Rig technologies key enablers in factory approach to drilling
By Jerry Greenberg, contributing editor

Drilling and completion technologies have helped US shale plays to gain more attention than even a few years ago. Vertical wells used to be the name of the game in some oil-rich areas such as the Niobrara shale in the Denver-Julesberg basin in parts of Colorado, Wyoming, Kansas and Nebraska. Very few horizontal wells had been drilled in the Niobrara until a few years ago.
Drilling contractors have helped the boom by building fit-for-purpose rigs with enhanced drilling capabilities that reduce operational cycle times and costs. Rigs built for the Bakken are winterized, and most also have skidding capabilities for pad drilling. Better fracturing and completion techniques allow operators to drill longer horizontal laterals to optimally drain the formation without having to drill additional wells.
Unit Drilling
Unit Drilling Corp owns and operates 122 rigs and is active in virtually all US shale plays, from Haynesville, Barnett and Eagle Ford in Texas to the Woodford, Cana Woodford, and the Mississippi and the Marmaton plays in Oklahoma.
“The interesting thing about the Mississippi and Marmaton plays is that both are targeting shallow formations between 5,000 and 7,000 ft before going horizontal,” said John Cromling, executive vice president for Unit Drilling. “That opens up a new area for another class of rigs, 1,000-hp rigs that are equipped for horizontal drilling.”
Unit Drilling also has rigs contracted in the Niobrara in southwestern Wyoming and is active in the Bakken.
Key rig technologies
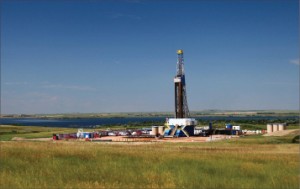
“Shale plays have progressed from vertical wells to highly deviated wells to horizontals, and horizontals with long laterals,” Mr Cromling said. “Drilling rigs evolved accordingly.”
He listed five key technologies that helped rigs to successfully drill the various shale plays, and each has helped to reduce operational cycle time and/or improve safety.
First is top drives. Second is larger and higher horsepower mud pumps, “because hydraulics are the key to drilling horizontal wells,” he explained. “The pre-eminent factor for drilling horizontal wells, much more so than the hookload of the derrick or drawworks horsepower, is hydraulic horsepower.”
The third technology is the mud system. “During horizontal drilling with high rates of penetration and with a large volume of solids being removed during the process, a good mud system is necessary to remove the solids,” Mr Cromling explained.
Another key area is the drillstring. “We are doing things with drillstrings now that we had been taught for 50 years not to do,” Mr Cromling said. “Pipe in compression, for example, and running heavy-weight pipe instead of drill collars and running it above the drill pipe.”
The fifth technology is skidding systems. “All of the shale plays are in the development process to some extent,” he said. “Most of the rigs in the Barnett shale can skid, and a lot of wells in the Bakken are at the development stage and they are drilled with rigs that can skid over multiple well pads.”
“It could take as little as three hours to prepare for the skidding operation and another three hours to restore the unit for drilling operations, while the actual move is usually less than one hour,” Mr Cromling said.
Other equipment that helps reduce operational cycle time includes a BOP handling system, which is critical for rigs that skid from wellhead to wellhead. The system picks up the BOP in a single unit from one wellhead, suspends it in the rig’s substructure while moving and then lowers it to the next well via hydraulic winches. “All of our skidding rigs have BOP handling systems, and it is a key factor in saving a lot of time in the preparation and restoration of the rig when skidding,” Mr Cromling explained.
Some operators also prefer the hydraulically operated catwalk, not necessarily because it saves time but because it eliminates third-party service and improves safety.
It’s interesting to note that most of Unit Drilling’s rigs do not incorporate cyber chairs with joystick controls. “We have some rigs with joysticks and a lot of rigs that do not,” Mr Cromling said. “Most of our newbuild rigs do not use joystick controls. Some people are convinced that if you don’t have a joystick your rig doesn’t have all of the new technology that is available,” he continued.
“I’m not against them, I just don’t think that is the only solution.”
When asked if using a rig without a joystick is more of an operator preference, Mr Cromling said, “That is more my preference. I think our rigs drill just as fast and efficient” as rigs with joysticks and automatic drilling systems.”
Anadarko

Anadarko Petroleum’s total 2011 capital expenditures are expected to be between $6.2 and $6.6 billion, with about 10% allocated to US shale plays. In the Eagle Ford, the company increased its average estimated ultimate recoveries to more than 450,000 barrels of oil equivalent per existing well. Its 200-plus planned wells for 2011 also signify a doubling of drilling activities from 2010 levels.
In the Marcellus, Anadarko plans to operate 10 rigs and participate in more than 250 wells this year. “The Marcellus will continue to be the only domestic dry natural gas field where the company will be actively drilling due to the play’s proximity to premium natural gas markets that enhance already robust economics,” the company said in a news release.
“Anadarko had nine rigs operating in the Marcellus play as of late March,” said Steve Bosworth, vice president of worldwide drilling for Anadarko, “including one rig that spuds and air-drills the vertical section of the wells from a multi-well pad to the kick-off depth to begin drilling the horizontal lateral portion.”
The company said it will continue to invest in other emerging onshore oil plays, including Bone Spring, Avalon shale and Wolfcamp in the Permian Basin, and the horizontal Niobrara play. Anadarko was operating two rigs in the Niobrara in late March and expected to increase that to three rigs by early April. “We are drilling Niobrara wells on a limited basis at the moment,” Mr Bosworth said. “It’s still early in the evaluation, but we hope to be running six operated rigs there by the end of this year.”
Reducing operational cycle time, costs
Mr Bosworth is convinced that, even if some line items are higher in cost than other methods resulting in the same end, operators will always save money by reducing the operational cycle times. Anadarko looks for higher-quality, higher-technology rigs for its horizontal shale drilling programs.
“The reason we feel we do as well as we have on the operational end is by utilizing these higher-quality rigs,” Mr Bosworth explained. “We look for a rig that will not compromise safety, and in fact improve safety, while improving our operational cycle time.”
He said the automatic catwalk is a safety improvement and eliminates additional third-party service personnel on location. He has similar feelings about separate crews to run casing. “Basically we are connecting two pieces of pipe,” he said. “It should not be dramatically different for a rig crew to run casing versus having a third-party casing crew and timing the logistics of that crew to the rig.”
Anadarko has been able to eliminate having a third-party casing crew about 20% of the time, but Mr Bosworth believes that will increase not only for Anadarko but across the industry. In time, a rig crew running casing will become more proficient at it, he added.
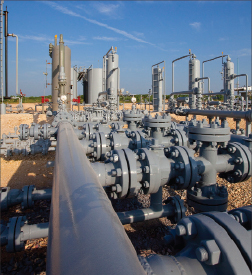
Pad drilling has also brought operational and economic benefits by allowing the company to batch together certain operations and “make it more like a manufacturing process,” Mr Bosworth said. “We are trending toward operating rigs with skidding capabilities because they are becoming more important to us from an operational efficiency standpoint by moving from wellhead to wellhead in a matter of hours rather than days.”
Mr Bosworth is not convinced that all technology is necessary from an economic standpoint. For example, while some operators often use rotary steerable systems in horizontal shale plays, “we think we do well with conventional tools depending on the particular area,” he said.
On the other hand, Anadarko’s success with rotary steering is resulting in increased use, depending on the area. “We are very encouraged by the rotary steerable wells we drilled in the Eagle Ford,” he said. “About 10% of those wells are drilled with rotary steerables, and I think we will be at about 50% during the next month or two. If you really want to get the consistent, repeatable good results, you are going to have to do that with technology.”
FlexRigs well-suited to shales

Helmerich & Payne has been building FlexRigs since the late 1990s and the A/C drive FlexRig3 since 2002. Today, the company boasts a 100% utilization rate of more than 200 FlexRigs in its US fleet. Most of them are working in shales.
“From our perspective, for the shale and unconventional plays, the more complex directional and horizontal wells, you need to begin with a platform that is A/C variable-frequency drive,” said John Lindsay, H&P executive vice president and COO. “We believe those rigs are the most efficient in the industry from a drilling performance viewpoint.”
The company has about 50 FlexRigs in the Eagle Ford, 21 in the Bakken, 20 in the Cana Woodford in Oklahoma, 16 in Haynesville (down from 29 last year due to low natural gas prices), and 11 rigs in the Barnett (down from about 25 rigs at the peak, also due to lower gas prices).
The FlexRig design concept is better safety and efficiency. “There are significant time savings to be gained in addition to the drilling process that benefits from lean manufacturing concepts,” Mr Lindsay said. “Only about 30% to 40% of the total well cycle is drilling; other areas for improvement include running casing, BOP nipple up and down, tripping pipe and moving the rig.”
The industry is also working on systems that will use real-time downhole data, for example, to deliver better performance based on the well that is being drilled, Mr Lindsay said. “With unconventional plays, there is a much more focused approach on factory delivery. The industry is set up much better today to look at a factory approach to exploiting reserves, which is a continuous focus on high-performance drilling.
“There also are a lot of lean techniques that go along with that – fit-for-purpose lean technology that continues to drive down drilling times by driving waste out of the process,” he continued. “After all, that’s what we are doing – we are manufacturing a hole.”

About 450 of the approximately 1,700 rigs working onshore US are A/C drive rigs, Mr Lindsay noted, and H&P owns just over 40% of those 450 units. There are also more than 700 mechanical rigs working in the US today, and it is estimated that over 200 of those are drilling in unconventional shale plays. But he added, “It’s not a function of the (mechanical) rigs not being able to drill the well. It is a function of the rigs not being able to drill the well as efficiently and economically as an A/C drive rig.
“Drilling has become more complex,” he continued. “Several years ago only 30% of the rigs working in the US were drilling horizontal and directional wells. Today, it is a direct inverse of that, with over 70% of the rigs drilling horizontal and directional wells. And the horizontal laterals have increased in length an average of 30% to 50% over the past two years.”
Those factors are why A/C variable frequency drive (VFD) technology will continue to gain market share, Mr Lindsay believes. “A/C VFD technology has enabled the deployment of the first generation of true high-efficiency multi-parameter electronic drillers,” he said.
H&P is able to drill concurrently using multiple parameters such as weight-on-bit, torque, Delta P and rate of penetration compared with a traditional auto driller that controlled only weight-on-bit. “We are just scratching the surface of what these systems will be able to do in the future.”
Many of the company’s rigs can skid over multi-well pads, and it manufactures its own skid system rather than buying from a third party. The skid system for its onshore rigs was adapted from its bidirectional skidding system used for offshore platform rigs, and in 2006 the first FlexRig4S unit was introduced in the Piceance Basin in Colorado that was capable of drilling 22 wells on a single pad. Shale development programs typically use drilling pads with between three to 10 wellheads, and this same system is being used today in the Marcellus, Bakken, Barnett and Eagle Ford.
Brigham Exploration increasing Williston fleet

Brigham Exploration said it will increase its operated fleet to 12 rigs this year in the Williston Basin’s Bakken and Three Forks plays by adding a rig every month beginning after May, when an eighth rig joins the fleet of rigs Brigham operates. “Accelerating from eight to 12 operated rigs is anticipated to increase Brigham’s drilling pace by approximately 44 gross wells per year” when the 12-rig level is met, which is anticipated to occur by September 2012.
“We are going to drill about 11 gross wells per rig per year,” said Erik Hoover, operations manager for Brigham. That translates into about 100 wells during 2011 and increasing to about 130 wells in 2012.
“With oil prices the way they are, liquid-rich fields are king,” Mr Hoover said. “Some plays are liquid rich, but the Bakken is probably the only true oil resource shale play.”
All of Brigham’s rigs in the Bakken are Nabors rigs, and the operator recently contracted two newbuild Nabors B Series PACE rigs. “I think many of the future Williston Basin rigs will be newbuilds because we’re now in more of a manufacturing mode, and newer rigs will likely be able to ‘walk’ from location to location and therefore reduce drilling costs,” Mr Hoover said.
Reducing drilling and completion times
- Nabors Drilling Rig 266 drilled Brigham Exploration’s Abelmann 23-14 #1H well in the Bakken Shale, which underlies Montana, North Dakota and parts of Canada. Initial production from this well was 4,169 bbl/day of oil equivalent with 33 frac stages. Nabors believes it holds the largest market share in the Bakken. Nabors photo courtesy of Jim Blecha Photography
Brigham’s wells average 17-23 days to TD, including a 10,000-ft vertical section and a 10,000-ft horizontal lateral. Three years ago, these wells took 30-35 days to drill.
Better drilling techniques account for some of the time reduction. For example, some operators who use oil-base mud in the lateral section are drilling 30-day wells. “We use oil-base mud in the intermediate section of our wells and brine water in the lateral,” Mr Hoover explained. “We typically set the bar at 20 days, but our record well was drilled in 14 days.
“With brine water we can drill up to 2,500 ft per day, but with oil-base mud we are lucky to get 1,000 to 1,200 ft per day,” he added. Most of the time, it would make sense that oil-base mud would result in a slicker downhole environment, reducing drilling time. However, when viscosity is added to the Bakken formation, it changes the drilling dynamics, Mr Hoover said. In some areas, oil-base mud is required where higher mud weights are necessary, but most of Brigham’s acreage is in normally pressured areas.
“The water drills like butter in the Bakken and Three Forks,” he said.
The rig and experienced drilling crews account for the faster drilling times as well. “Rigs are customized for the Williston Basin, and there are a few differentiators,” Mr Hoover noted. “One is an AC electric top drive drilling system, which is installed on virtually every Williston Basin newbuild rig.”
“New technologies and equipment on the rigs include BOP handling systems and automatic catwalks, which make these rigs more efficient,” Mr Hoover said. “There also are new drill bit technologies and directional drilling tool improvements.
“We’ve learned how to drill better, and that knowledge is combined with improved rig quality to contribute to fewer days drilling the well,” he added. “There also is a big push for safety, and some of the new technologies and equipment also increase safety on the rig.”
Nabors Drilling
Nabors Drilling is active in numerous shale plays around the US and says it holds the largest market share in the Bakken shale, for which the company’s B Series PACE rig is designed. The B Series is essentially a winterized iteration of its 1,500-hp rigs for shales and conventional fields in warmer climates.
“The B series rigs with walking capability are well-suited for simultaneous operations when development drilling begins,” said Ronnie Witherspoon, senior vice president and general manager, Nabors Drilling Northern Division. “The rig can clear existing wellheads, and its skidding capability is conducive to pad layouts.”
Most new B Series units are delivered with Columbia substructure moving systems. Additionally, the rigs can be fitted with a moving system later if they are not delivered so equipped. The rigs are also equipped with technologies from CanRig, a Nabors company, including an automated catwalk, Torq-Matic floor wrench, a top drive drilling system with Soft Torque software to mitigate stick-slip and downhole vibration, and Rockit, a surface rotary steerable system that rotates the drillstring in horizontal wells to reduce downhole friction.
- Nabors Rig 981, an SCR unit, is drilling a well for Shell in the Marcellus Shale. Ronnie Witherspoon, SVP and general manager for Nabors Drilling Northern Division, says the company is continuing efforts to enhance rigs, equipment and software for shale drilling. In plays such as the Marcellus, wells are often drilled in a manufacturing mode. Minimizing the number of days on a well and reducing costs are key considerations for operators, he said.
“All of our technology enhancements are geared toward optimizing drilling efficiencies while addressing the operator’s ultimate goal of minimizing the number of days on a well and shaving costs,” Mr Witherspoon said.
“When shale plays are in development, they will be in a manufacturing mode, so to speak, where well after well will be drilled from a multi-well pad,” he explained. “What we are trying to do with our rigs, equipment and software is to optimize the process and continue to drive down the number of days on a well.”
My Need The Job In Drilling Rig .
My Exsperiens In Drilling Rig 24 Year
Dear sir
There is a budget of $10million usd project to supply drilling pipes, Please can you work on this Government contract.
Your comment will be appreciate for business progressive.
Thanks
Mr. Paul