Automated predictive frac control system taps operator’s machine-learning model to improve completion execution
Hess, Halliburton partner on Bakken pilot pairing automation with a predictive model to optimize for new surface efficiencies
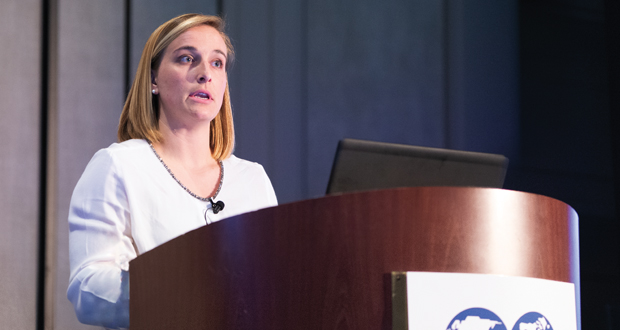
By Jessica Whiteside, Contributor
The technology behind what Hess called a “push-button frac” pilot is complex – combining automated hydraulic fracturing with predictive machine learning – but the potential payoff is as simple as it gets: a faster frac with better economics.
“What we are using this specific model for is surface efficiency optimization. Overall, we want to reduce time and material costs,” said Erin Butler, Senior Specialist Engineer for Hess, which conducted a pilot in the Bakken in partnership with Halliburton in 2021.
The project demonstrated the ability to upgrade completion performance with minimal human intervention by using the operator’s machine-learning model to accept data from, and provide tailored frac design guidance to, the service provider’s automated fracking system.
In a presentation at the SPE Hydraulic Fracturing Technology Conference in The Woodlands, Texas, on 2 February, the project team described the venture as “the first time a hydraulic fracture was conducted via automation with algorithmic integrated design improvement.”
According to Ms Butler, the successful pilot provides “the groundwork for operators and service companies to progress toward automation of hydraulic fracturing operations” and make further step-change improvements in frac design and execution.
“The overall vision of automation in hydraulic fracturing isn’t going to be tackled in one fell swoop,” she said. “It’s going to take small incremental steps to get there and really capture value from automation.”
Removing human bias
Traditionally, decisions to modify frac design during a job are made by engineers or supervisors on location. However, this can lead to inconsistent execution because, in addition to subsurface heterogeneity, these decisions are influenced by variability in the experiences and capabilities of the individuals and crews involved. It can also be challenging for these professionals to gain approval for modifications in a timely manner, leading to missed optimization opportunities.
Pairing automation with machine-learning models that can run 24/7 and process more data more quickly than possible for a human could avoid some of these pitfalls.
“Automating hydraulic fracturing processes can add value by driving consistency, removing human bias, reducing our EHS risk, eliminating waste and even enhancing our well performance,” Ms Butler said.
Automation and digital workflows are still relatively new to hydraulic fracturing, with testing of automated equipment beginning in the initial breakdown stage of completions in 2016. By 2020, Halliburton had introduced an automated fracturing system that the company says is capable of running completions from beginning to end. The system is described as a “co-pilot” that uses subsurface sensors, 3D visualization and other features to provide operators with greater control over fracture placement through “intelligent automation.” The system provides real-time diagnostic insights into factors such as pressure, rate and proppant concentration and enables automatic changes to fracking equipment, such as the blender and hydraulic pumps.
What Hess wanted to determine through the 2021 pilot, however, was whether the Halliburton system could be configured to accept inputs and direction remotely from an external source – a machine-learning model developed by Hess that would analyze both historical and real-time data from the job. The model is designed to assess pump curve characteristics and make on-the-fly recommendations for design changes to improve the frac based on specific optimization targets (e.g., reduce time or execution cost, maximize rate, etc). The model would then need to communicate these changes directly to the intelligent automation system for execution.
Hess trained its optimizer model on a data set of more than 150 Bakken wells. The model retrains itself with real-time data it receives during the completions process, improving its performance and prediction accuracy as the frac progresses. With this model, Ms Butler said, you can better capture why and when a decision was made and use that information in additional analytics.
Developing data workflows
The companies worked together to develop a data architecture that facilitated the secure delivery of data between the operator’s model in the office and the service provider’s system at the frac site. The resulting automated process feeds the frac equipment with the updated design change recommendations from the machine-learning model at an agreed-upon frequency.
“What we had to develop was a translation on how to take this prediction table and put it into a format that was digestible by the intelligent fracturing service,” Ms Butler said.
While the project team had intended for this process to happen autonomously, time constraints during the trial meant they weren’t able to get to the point where there was no human intervention to accept the model’s design suggestions.
“What we did get to was that we were able to stream the model outputs to the user interface of the intelligent fracturing system so it was just a quick acceptance and a copy-paste to the blender outputs,” Ms Butler said. Future iterations of the technology will remove that human step to enable seamless, closed-loop communication between the operator and service-provider systems.
To ensure that the optimizer model was functioning correctly, the pilot required human oversight of the design change protocols recommended by the model. This oversight involved a sign-off from the field supervisor and the engineer, who conducted a “final check that we were adhering to our boundary conditions and that there was no outlandish suggestion by the model,” Ms Butler said. “Then we gave the nod to the operator to adopt these model changes.” Such manual requirements would be phased out in future iterations following further vetting of the data architecture and boundary condition adherence.
Because the project used a joint service company-operator data stream, an important feature of the data architecture was the ability for both parties to maintain the security of their respective networks.
“Integration of the operator’s model with the service company’s automation-enabling equipment was developed without risk to either party in terms of security or the loss of intellectual property, providing mutual benefit,” Ms Butler said.
Proving the technology
The 2021 pilot took place on a four-well pad operated by Hess in the Bakken. For the first two wells, the team tested only the functionality of the Halliburton automated fracking system, without activating the machine-learning model. The automated system successfully and consistently placed the Hess fracs.
For the second two wells, tested in July 2021, the team brought the integrated machine-learning model into play and met the project’s goals of ensuring that the intelligent fracturing system received the model’s outputs at the designated frequency and under established boundary conditions. They also met another key goal: to avoid any downtime associated with the modeling process and acceptance of design changes.
A secondary goal of the pilot project was to better understand the machine-learning model’s performance and how it achieved the optimization targets. That analysis is now under way, Ms Butler said.
“Right now, we are investigating a few hypotheses that we have for why the model is behaving in the ways it did, and then we would like to take steps to fine-tune this optimization tool – the run times, the frequencies, the methodology – to best achieve our operational efficiency targets.”
Change, she added, is the only constant when it comes to developing automation. “Things that work well are going to stick, and things that don’t work well we need to learn from quickly and move on to our next task.”
She noted that there is no set methodology for hydraulic fracturing automation, and different operators pursuing the vision of a push-button frac might order their processes or data flows differently depending on their value drivers. However, she advised that necessary capabilities should include digital workflows, real-time data aggregation, edge devices and cloud computing, machine learning and artificial intelligence tool development, AI-enabled equipment controls and an integrated operations center.
Efficiencies like those emerging from this pilot align with Hess’ strategy for generating cash flow from its Bakken assets, which remain a critical component of its portfolio. Hess produced approximately 155 MBOED from its Bakken assets in 2021, and its 2022 production budget includes $790 million to fund a three-rig program in the Bakken. With those funds, the company expects to drill approximately 85 gross-operated wells and bring online approximately 85 wells this year. DC