Stick-slip workshop highlights mitigation technologies, needs
No ‘silver bullet’ exists, but training, field experience may help stem vibration damage
By Keith Womer, KWTS; Dustin Torkay, Gino Villanueva, Seawell Americas; Thomas Geehan, M-I SWACO; Jan Brakel, Shell; Dimitrios Pirovolou, Schlumberger; David Reid, National Oilwell Varco; Mike Killalea, IADC

This article presents the results from a workshop on stick-slip mitigation held in Houston on 15 July 2010. Sponsored by the Future Technology Subcommittee of the IADC Advanced Rig Technology (ART) Committee, the event brought together technology leaders and engineers to discuss stick-slip mitigation.
Led by specialists with operating and technology companies, the goal was to educate the industry regarding existing technologies available to address this issue, as well as identify the need for possible future technologies. In addition to presenting the findings from the workshop, this article also aims to describe the event’s unique structure:
• Opening, non-commercial presentations wherein the science of stick-slip and the business case for its mitigation were reviewed;
• A series of short presentations by various providers with technologies to identify or mitigate stick-slip;
• A roundtable discussion involving both the presenters and the audience to assess the effectiveness of these technologies and areas where further technology, education or process improvement is needed.
This was all condensed into one afternoon. It was the first in a series of planned workshops to address technology needs that were identified in an industry survey conducted by the IADC ART Committee last year and reported in IADC/SPE 128953, presented at the 2010 IADC/SPE Drilling Conference in New Orleans.
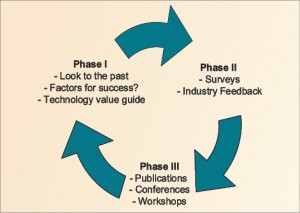
Background
The mission of the IADC Future Technology (FT) Subcommittee is to encourage technology commercialization and increase the industry’s technology adoption rate, focusing on high-need applications. This process consists of three phases (Figure 1):
• Phase 1 analyzes case studies of successful technologies, so-so technologies and unsuccessful technologies.
• Phase 2 conducts industry surveys regarding technology needs online and at industry conferences.
• Phase 3 actively addresses technology through publications and workshops targeted at specific high-need areas.
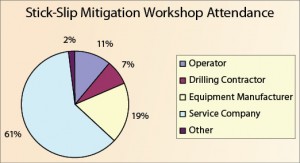
At the 2010 IADC/SPE Drilling Conference in New Orleans, the FT Subcommittee presented a paper that assessed examples of past, present and future technology commercialization and summarized results from its 2009 technology-needs survey. Results indicated that stick-slip mitigation technology was in high need, and the group decided that a half-day workshop would be the best format for bringing together leaders of different technologies to help educate the industry on available solutions.
Workshop Format
The afternoon format was a critical factor for the success of the workshop, and its popularity was largely unexpected. It appeared to have been popular primarily because most attendees would not have to miss an entire workday. Additionally, because the workshop was only four hours, content was condensed into a dense, high-value format with little overlap on topics or presentations.

Another somewhat unusual aspect of the conference was in its approach to commercialization. One of the sessions was devoted specifically to providing vendors of slip-stick mitigation technologies an opportunity to present a brief overview of their solutions. It was felt that this was an efficient means, both for the vendor and attendees, to present basic information regarding various technology offerings on the market. Commercialization beyond this narrow scope was not permitted.
The workshop consisted of the following sessions:
• What is stick-slip.
• The value of stick-slip mitigation explored with case studies.
• Technologies that address stick-slip mitigation.
• Roundtable discussion.
• Knowledgeable and well-rounded speaker representation with open discussion.
• Networking hour.

Background and prejudice of participants
There were a total of 106 attendees, most of whom were local to the Houston area. A survey was conducted at the end of the workshop, completed by 51% of attendees. The survey provided a good estimation of the demographic makeup of the participants and measured their opinions regarding the workshop format and technical content.
The survey revealed that 61% of participants were from service companies (Figure 2). Approximately 18% of participants were from drilling contractors and operators, and 90% of all participants found the workshop to be very/somewhat valuable.

The large representation of service companies could have biased results for some of the survey questions where participants were asked to evaluate what they think the most effective and cost-effective technologies presented were (Figures 8 and 9).
What is Stick-Slip?
This session was designed to be a tutorial regarding stick-slip, specifically what it is in the context of general drillstring vibration, how it is detected and typical techniques for mitigation.

One definition for stick-slip is that it “refers to the phenomenon of a spontaneous jerking motion that can occur while two objects are sliding over each other.” In the drilling industry, it is characterized by large cyclic variations of the drive torque and the rotational bit speed.
The technical discussion was presented by John Macpherson from Baker Hughes. He outlined the characteristic drilling responses that identify the condition, drill bit stalling and the significant variations in torque. A remedy to remove the effect is by decreasing the weight on bit and increasing rotational speed.
An example of the worst case was quoted as 24 seconds with no bit movement and 1.4 seconds of backward drill rotation. After nine hours, the tools were destroyed – illustrating that the subsequent effect of stick-slip on tools in the drillstring can be very severe.

Mr Macpherson also remarked that slip-stick vibration and lateral vibration are inversely coupled, meaning that often a decrease in stick-slip may result in an increase of equally harmful lateral vibration. Hence, “stick-slip mitigation” is actually a balancing act that involves trading off slip-stick and lateral vibration to establish an operating environment that minimizes both but perhaps not eliminating either.
The Value of Stick-Slip Mitigation Technologies
The second presentation, by Mark Dykstra of Shell, addressed the business value of mitigation of the stick-slip effect. Primarily, the justification was based on the cost-per-unit depth analysis. The related effect of wear on the dull tool was highlighted by the option of increased rotational speed.

The presentation went on to describe the auto-mitigation technique known as Soft Torque Rotary System (STRS). This works on the transfer function of speed and torque. An example of its use on an offshore well in Qatar was described. In that application, the use of the technique resulted in a 42% improvement in ROP. Shell has resumed active sponsorship of deploying the latest soft torque rotary system technologies – a sponsorship they pioneered in the 1990s.
Technologies Addressing Stick-Slip
The presentations in this session were from vendors of stick-slip detection, analysis and mitigation technologies. They ranged from basic monitoring to analysis services (frequently bundled as part of an overall vibration management service) to soft torque control systems.

In the first presentation, Ryan Weeden of NOV ReedHycalog discussed how the effect of stick-slip can be reduced by the correct design of the drill bit and bottomhole assembly. More drill bit contact area with the annulus wall can help to decrease torsional vibration and thus stick-slip. Additionally, the use of a stiff assembly will decrease the deflection of the string, causing natural frequency changes that can help to mitigate stick-slip.
In the second presentation, Svein Ove Aanesland from National Oilwell Varco described a soft torque control system that modulates the top drive drilling motor while using sensors to determine the rotational speed and torque and incorporating simulation software.
He also described the difference between AC and DC top drives and the internal damping from each. When comparing two nearly identical wells drilled in the same formation, the DC top drive outperformed the AC top drive in terms of higher ROP and reduced bit wear due to “droop” or more dampening inherent to DC motors.

In the third presentation, Scott Boone from Canrig Drilling Technology presented his company’s implementation of a soft torque control system. In general remarks, Mr Boone explained how the driller needs the correct suite of tools to reduce inefficiencies.
Improvement in tool performance comes from automation and optimization, resulting in greater safety and the reduction of flat time. All combine to reduce well costs. In the case of stick-slip, Mr Boone stated that between 20% and 70% improvement in ROP can be obtained with an automated soft torque system.
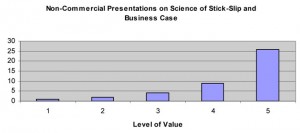
The last two presentations were delivered on the topic of vibration monitoring, by Riaz Israel from Schlumberger and Jorge Delgadilla from Geoservices. The use of both surface monitoring and downhole sensing were discussed. The use of high-frequency data acquisition was discussed, and it was stated that the measurements should be taken as close to the sources as possible to improve accuracy.
From the data acquisition, results need to be communicated and protocol procedures have to be implemented, with the supply of support and suggestions. These outputs are based on the analysis of the data acquired both surface and downhole.
Roundtable Discussion
The roundtable discussion included all speakers. Along with scripted questions, comments and questions were taken from the audience. The scripted questions were:

What level of expertise and training is required to run these systems?
It was noted that soft torque control system products featuring an on/off switch have an inherent simplicity: “Try it. If it seems to help, great. If not, switch it off, no harm done.” Nonetheless, it was acknowledged by all that such systems don’t address every situation; therefore training and services will still have to be given to rig personnel to recognize a situation, determine the root cause and identify and implement a solution.
Given the current solutions for stick-slip mitigation, what else should be done?
The following points were made by various panelists:
• Further gains could be made if companies work with each other and try to control both rotational speed and weight rather than each alone.
• Further coaching is needed regarding tool limitations to avoid unsafe tool use.
• The use of high-resolution data – as is available with wired pipe or in recording tools – was encouraged.
• A recognition of the interrelationship of torsional vibration and lateral vibration is important.
• There are other variables that were not fully covered in earlier discussions, such as well shape and hole size, that need more study.
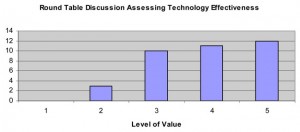
What improvements can enhance the systems shown today?
The following points were made by various panelists:
• With more runs in various drilling situations, more experience will be gained.
• The control systems still need checks so that wrong inputs can be regulated.
• The situation downhole is still a blind one. We can’t really see what is happening downhole. Anything to improve understanding will move the industry forward.
• Wired pipe and real-time data to reduce latency would be an immense help.
• Having vibration monitoring on different points in the drillstring would aid understanding of vibrations.

What level of detection and mitigation seems to be the most cost effective?
The moderator acknowledged this as the “unfair question,” which nonetheless is one that was on the minds of all of the attendees.
The following responses were made by various panelists:
• Regardless of other analysis and mitigation, bit optimization needs to take place.
• However, bit optimization is still limited by other components.
• “Cost effective” must be measured against acceptable risk: In most cases, the cost of having to fish or saving one trip can cover the cost of analysis services or one of the software torque control systems.
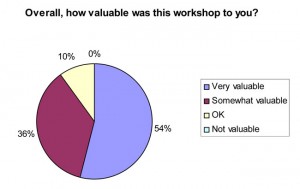
Where should the future of stick-slip mitigation be invested and directed?
Following were the recommendations of the panelists:
• Operator training and planning. For example, with a rotary table, everyone knows when stick-slip is happening because everybody can feel it. However, an AC top drive will power right through it, making detection difficult; therefore operator training is important.
• Broadening system application.
• Educating people on the benefits and problems of stick-slip.
• Improved planning.
• Use of real-time measurements, such as wired pipe, as a way to “close the loop” not just for stick-slip but all modes of vibration.
Comments taken from the audience included:
• Rig culture considerations, such as drilling parameters dictated by the company man, need to be considered. Sometimes when drillers notice a stick- slip condition, it is ignored, deviating from the dictated drilling parameters. Managing the decision-making process can help alleviate cultural problems.
• Control systems such as soft torque assume the driller has some autonomy and is proactive.
• There is no perfect solution.
• Proper well planning and design of bit, BHA, mud, ROP and WOB can solve many problems.
Conclusions
The overall conclusion from the workshop is that there is no single solution to stick-slip mitigation with current technologies. However, services and control systems can offer a cost-effective benefit in certain situations. Given that there is no “silver bullet” at this point, rig training is still required to recognize and mitigate stick-slip. More field experience in the use of soft torque systems will improve the effectiveness of the systems.
Additionally, the use of real-time downhole data is the frontier that could result in a step-change improvement in management of the multiple modes of drillstring vibration.
The Stick-Slip Mitigation Workshop was a success due to excellent speakers, engaged participants, a focused and compact agenda, and presentation and analysis of a variety of technologies that can help mitigate the costs of drillstring vibrations. 50% of attendees surveyed said the workshop was very valuable, 40% said it was somewhat valuable, and 10% said it was just OK.
Overall, these responses were positive, and the IADC Future Technology Subcommittee plans to host additional workshops for other high-needs areas.
This article is based on IADC/SPE 140044, “Results of July 15, 2010 IADC Stick-Slip Mitigation Workshop,” presented at the 2011 SPE/IADC Drilling Conference and Exhibition, 1-3 March, Amsterdam, The Netherlands.