Tailored engineering, automation to drive optimized fracturing

Rush into manufacturing mode may be leading to less efficient frac designs, forfeiting valuable information, production in shales
By Katherine Scott, associate editor
Ronnie Witherspoon is executive vice president of Nabors Completion & Production Services.
What technological challenges do you see in the provision of completion and production services, and what equipment improvements will be needed in the future?
If you look at the estimated ultimate recovery using unconventional drilling and completion practices, the numbers are a stark contrast to what we see in conventional oil and gas production, where ultimate oil recovery may have exceeded 20% over the original oil in place, so there’s room for significant improvements in current completion technology.
The reserves being produced today are often more geophysically complex in nature and much harder to reach from a drilling perspective. These reserves often require advanced completion techniques in order to be economic.
These challenges are being met with new technologies and novel applications of existing technologies, as well as the careful application of best practices. The industry will certainly witness an increase in fracture network efficiencies in the reservoir contact area and the implementation of improved secondary recovery techniques.
As we continue to optimize the fracturing process, the industry will have to move toward greater automation. The drilling side of the industry has become largely an automated process. This development has substantially lowered manual labor requirements. However, the completion process, including hydraulic fracturing, continues to be highly labor-intensive. There is significant room for improvement in the automation of that facet of the business.
How should a well be designed for successful fracturing?
We’ve seen a complete rush into the shale plays, so the urgency to exploit the play to extract hydrocarbons in a rapid fashion has really put the industry into a manufacturing mode mindset. This practice has unfortunately marginalized the science needed to optimize each well utilizing a tailored engineering solution. It is critical to account for certain variables, such as closure stress, permeability and conductivity, and fluid efficiency in order to ensure that we are designing a fracturing recommendation that results not only in the highest recovery for the initial production but also in the optimal production decline over time for each well.
In many of these basins, operators are utilizing more wells per pad. Instead of one well, industry now sees anywhere from four to 20 wells per pad, and the geologies don’t vary a great deal so operators default into a manufacturing mode.
This shale concept of drilling multiple wells on a pad is somewhat new to the industry. You drill one well over and over, replicating that process. A cookie cutter approach is, however, not always the most optimal approach.
Has this manufacturing mode of drilling been beneficial for the industry?
It’s a double-edged sword. Operators can look at some simple injection tests that may have been performed in the past on certain fracturing treatments in order to gain valuable knowledge about the formation.
Indeed, it’s becoming common practice now for companies to utilize the relatively cost-effective procedure to gain information on initial wells.

Unfortunately, a lot of companies are sort of defaulting to this replication approach after the initial well design is implemented, which may or may not be a bad thing, but it’s ultimately a blind reliance on initial sampling. It can result in the forfeiture of valuable information about certain anomalies or complex faults or structures that persist in the underlying formation.
Do you believe industry needs to improve how they understand these reservoirs?
Over time, operators will realize quicker cash flows from producing wells in that replication mode, but that can lead to less efficient frac designs. For example, proppant selection is still critical for the longevity of the well and, as formations become deeper and more complex in structure, the overall natural stresses from the well production can lead to proppant embedment and crushing, so understanding the connectivity implemented by the initial fracturing treatment is important.
Ascertaining the closure stress present in an individual well is a prerequisite to an optimal proppant selection process and can help ensure that an operator’s investment can and will lead to maximum recovery over the lifespan of the well.
Fracturing operations require trucks to move materials to location. How is industry working to reduce road use during fracturing?
As an industry and definitely at Nabors, we’re focused on increasing driver training and education. In addition, we have raised the bar with regards to the selection and criteria that must be met by new drivers. Across the board, the industry is using more stringent hiring practices around driver selection. There is also heightened focus on increased control injury management for vehicle movements and monitoring between locations.
Another issue surrounding fracturing is water management. How does industry approach this task?
Water resource plays a critical role in our management strategy. The drilling of deep saltwater wells for hydraulic fracturing has become more common, but both saltwater and water reuse techniques require fluids design technology that is capable of resisting brines and other water mineral characteristics, so the oil and gas industry has focused its efforts on “green” chemical initiatives. More and more, industry has viewed water as a key resource central to the operation of the business.
The manner in which water is being obtained, managed, processed, stored and utilized as a critical asset is a high priority for our industry. Technology is playing a key role in the water management cycle for utilization, filter and reuse. Addressing this challenge requires an “all in” strategy, including the use of flowback and produced water in completion methods in large-scale drilling, as well as stewardship and the conservation of surface water. It will make the use of deep saltwater wells to source water for oil and gas operations increasingly more commonplace.
What specific technologies can you point to that are addressing this?
We’re looking at technologies for overcoming these obstacles with a focus on new completion fluid designs, with increased tolerance for brines and other minerals in the water while meeting the challenges and requirements of unconventional wells. Additionally, new technologies of filtration and purification continue to come into the marketplace, addressing the challenging water conditions encountered by the industry.
What do you see as some of the biggest challenges to hydraulic fracturing?
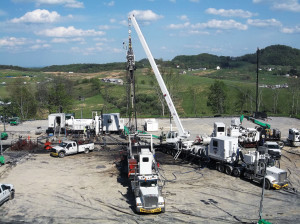
The market in the US is a bit challenged right now. We’re in an oversaturated state, so it sort of exacerbates the people situation when you want to continue to attract and retain the best people, but you have to find the fine balance in it. We’ve just undergone a transition from the more gassy areas to the liquid-rich areas, so we’re still balancing that out.
If you look at some of the commercial challenges, not only have we seen the frac capacity increase, but also we’ve seen a decrease in the demand side. Service intensity has also fallen, causing incremental reductions in demand based on redeployment of frac capacity to lower-intensity places, i.e., the oil and the liquid plays from the gas plays.
We’re starting to see a greater adoption of certain completion techniques that reduce time post-frac, which exacerbates this overcapacity situation. We’re working closely with clients to establish and reduce that time for fracturing, and the reduction of frac stages per well in the gas plays. All of that right now puts us in an unbalanced situation that over time will take care of itself.
How does Nabors address challenges on the regulatory front?
Both as a production and service company, we’ll have to continue to comply with a host of local, state and federal regulations in the US, as well as regulations from foreign governments, including taxes, financial reporting, air and water emissions, transportation, and product use and disposal. There exists an extensive procedural regime for applying and receiving key permits and licenses. There’s a lot of misinformation out there, and as an industry, we’re going to have to continue to work closely with the public and the regulatory authorities to ensure that the existing regulatory and permitting process and framework makes sense.
Do you see industry expanding its fracturing operations around the world?
Nabors doesn’t have stimulation operations outside of the US other than Canada right now, but we are looking to expand our footprint in the major shale basins around the world that have commercial productivity. Our drilling group has a sizeable footprint in the international markets, and we want to leverage that to establish a footprint on the stimulation side in key areas like Argentina, Colombia, Mexico, the Middle East and potentially China.
How has industry approached the fracturing issue in relation to its public image, and how should it be approached going forward?
We have to continue to educate the public. There’s a lot of misinformation about the industry that really stimulates an irrational fear about our business. The industry has to encourage public media-based educational programs. We have to continue to have town hall meetings that are informative and worthwhile at the local levels, but at the end of the day, the industry’s detractors will always seize upon the uncommon occurrences and make an improper characterization of the industry as a whole.
We’ve got to do a better job at combating some of the things that are improperly characterized and instruct the public about the significant technologies, safeguards and procedures that we’re all driven toward and that we’re committed to implement in order to ensure safe operations throughout the industry.
Nabors lives in the communities that it works in. Safety drives every aspect of our business, so the industry should not embrace more regulations just for the sake of more regulation, but what we should do is work in a collaborative effort with the public and regulators, and develop a regulatory framework that makes sense for the industry and for the public.
I think that our goals are far more aligned than what some of the industry detractors would have the public believe.
Do you think industry is doing enough to improve environmental performance so that is comparable to its safety initiatives?
We look at environmental performance as a key piece to our ongoing strategy to preserve and protect the well-being of our people and communities. It’ll continue to hold the same priority it does for us to protect and serve our people, so when I say safety, I talk about our environmental efforts as well. They go hand and hand