Modified cement head cuts rig-up time, risks
Integration with top drive casing-running system improves zonal isolation, bonding in Caspian
By Tracy Cummins, Weatherford International
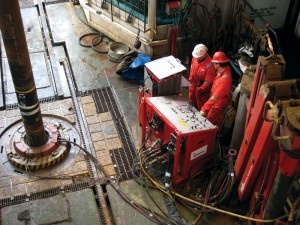
Integration of a remote-controlled rotating and hoisting cement head with top drive casing-running operations is cutting transition times between casing-running and cementing operations in Caspian Sea wells by reducing equipment rig-up time. The combined system allows rotation, when applicable, and reciprocation of the string while circulating, cementing and displacing to facilitate cementing best practices.
While offset wells exhibited total losses during cementing, which led to poor isolation, subject wells have been cemented with reduced losses and improved bond logs.
The success of the cementing head has led to its adoption for use in cemented tie-back liner applications and in landing subsea casing strings with full-bore landing strings to cut costly semisubmersible rig time and casing string static time.
Caspian Sea challenges
In the Caspian Sea, traditional methods for landing and cementing casing strings in surface wellheads have experienced many operational problems, including moderate to total losses while cementing casing, poor zonal isolation with hydrocarbon crossflow and flow to surface, and poor cement bonding and placement.
In addition, the methods presented a safety risk because of extensive manual handling of the cementing equipment and man-riding operations.
A key source of these problems was the time required to install a standard cement head. The time to rig-up the conventional equipment prevented circulation for as much as one hour. During this extended transition time, static thixotropic well fluids thickened into a gelled state before cementing operations could begin.
The gelled fluids resulted in channeling, mud and cement losses, and poor cement placement. To avoid these problems, the operator needed to reduce the transition time between running casing and being able to circulate, reciprocate and, ultimately, cement.
The Caspian region has a history of successfully working with remotely controlled top drive casing-running tools and casing string rotation in open hole. Weatherford International’s OverDrive top drive casing-running system combines the functions of the main hoisting casing elevator, power tong, fill-up/circulating tool and bails, or single-joint elevators, into one system.
The system connects to the rig’s top drive and requires no permanent interface with the rig. The main component of the system is the TorkDrive, which enables hands-free pickup and makeup of casing joints. It also adds the ability to immediately rotate, reciprocate (or push down) and circulate the casing string into the well. This facilitates real-time hazard mitigation in problem wells, high-angle wells and extended-reach wells while enabling drilling with casing and enhancing cementing best practices.
Cement head advance
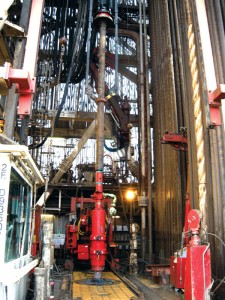
In the Caspian application, time required to install the conventional cementing head meant circulation and reciprocation was delayed during the transition. To reduce transition time and manual handling, the Caspian Sea teams modified an existing remote-controlled top drive cement head and integrated it into existing top drive casing-running operations. This innovation allowed the cement head to transition quickly to the casing landing string with minimal manual handling, cutting the transition time from one hour or more to approximately 10 minutes.
The modified cement head was picked up as the last joint in the landing string, eliminating the need to rig-down any tubular-handling equipment after the casing string was run and enabling immediate circulation and reciprocation of the casing string.
While remotely controlled top drive, rotating/hoisting cement heads have been used in the industry for years, they presented similar installation challenges, as with conventional cement heads. Installation still required manual handling and transition time to rig-down the casing elevator and bails and rig-up and connect the cement head to the top drive.
To date, the head has been used in more than 17 regional applications and has been accepted as a tool to improve cementing and to increase efficiency. Installations in the field include 9.625-in. and 13.375-in. casing strings up to 20,000 ft in length.
Use of the device has broadened to include improving landing efficiency and cementing for liner tie-backs and casing strings on subsea wellheads.
Project overview
The Caspian project started with the modified cement head being pre-assembled and loaded with plugs; it was tested before delivery to the platform.
On the rig, the casing string was run hands-free using the top drive casing-running system. The cement head was picked up with minimal manual intervention and moved to the landing string with the top drive casing-running system, which allowed circulation through the top drive to begin immediately. This process kept the casing and well fluids in motion to eliminate gelling.
Cement plugs were remotely launched, and cement was pumped. The casing string was reciprocated through the entire operation to allow higher displacement rates, reduced formation pressures and improved cement placement.
Job summary

The cement head modifications included the addition of casing pup joint on top of the head to match the casing size being run. Below the pup joint, a safety valve and crossover were added to isolate cement from the top drive. The cement head included an upper swivel sub, flow-around plug cage assembly and bottom-casing adapter. A pup joint the same size as the casing was connected at the bottom of the assembly. The resulting assembly was approximately 41 ft in length, similar in length to a joint of casing.
Pre-assembly at the workshop included installation of the job/size-specific components.
A pressure test was performed on the entire tool before loading the upper and lower cement plugs. An anti-tamper lock was installed on the remotely controlled plug-launch system for transportation to the rig.
Preparations continued offshore, where a low-torque valve with a short cement hose was installed while the cement head was on the pipe deck. Simultaneously, the casing string was run hands-free using the top drive casing-running system.
The casing string, casing hanger and landing string were run in hole and reciprocated and circulated before picking up the cement head. A crane moved the cement head to the pipe conveyor, where it was lifted into the derrick using the top drive casing-running tool. The process was the same as handling a standard casing joint.
Once the cement head was in place, circulation was initiated and hanger-landing operations began. The pre-installed cement hose was connected at rig-floor level.
When the casing hanger land-off was confirmed, the casing string was picked up, circulated and reciprocated to clean the hole. The cement line was flushed and tested before opening the low-torque, side-entry valve and closing the safety valve on the cement head assembly.
The bottom plug was then launched by remote control, and the lead and tail slurries were mixed and pumped, followed by launch of the top plug and displacement of the cement.
Tangible results
The combined technologies were credited with reduced transition time between casing-running and cementing operations, from more than one hour to 10 minutes. The ability to apply cementing best practices led directly to improved zonal isolation, confirmed by the cement bond log. The planned top-of-cement placement was reached, and a seal was achieved inside the casing shoe. An annulus pressure test was successful, and no losses were experienced.
Safety was also improved by reduced manual handling of equipment and the elimination of man-riding operations. The cement head was located at an easily accessible height over the rotary table.
Liner tie-back
In two other applications, the modified cement head has been used in cementing casing liner tie-backs in deeper and higher-pressure wells. Placing cement behind the tie-back seal assembly enhances safety by extending the cement pressure barrier up the annulus above the liner hanger.
The modified cement head also can be useful in landing the liner and cementing it. Conventionally the process would require considerable time to rig-up equipment, such as the cement head and elevators, to move the string up and down.
In this procedure, the tie-back liner is run in the hole and into the liner polished-bore receptacle (PBR) to establish precise casing land-off depth. The tie-back string is then picked up and spaced out for the casing hanger, and the cement head is installed as the last joint of the tie-back landing string.
The seal assembly at the bottom of the tie-back string is ported to provide communication with the tie-back annulus. When the tie-back seals enter the liner hanger, PBR ports are covered, and pump pressure rises to indicate accurate setting depth with the hanger landed off in the wellhead.
The tie-back liner is then slightly pulled up to re-expose the ports, and the cement is pumped and displaced. When the cement is fully displaced, the tie-back seal assembly is lowered and re-entered into the liner hanger of the PBR. With the casing hanger landed, the cementation ports are isolated from the annulus.
Subsea landing
The most recent use of the modified cement head was for landing casing strings in a subsea application performed from a semisubmersible, with reduced rig time as the key objective. The water depth in this application was relatively shallow, at about 1,000 ft.
Standard procedure for landing a casing string in the subsea wellhead is to convey it with drill pipe. As with conventional casing operations on surface wellheads, the transition time between casing running and drill pipe landing operations could be improved, and the well fluids could remain static. Also when landing casing strings with drill pipe, cementing plugs in the casing string are released by smaller darts or balls dropped through the drill pipe. While generally reliable, the balls or darts add another mechanical step to the process and introduce the possibility of a failed plug release. The smaller ID also reduces flow rates necessary for effective hole cleaning.
By using a full-bore casing string to land the casing string in the subsea wellhead rather than drill pipe, transition times were dramatically reduced and eliminated the need for subsea plug release with darts or balls and drill pipe flow-back tools.
Landing with a full-bore casing string allowed the casing hanger to be picked up and run in hole with no delay. Continuous running and circulation reduced the chance of hole instability induced by long static conditions.
Another innovation by the Caspian team is the use of three cementing plugs. While top and bottom plugs are typically employed, the new cement head can be loaded with three plugs. The first sacrificial plug is pumped down initially to calibrate the rig’s pump efficiency before cement displacement or as an additional barrier between cementation fluids.
Best practices
Innovative modification of a rotating cement head in combination with a top-drive casing-running system kept fluids moving to improve cementing on surface and subsea wellhead casing installations. Bond logs showed improved zonal isolation and cement placement as a result of being able to apply the best practices.
SPE/IADC 139909, “Remotely Operated Top Drive Casing-Running System Combined with New Cement Head Enables Major Oil Company to Improve Zonal Isolation and Cement Bonding with Enhanced Safety and Efficiency in Caspian Sea,” was presented at the SPE/IADC Drilling Conference, 1-3 March 2011, Amsterdam.
OverDrive and TorkDrive are registered trademarks of Weatherford International.