Manufacturers pave path to hands-free drilling with automated tubular handling
Systems rely on advanced robotics and modular components to reduce need for manual labor, improve rig floor efficiency
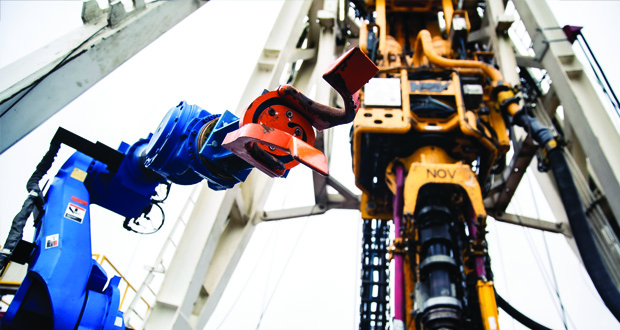
By Stephen Forrester, Contributor
As the oil and gas industry continues to modernize rigs and equipment, an area ripe for innovation is tubular handling. With so many processes on the rig floor and around the rig dependent on human work, the industry has long sought to understand ways of redirecting those workers to more critical tasks while taking them out of areas where there are likely to be major safety incidents.
Whether due to cost constraints, the industry’s aversion to sweeping change or system shortcomings, new products have often been implemented piecemeal, if at all, often leading to too much variability in results.
Through two of their latest technologies in this area, Schlumberger and NOV are attempting to significantly move the needle on tubular handling, driving the industry to lower well delivery costs and improve rig safety.
Robotic arms aim to enhance human assets on rigs
NOV is in the final stages of getting its ATOM RTX system ready for commercialization. It is a modular and fully automated robotics solution that can deploy up to three robotic arms on the drill floor.
A lower arm, working in conjunction with legacy equipment, can perform tasks such as tailing the bottom of stands, while an upper arm performs the transfer of the upper end of the stand from the setback/fingerboard to well center and vice versa. The third, or ancillary, arm can be installed between the mast and the drawworks, performing tasks such as doping, mud containment and stabbing assist. All arms are fundamentally the same design but used for different applications. Other configurations are also possible to accommodate existing rig floors setups and asset locations.
ATOM RTX, which syncs with NOV’s Cyberbase, Amphion and NOVOS drilling control platforms and multi-machine-control system, is designed to be scalable. It also integrates with a rig’s existing equipment package while automatically completing tasks that were previously manual. The arms operate simultaneously, and no human operator is needed to manage the individual robots. The system can be used both during drilling or tripping, as well as singles handling.
“About four years ago, we started to see a desire to accelerate the adoption of automation in the industry,” said Andrew McKenzie, Director of Robotics and Equipment Automation. “We then started looking into how we could further enhance automation on drilling rigs with respect to drill floor and red zone operations. Safety is paramount, so that came out as a top priority.”
Although safety was a driving factor in the system’s development, the company also recognized that the system had to achieve operational improvements. “Any system we developed had to augment the core functionality that the rig has to deliver on,” Mr McKenzie explained. “We needed a solution that would be consistent, efficient and, most importantly, reliable. There was no point in putting a system out in the market that worked well, but when it failed, it affected the overall performance of the rig.”
A focus area with the new system was on enabling rig crews to perform more critical tasks that require a human-oriented approach versus the repetitive processes typical of the rig floor, like tending to the mud system or observing process parameters. This, said Mr McKenzie, is very much in line with what NOV has touted as one of the benefits of its NOVOS platform – reducing manual processes and transforming rig crews from laborers and button-pushers to process directors.
“We’re using industrial robots in an oilfield application to change how repetitive tasks are done, with ATOM RTX operating in conjunction with the other components on the rig to enable a hands-free drilling operation,” said Product Line Director Robert Goodwin. “We’re not trying to replace the human assets on the rig – we’re trying to enhance them. These robotic arms are intended to be used as part of a hands-free drilling system.”
A lot of effort went into integrating the system with platforms like NOVOS. “We knew we couldn’t just take one of these off the shelf and put it on the drill floor and press a button,” Mr McKenzie said, noting that special emphasis was given to ensure full integration of the robotics system software into the broader rig software architecture. “This is one of the main areas where NOV’s engineering horsepower has been used, as well as the development of ‘end effectors,’ or the tools that go on the end of the robot.”
These end effectors change the functionality of a robotic arm in its given location, allowing it to perform certain tasks and, if necessary, to rapidly change to another task using a different end effector. A rack of end effectors specially designed for each task sits adjacent to the system, allowing each arm to equip itself to perform a given task on the drill floor.
Currently, available end effectors include a quick disconnect system, tailing claws, doping head, pipe stabbing assist head and modular mud bucket. NOV is also working on new end effectors to further expand the range of available tasks each arm can perform. “Now we have grip and spin technology, so we have a grip and spin end effector,” Mr McKenzie explained. “That allows us to pick up crossovers and spin them, whether horizontal or vertical. That ties into the BHA-type operations, taking hands off these very manual tasks.”
Over the past two and a half years, the ongoing COVID-19 pandemic also became a driving factor in the development of the ATOM RTX system, Mr McKenzie said, as crew movement became more challenging than ever.
Another factor over the past year was that drilling contractors, like many companies, began facing difficulties in securing labor to carry out critical tasks. Considering those challenges, along with the rise of remote operations, he said the company felt the time was right to introduce a system like ATOM RTX.
Extensive testing has been conducted at NOV’s test rig in Navasota, Texas. “We took a phased approach to testing, putting the lower tailing arm on the rig to examine the mechanical feasibility of using robots in this space,” Mr McKenzie explained. “After a successful trial using the lower arm to tail the bottom of stands in conjunction with legacy equipment, we installed a second arm on the diving board, and the rig was then used to drill a 12,000-ft R&D well. We were under a lot of pressure to make it happen, but the well was drilled on time, with no downtime by the drill crew and no issues with the system.”
Testing culminated with the placement of a third arm on the drill floor, focusing on ancillary tasks to assess how many humans could be removed from those processes.
The rig crew, as of early August, was still using the full three-arm system, even when the engineers were not there to oversee it. This is allowing NOV to obtain a “voice of the customer” analysis that can be used to better understand how potential customers will react to the technology.
While it’s too soon to say whether the system will drive a fundamental change in how the industry approaches rig design and crew function, Mr Goodwin said he believes what’s happening in other industries might be an indicator.
“Why did the automobile industry go to automation?” he asked. “They want to eliminate risk and inconsistency in operations in general, which is exactly what we’re aiming to do with this robotics system. We are eliminating inconsistencies for weather and other variables associated with drilling processes, making it predictable for drilling contractors to know that to drill a well of a certain size will take a certain amount of time, every time. Maybe that drives the industry to standardize. All we know for now is that we’re enabling people to do other tasks while drilling and tripping because this system is in place.”
The benefits of implementing robotics could also extend to the industry’s recruitment efforts, Mr Goodwin added. “We’re not always seen as a high-tech industry. Does this change that? Does this help enable new people get excited to work in oil and gas?”
Customer acceptance testing on the first ATOM RTX system began in August.
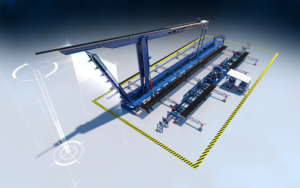
Horizontal tubular-handling system helps drillers reduce activity at well center
Schlumberger’s horizontal tubular handling system comprises two modular components — a hydraulic catwalk and an assembly table with integrated side-entry bucking machine — engineered to work together. The system is flexible and can be easily moved from rig to rig as needed. With the capability to enable makeup and breakout of double stands of casing and triple stands of drill pipe, the horizontal tubular-handling system allows well construction activities for various combinations of tubulars and bottomhole assembly (BHA) components to be completed away from well center.
“We’ve been looking at removing people from the drill floor for a long time,” said Domain Expert Aaron Bryant. “We knew that if we could do this, we could dramatically reduce the number of injuries on the rig. Since most rigs in the world are traditional rigs with manual pipe-handling operations, we wanted to reduce the activity at well center while improving well construction efficiency. By integrating a suite of technologies into one system, we’re now able to remove vertical activities and perform them offline and horizontally.”
The bucking machine is a unique component of the horizontal tubular-handling system. Most bucking machines have a closed-center headstock requiring tubular components to be fed in and out axially, requiring significantly more space to complete the operation. Top-loading machines, on the other hand, while requiring less space, take more time to make up pipe and casing. “We developed a side-entry bucking machine system with no doors on it,” explained Mr Bryant. “A casing double, for example, rolls straight out toward the catwalk once it’s made up. When you’re breaking out drill pipe or making up triples, you make a double, move it 30 feet, make the triple, and then it rolls straight to the catwalk. You don’t need all the extra space.”
The bucking machine is integrated into a single unit, with all tubular feeding — in and out and axially locating it with the bucking machine — in one system, controlled by one person through a common control system. This eliminates the need for independent hydraulics, as would typically be necessary in a warehouse environment, where 15 to 20 powered rollers feed pipe in and out, and each requires cylinders to raise that pipe up and down and align it.
“This is OK in an environment where the system is sitting on concrete and never leaves,” Mr Bryant said. “But what we had to do was find a way to move the system from rig to rig very easily, without all the additional hydraulics and complications. So, we integrated the system into one package that can be moved from rig to rig during one road-legal move.”
The system’s modularity is another key feature, as it can be moved from rig to rig, or even field to field. “You don’t always need the integrated bucking machine/assembly table at the rig site,” Mr Bryant explained. “When field conditions and logistics allow, it can be shared over several rigs.”
The system can even be used as a logistics hub — for example, in areas of the Gulf of Mexico, the system is located centrally, and doubles of casing are transported to the rig to offload.
A benefit of having the full system on location is the ability to have what Mr Bryant calls “just-in-time casing delivery,” which means that the casing can be made up in doubles horizontally faster than it can be run in the hole, further reducing footprint and increasing efficiency. “Instead of laying out 15,000 feet of casing horizontally, you can leave it in bolsters, and we’ll make up several joints as a buffer, then make it up just in time to keep it going,” he said. “We can do the same thing with drill pipe, and we can build those stands faster horizontally than we can vertically. This allows you to transport from location to location without breaking the stands down, depending on the needs of the operation.”
Schlumberger sees the system as an enabler not just in reducing activity on the drill floor but also in the future evolution of rig design — a future where rigs won’t need to have a setback. With all tubular handling done horizontally, the driller could be located in the most optimal location without needing to make room for the drill pipe first.
Furthermore, horizontal tubular handling would eliminate the need for a fingerboard, as there would no longer be a human on the derrick or mast. While this would represent a dramatic shift in current rig and crew configurations, “this is totally doable. It’s all about building the confidence to get there,” Mr Bryant said.
In terms of efficiency improvements, the company has already seen quantifiable results. “Based off field operations in the Gulf of Mexico, we’ve seen that running in doubles as opposed to singles reduces casing-running times by up to about 45%,” Mr Bryant said. “Running in doubles also reduces the number of connections at well center by 50%, and studies of BHA data have shown that the system decreases the time necessary for BHA makeup and programming up to 65%.”
Additionally, he noted that the system improves running time, reduces open-hole exposure time, helps get back on bottom sooner, and enables rig-move time savings due to the pipe handling being done offline. Due to restrictions when working in certain scenarios — such as in Pennsylvania, where an operator would need more setback due to deeper wells — the system could allow some of the racking to be done horizontally on a rig that was previously active in the Permian, which would have otherwise needed a major overhaul.
In the future, the horizontal tubular-handling system could become part of Schlumberger’s DrillPilot digital control software, where the full suite of rig equipment could be controlled together instead of as individual machines. “We want this to, one day, be a fully hands-off system,” Mr Bryant said. “While we don’t know if it will be fully autonomous, we can definitely see there needing to be only one or two people, and no one manually handling pipe or casing. We’ve done it vertically — now we need to do it horizontally.” DC