Going beyond LTIs: Industry must reassess how it measures safety
Not incorporating high-potential incidents into evaluations of safety performance creates blind spot for company, industry
By Linda Hsieh, managing editor
Søren Risgaard Jeppesen is senior director of QMHSE for Maersk Drilling.
From your role leading the HSE department at Maersk, what is the company focusing on going into 2014?
Maersk Drilling, like many other companies, is really focusing on how to get to zero incidents. The drilling industry is growing very rapidly, and we are onboarding a lot of new crews. Getting that message of zero incidents out to our employees is fairly easy, but it’s not as easy to ensure the message is fully understood. We need to get to a level where the culture of the company is embedded in daily operations. That’s a critical task that will be vital to our success as an industry. Particularly in view of changing legislations around the world, including in the Gulf of Mexico and the EU, we must have a good safety culture.
What does safety culture mean to you?
Today, the industry predominantly measures safety performance through LTIs. I believe this is misleading. If we are not incorporating high-potentials into the metric, then we are creating a blind spot for ourselves. The industry as a whole has been working for many years under the assumption that an LTI-free environment equals good safety culture, but we’re realizing that’s not the case. We’re actually missing out on a number of elements and near-misses that have very high potential.
For example, if you have Company X with 10 LTIs but no high-potential near-misses and Company Y with zero LTIs but a lot of high-potential near-misses with high potential – which do you think is the better of these two companies, culture-wise? This is something that needs to be addressed. We need to figure out what are we measuring, and is that the right thing to measure? It’s a tough topic, and it can’t be changed overnight, but it needs to be addressed before we can really get to zero incidents; otherwise we’re just fooling ourselves.
The IADC Drilling Near Miss/Hit Report does point the industry in the right direction, but it’s not enough in itself. The culture won’t change so long as the industry as a whole is focused solely on LTI count and frequency. We have to dig deeper.
We need a basic understanding of what safety culture is. We can’t define it as a global term. I think it’s something that needs to be defined by individual companies. What does safety culture mean at your company? That question forces you to really think about what you mean when you say safety culture.
What would the regulators’ role be within these efforts?
Once you’ve figured out what your safety culture really is, regulators can come in and inspect whether you actually have the culture you think you do. Having a safety management system or a drops policy is not the same as having a safety culture. The company has to really think about it and make sure it’s embedded into the organization. You can’t just have words and not have anything to back it up.
When you break it down, the industry and the regulators all want the same thing. Regulators want a safe work environment; so do we. We all want the same bottom line. It’s just, how do we get there?

What about the operators’ role?
We did some studies after Macondo that led us to start questioning the operators. Basically we’ve gone to them and asked them to prove that they are in control of their safety-critical barriers. Some are more open to this, and some are not, but it’s really demonstrated to me that, if we really want to have a safe working environment, we have to stop looking at this as “them” and “us.” This has to be a partnership.
To set the foundation for that partnership, we need to align our understanding of safety cultures and what we mean when we use certain terms. We need common understanding, common ground.
You said safety culture should be company-specific. Do you think each company should have a uniform safety culture across its global operations, or should it be varied by region, perhaps due to cultural and geographical differences?
My take is that there shouldn’t be different standards. If your company works globally, you should work to the same standard. Why would you go to a lower standard in some areas? If you allow things to be different, that shows the wrong safety culture. You can see this reflected in the EU regulations, too. Their message is that, if you want to drill safely in our backyard, then you’ll have to do the same in our neighbor’s backyard.
You mentioned earlier that you don’t think LTI is a good safety metric for the industry, particularly as it does not address near-misses. How can we measure potential for incidents?
I don’t have a fixed answer to that question, except to say that we should start looking at something as simple as “How do you track high potentials?” Every operator has a different version of what a potential is, and we should look at having defined standards. There are some existing standards, but they’re not adopted globally.
I should also clarify that potential does not mean pre-incident potential but post-incident potential – the potential that an incident could have had if it had gone wrong.
The issue is really around whether we are measuring ourselves by the right criteria. If we’re not, then what are the right criteria? I agree, this is not a simple task, but we need to be ambitious about it. Just because it’s difficult doesn’t mean we should not do it or try to do it. Especially now, as regulators are coming in and telling us whether they think we have a good safety culture, this is vital. I like to stay ahead of the regulators and be able to show them this is something we’re already doing when they arrive.
In the end, it’s not the regulator who should ensure our units are safe. It’s us. It’s our task that nobody else can do.
What are the challenges to embedding a good safety culture into the organization and its daily operations?
I think the biggest challenge is communication. This doesn’t mean this is all just a communication exercise, but it really is important to help your employees understand your safety culture. Even when the CEO of the company is actively communicating the message of zero incidents, sometimes the message gets lost or distorted as it moves down the ranks. This ties back to what the culture of the company really is: how are we communicating, what level of accountability do we have in each position, etc. Why do we sometimes still see people not comply with procedures? What is it that makes a skilled and trained person decide not to follow a procedure?
There are a number of reasons for that, but we need to figure them out, and we need to face them.
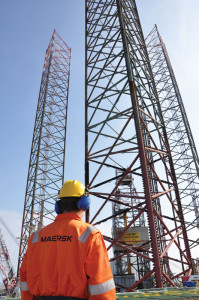
As you mentioned, companies are doing a lot of onboarding of new crews, sometimes newhires and sometimes from peer companies. What are the most important considerations during this process as far as safety?
If the recruit is coming from another company, it’s very easy for them to fall back to the culture at their previous company. Not that it’s a better or worse culture, it’s just different than ours. So we have to be careful about the onboarding process.
I always try to go out to meet our newcomers when they are training because it’s critical that we help them understand that we’re not just saying words, that we actually mean what we say, whether it’s “You’ve got time to do a job safely” or “We expect you to stop a job if there’s potential to harm someone.”
We really struggle sometimes to get that message across even if I’m standing there telling them. It’s vital to have them actually believe this is what we want.
In recent years industry has shifted away from simply training to ensuring specific competencies for our personnel. How do you see this shift reflected in the programs developed at Maersk Drilling or across the industry?
One thing we realized after Macondo was that industry has trained individuals to be competent, but what we’re really interested in is not individual competency but field competency. It’s the ability to act and interact with each other as a team. It’s the ability for somebody to say “stop” even when that person is not the most senior person on the team. I think our industry has realized that we need to train in teams.
Individual competency is fine, but it doesn’t provide us full shelter from an incident. We normally say that the person in the driller’s chair is our last barrier. That is true, and we should train that person, but we have to remember that he also has to rely on his team to complete his tasks. It’s not just about him but the team around him.
Maersk has invested heavily in a new training facility in Svendborg, Denmark, and the training setup at the center is aimed exactly at building team competency.
We have two drillships being built in South Korea that will be going to work in the Gulf of Mexico. Recently we gathered the whole crew for the first drillship and sent them to Svendborg to train in the simulator as a team. It was the first time we had the crane simulator, the engine room, the bridge and the drill floor simulators all connected to work with one another. A lot of these crews were amazed by the reality of the training and how much they were able to gain from simulations. No question, it was an amazing experience for these people, and this type of training justifies the investment we put into the center. If we can get these people well trained so they’re successful on our drillships from day one and not have any incidents, then this is a priceless investment.
From your view as a safety professional, how is automation and mechanization impacting safety on today’s rigs?
I think it’s important to always strive to be automated. From an operations perspective, I think automation does create some challenges. But from a strictly safety perspective, it’s fantastic. I’m not advocating that we have a fully automated rig, because we still need people out there even if we take people away from the high-potential areas. But from an HSE perspective, I think it’s the only way we’ll do things going forward.
Operators around the world have been emphasizing process safety much more heavily since Macondo. What kind of trickle-down effects have you seen at drilling companies, perhaps due to operator requests?
I think that if a drilling contractor just adapts whatever the operator tells them, they would be moving themselves into danger. Like with safety culture, we’ve looked closely at what process safety means to us. We worked through the API standards on process safety and got cooperation from a number of operators. One thing that became quite evident early on was that we couldn’t piggyback on what the operators have because it is very different from what we have or what we should have.
A lot of people say we haven’t had process safety in the drilling industry, but I would say that’s not true. Look at our well control manuals. It’s all about barriers – how you maintain them, how you evaluate them and how you measure them.
At Maersk we’ve established a separate group that deals only with process safety, and one of the first things that came out of that group was an eye-opener for me. If you look at process safety from the perspective of how to manage barriers, it is a lot more difficult for drilling contractors than for upstream companies. A drilling contractor has a lot more barriers, especially if you think about the stability of rigs and stability of gasses, which are key elements of process safety.
When we are finished at Maersk in deciding what process safety means to us, I think we’ll be able to go out and tell operators that our procedures are much more operative than theirs because we have a lot more difficult operations and tasks at certain points and times.
Do you think industry also needs to define what constitutes a barrier?
This is a personal view, but I think using the term process safety in the drilling industry is wrong. I think we should call it barrier management because that’s what we’re all about. A governmental report had defined process safety as keeping hydrocarbons in the pipes, and that’s fine for a process unit, but we are not a process unit.
As drillers, we need to talk about barriers, and I think we have a good understanding of barriers and what they do. The difficult part is measuring them and ensuring they’re intact.
What role does management of change play in all this?
When we analyzed process safety and looked at the gaps in areas where the organization felt we were lacking, one thing that came up with a high score was management of change. We went out and did comprehensive interviews offshore, and a clear-cut suggestion was to take the heavy evaluations off their shoulders. Another thing we identified was that a lot of people didn’t know what management of change was.
We’ve now done a rewrite of our management of change procedures and are about to go live with it. It will be mandatory learning for everyone onboard. It is in three tiers, but everyone will have at least a basic understanding of what it is.
I think, to a lot of companies, management of change has mostly been another paper exercise, and people didn’t really see the upside to it. There are a lot of upsides, of course, but they may not be so clear when you’re looking only at the short term.
Industry is hiring a lot of younger workers. Do you think we’re doing enough to help this new generation see this as a lifelong career rather than just a job?
We have what we call Plan 3000 that helps us define what we need to do to train new people, down to details such as when we can start taking them from existing units and put them on new units. We don’t downgrade the level of readiness on each unit just because we need to man our new units. I feel fairly confident in saying that we’ve put a lot of effort into hiring these people and putting them into the right environment, at least at Maersk Drilling. We’ve certainly put a lot of effort into their onboarding process. In fact, a lot of them say that this is the first time they’ve seen a company do so much for a newcomer.