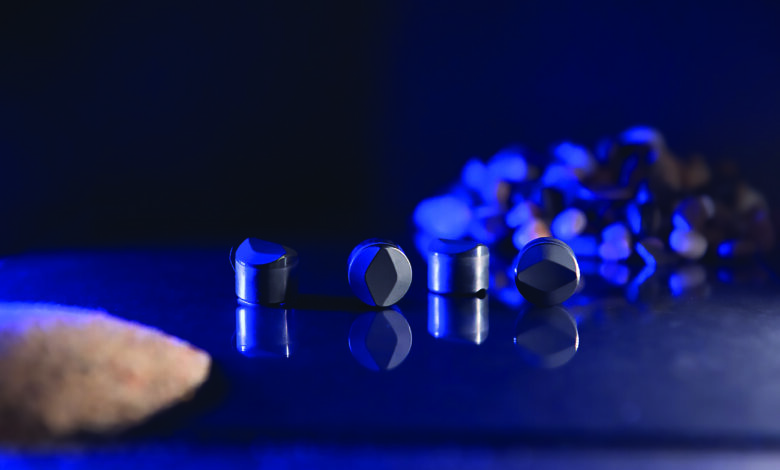
Marcellus and Haynesville case studies show how 3D shaped cutters enhance ROP and drill bit durability in medium-strength, interbedded formations
By Wiley Long, Smith Bits, a Schlumberger company
Innovation of 3D shaped cutters for polycrystalline diamond compact (PDC) bits is evolving as drilling operators desire to drill faster in challenging and complex geologies, including medium-strength and interbedded formations. Because these formations challenge operators to drill more efficiently, improving rate of penetration (ROP) and drill bit durability is key to helping operators reduce rig time and costs.
With drill bits, there are two primary ways that they can contribute to reducing drilling costs: first, by increasing ROP to reduce on-bottom drilling time, and secondly, by increasing durability to eliminate costly bit trips. The challenge is finding the right solution that enables achieving both objectives.
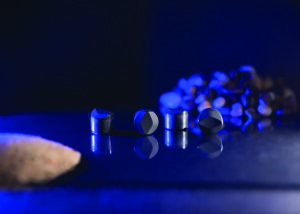
There’s no doubt that the development of PDC cutters over the past 20 years has been instrumental in contributing to improved bit performance. Even after the introduction of leached PDC cutters in the mid-2000s, over the past decade the industry has seen great improvements in material science and manufacturing processes to further advance the durability of traditional, flat PDC cutters.
Technology development for PDC cutters has primarily focused on improving their mechanical properties, such as wear and impact resistance. Over the years, opportunities to deliver the next leap in cutter performance have become more difficult as the industry has exhausted many of the traditional utilities available.
While advancements in flat PDC cutter development have been limited, in parallel, bit manufacturers constantly iterate the cutting structure layouts to seek performance improvements. For example, operators that experience minimal cutting structure damage in their existing bits would likely see this as an opportunity to update the bit design to one that can increase ROP to reduce drilling time. On the other hand, making too dramatic of a change to the bit design can potentially sacrifice durability, resulting in increased rig time due to excessive bit wear and changing out bits while drilling through challenging formations.
The current approaches of traditional PDC cutter and cutting structure development, at best, lead to marginal gains in drilling performance over relatively long periods of time. What operators require is a way to maintain the same overall cutting structure durability of a bit, while receiving substantial performance gains out of the PDC cutters used.
Cutting efficiency as an art
By incorporating shape into cutting elements, another dimension into their potential is realized – cutting efficiency. Improving cutting efficiency at the cutter element level is beneficial in two ways.
First, it allows for increased ROP without increasing the energy input into the bit via weight on bit (WOB) and rotary speed. When increased energy is required to deliver higher ROP, the rate of PDC cutter wear often accelerates and compromises bit durability.
Second, it does not require the bit design to be altered in ways that sacrifice bit durability, as is often the case when PDC cutter attack angles are decreased or when PDC cutter counts are reduced to increase overall aggressiveness. By maintaining a sharp structure with minimal damage and dulling condition, the bit can drill longer while sustaining consistently high levels of ROP throughout the entire run.
Concave diamond element bits
A new cutting element that is enabling operators to improve ROP in medium-strength and interbedded formations is the StrataBlade concave diamond element bits by Smith Bits, a Schlumberger company. Concave diamond element bits complement the company’s 3D cutter element technology portfolio, which includes ridged diamond element bits and hyperbolic diamond element bits.
Ridged diamond element bits have demonstrated their effectiveness in improving cutting efficiency in hard and brittle rock types with formation strengths in excess of 15,000 psi. Hyperbolic diamond element bits are used to increase ROP in soft and plastic formations with formation strengths less than 9,000 psi. It was recognized that a gap remained to improve cutting efficiency in the medium-strength formations that reside between those covered by ridged diamond element bits and hyperbolic diamond element bits; as well as drilling through applications consisting of interbedded layers with unconfined compressive strengths (UCS) ranging from 5,000 to 20,000 psi. StrataBlade concave diamond element bits were designed with these exact applications in mind.
The new bits feature unique geometry cutters designed to save rig time and costs by delivering faster, instantaneous ROP. Their distinctive concave feature decreases the effective cutter back-rake angle that enables cutting deeper into abrasive and impact-prone rock. Its form, consisting of a pointed ridged tip with a thick diamond layer, improves point loading to enable deeper drilling and increased footage without adding WOB.
For deep lateral wells where weight transfer to the bit is a challenge, the cutting element delivers better torque response at the bit for superior steerability and conformance to directional plans.
The performance of concave diamond element bits has been validated with extensive laboratory scrape tests and simulations, which analyzed bit-to-rock interactions that confirmed efficiency gains versus other PDC cutter types. It is in these initial lab tests where engineers were able to get a first glimpse at the potential gains in cutting efficiency that could be achieved with the new concave shape. Additional testing was completed to validate the overall mechanical strength of the new concave shaped PDC cutter to ensure that it could withstand the harsh environments present in downhole drilling applications.
Together, the laboratory tests and simulations confirmed that the newly developed shaped cutter could increase cutting efficiency without compromising mechanical strength, avoiding a tradeoff often present with traditional PDC bit designs.
Once lab testing was complete, the new concave-shaped cutter was put onto the bit for testing in the field. In 2020, more than 100 field tests were conducted in North America, with more than 95% of these runs delivering significant improvement in ROP compared with their direct offsets.
Marcellus Shale
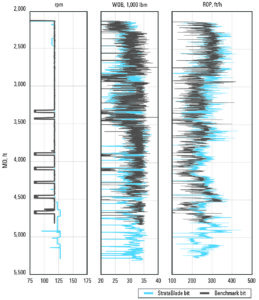
In early field testing, the concave diamond element bit’s ability to improve ROP and cutting efficiency without increasing WOB was validated in the Appalachian Basin, where formations comprise highly interbedded shale and sandstone layers.
An operator drilling 8 ¾-in. vertical intervals in the Marcellus Shale had previous benchmark drill bit designs that drilled shoe to shoe with minimal damage to the cutting structures. However, the operator desired improving drill bit performance to further increase ROP. The benchmark design incorporated ridged diamond element bits with a steerable motor bottomhole assembly (BHA).
To ensure ideal test conditions, the same BHA and bit designs were deployed except for the cutters, which were replaced with concave diamond element bits. The bits ran in an adjacent well on the same pad as prior bit designs with identical drilling parameters. Drilling the same interval, the concave diamond element bits averaged 263.8 ft/hr drilled. The next-fastest bit run on the pad was 239.4 ft/hr.
This improvement showed 10% increased ROP over the best run with the benchmark bit design and a 15% increase compared with the average offset performance. The concave diamond element bits drilled shoe-to-shoe intervals in single runs and delivered the highest ROP with the same WOB.
Haynesville Basin
In another field test in the Haynesville Basin of Texas, an operator wanted to reduce bit runs while drilling a vertical interval in an intermediate section of the Travis Peak and Cotton Valley geological layers. Drilling these interbedded and abrasive formations caused premature cutter wear and fatigue on conventional PDC bits resulting in additional runs, consequently lowering ROP and requiring the BHA to be pulled before reaching interval target depth. An offset performance study showed that for the 9 ⅞-in drill-out bit runs, the rate of shoe-to-shoe runs was about one in every three wells. Some intervals required as many as five bit runs.
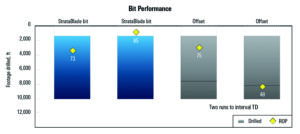
During the testing, three runs using concave diamond element bits in adjacent wells on the same pad drilled shoe-to-shoe intervals in a single run. These runs also increased ROP by an average of 28% compared with the offsets. This performance enabled the operator to eliminate bit runs while drilling to 10,000-ft measured depth, achieving higher ROP and maintaining bit durability.
Conclusion
Today, StrataBlade concave diamond element bits are being widely used in the US across all major shale play basins. Recent deployments have also expanded to Canada, Russia, Norway, Saudi Arabia, Kuwait and Brazil, in applications ranging from horizontal intervals in unconventional land wells to those in deepwater wells.
In the industry’s quest to improve bit performance, shaped PDC cutting elements offer a new opportunity to increase cutting efficiency that enables faster drilling across all rock applications. This provides a third dimension that builds on the improvements achieved in impact and wear resistance over the past decades. With improvements in cutting efficiency, operators are seeing how reduced on-bottom drilling time and expensive bit trips translate to saved rig time and, ultimately, overall well construction costs. DC
StrataBlade is a mark of Schlumberger.