Drilling mud solutions: Cracking the shale code
Highly customized fluids are helping operators to unlock resources, reduce costs in vastly different US plays
By Diane Langley, editorial coordinator

A trend afoot in the world of drilling fluids is further evidence of the importance of shale plays in North America today. Every shale play is not created equal; so it stands to reason that the ideal drilling mud solution needs to match the unique requirements of each play.
Operators in the US shale plays are getting some help from drilling fluid suppliers who are customizing fluids to prevent dreaded hydration of the shales while drilling and running casing, to withstand high borehole temperatures and to meet more stringent environmental requirements.
“Drilling operational strategies employed in various plays often drive formulation variations more than the typically less significant differences in shale characteristics,” David Breeden, supervisor analytical services for Newpark Drilling Fluids, said. “For example, varying casing programs often impact fluid formulation and strategies, and expose formations from the previous casing point down to the shale play for extended periods. Fluid formulation must be altered to enhance shale stability to address such instances.”
Service companies also are addressing the environmental issues associated with shale plays — the need to move away from oil-based mud (OBM) and to reduce the need for fluids and cuttings disposal. According to Quan Guo, manager of industry initiatives for M-I SWACO, the company has developed water-based muds (WBMs) and is working on completely biodegradable synthetic-based muds (SBMs). They’re also looking at mechanical-based inhibitors versus traditional chemical-based inhibitors in an effort to avoid or reduce disposal issues.
Traditional mud-shale interaction evaluation techniques for selecting drilling fluids do not apply to shale-gas wells. Gas shale is inhomogeneous, highly laminated and very brittle. M-I SWACO has developed new testing techniques specifically for gas shale. “These fluid-shale interaction tests have been demonstrated to be effective for fluids selection to minimize fracture development and delaminations, to evaluate water invasion into shale formation and its impact on shale strength,” Mr Guo said.
“Organic shale plays are very different from traditional highly reactive and swelling shales, and not all shale plays are the same. The reservoir temperature, pressure and local stress are quite different,” he said. For example, in the Eagle Ford shale in South Texas, the Wilcox and Midway are highly reactive and heaving formations.
“For this region, we have to design and select drilling fluids that can prevent shale instability in the surface and intermediate casing hole sections, and these fluids must be able to handle entirely different wellbore stability problems in the reservoir section,” Mr Guo said. “The shale instability problems in the reservoir section are related to interface instability, hole collapse and caving through delamination and micro losses through natural fractures and interfaces.”
Lubricity and hole-cleaning are key issues in long horizontal drilling. According to Mr Guo, the industry has not established effective lubricity testing techniques that are meaningful and reproducible or consistent with field experience. “We are tackling the lubricity issue through two areas: product development and testing methods development. The ultimate verification is hrough field performance,” he said.
There has been an increase in rate of penetration (ROP) in the field, perhaps due to better lubricity and hole-cleaning. “For example, for more than 100 wells of similar well depth and trajectory in the Haynesville, the wells drilled with one type of fluids of better lubricity and shale inhibition take fewer days than wells drilled with other types of fluids,” Mr Guo noted.
He cited another example in the Bakken field where the ROP or the total drilling days were improved 35% to 50% by optimizing hole-cleaning practices, without increasing the pumping rate or the solids control equipment.
Fayetteville Shale
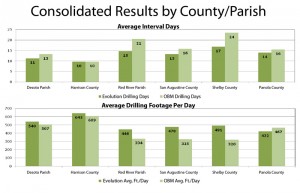
The Fayetteville Shale play, located on the Arkansas side of the Arkoma Basin, stretches from approximately Fort Smith east to beyond Little Rock and is about 50 miles from north to south. The play ranges in thickness from 50 ft to 550 ft and ranges in depth from 1,500 ft to 6,500 ft.
Operators looking for a substitute for the traditional OBM to drill in the Fayetteville discovered efficiencies from the use of an application-specific fluid after trying several WBM systems. “The WBMs that they tried had not been as efficient for them as the OBM,” Brady Fritz, global technical advisor for Halliburton’s Baroid business line, said. “They needed something that was a bit more high performance.”
One of the operators was experiencing high torque and drag, high low-gravity solids in the mud, overall wellbore instability and higher mud costs because of lower-than-expected performance from the WBM fluids. “All of these things represent nonproductive time (NPT),” Mr Fritz said. “Rig rates can be upwards of $50,000 per day, so when you’re down for hours, that gets to be very expensive. As a mud company, if we can come up with a fluid that not only keeps NPT down and allows the operator to finish their well a day or two earlier, that’s extremely beneficial.”
In the case of the Fayetteville play, the methods by which the shales are inhibited are extremely important. When an operator talked about having hole instability, the thought was that low water loss was needed to get through the overlying shales. “It came to my attention that this was not the factor by which the shales are inhibited,” Mr Fritz said. “It had very little to do with water loss and had more to do with the fact that the shales are naturally micro-fractured and we have to have a way to seal those shales to keep them from getting wet.”
When the shales in this particular area get wet, the illite (which is the mortar that holds the shale together) within them has a tendency to dissolve or crumble. When exposed to water, these shales delaminate severely, causing the hole to cave in. The fluid formulation that Halliburton developed for the Fayetteville play is a WBM potassium silicate-treated fluid. “It’s not the typical silicate fluid that we’re used to seeing from days of old,” Mr Fritz said. “It’s a silicate-treated fluid; that means there is a great deal less silicate in it so there are no issues with lubricity or slower drilling. The key to system performance is inhibition.”

The operator needed shale stability and lubricity that was inherent with an OBM but also wanted the cost savings and environmental benefits of WBM. The SHALEDRIL F fluid was field-trialed and was successful on all five wells. Not only did the formulation meet Arkansas environmental regulations, it also helped to reduce the operator’s liquid mud waste. Drilling rates were comparable to OBM, and overall well costs were reduced because the job was finished sooner than anticipated, according to Halliburton.
In Van Buren County, Ark., one well program called for air drilling down to about 3,500 ft (the top of the Morrowan Shale), setting surface pipe from around 600 ft to 1,000 ft, cutting the curve through the Morrowan Shale and drilling laterally into the Fayetteville Shale. The custom drilling fluid was introduced into the hole at 3,500 ft. “The fluid had to be very inhibitive because there was no time before building angle and cutting the curve,” Mr Fritz said. “At that point 1,500 ft to 10,000 ft of lateral may be drilled.”
“The fluid has been an absolute game-changer for operators in the Fayetteville,” he continued. “We’re able to drill the wells one, sometimes two to three days, faster than before and in areas where we have high loss of returns the WBM is much more cost-effective than the OBM.”
Approximately 60 jobs have been run for one operator; another operator in the play has run about 12 jobs using the fluid. On average, 30-80 ft/hr have been achieved when sliding and 100-300 ft/hr have been achieved while rotating. “To date, we’ve had no issues drilling or running casing. We’ve had minimal site remediation and other ancillary costs. We’ve had excellent wellbore integrity,” Mr Fritz said.
Success in using this fluid has spurred laboratory research and a desire for other fluids “Quite frankly this began an effort to customize each and every shale play,” Mr Fritz said. “Now that’s a lot of work of course and we’re working on devising systems for a number of plays. As a direct result of this effort, we came out with unique fluids for use in the Barnett and Haynesville.”
Haynesville Shale
A shale rock deposit located in Louisiana and East Texas, the Haynesville shale play also extends into Arkansas. Experts estimate that the play holds between 20-35 Tcf of gas. Natural gas production from the Haynesville occurs from rocks about two miles beneath northwestern Louisiana, southwestern Arkansas and eastern Texas. Two shale beds, the Haynesville and Bossier, are encountered while drilling Haynesville production intervals.
High bottomhole temperatures, troublesome formation contaminants, high pore pressure and wellbore lubricity challenge operators attempting to use water-based fluid formulations in the Haynesville play. According to Newpark’s Mr Breeden, operators had been presented with a hostile combination of conditions that limited the effectiveness of conventional WBMs, and OBM was the common choice for drilling horizontal production intervals in this play.

“Newpark is examining each shale play to individually formulate the fluid required to successfully drill specific shales,” he said. “We are also looking at well-to-well formulations in certain shale plays due to the variance in drilling operational strategies employed.”
A clay-free WBM, the Evolution drilling fluid system, was formulated for the Haynesville play and includes a synthetic viscosifier/suspension agent, a blend of environmentally sound lubricants and a low-end rheology modifier. Several system characteristics enhance fluid applicability to Haynesville shale use, including extreme thermal stability, resistance to H2S and CO2 contaminants and HPHT lubricating capabilities. In areas like the Haynesville where good mud lubricity can stretch the technical limit in the horizontal lateral length, the mud friction coefficient of 0.04 to 0.09 is extremely beneficial.
“This system provides ample inhibition to stabilize the Haynesville shale throughout drilling and casing operations. We conducted detailed shale characterization studies on the shale as a starting point in designing the WBM specifically for this use,” Mr Breeden said.
The new fluid formulation satisfies prevailing environmental requirements because no diesel oil or salt is used. In addition to promoting a clean wellsite, use of the system eliminates the requirement for transporting and disposing of whole mud and cuttings, and protects fragile wellsite ecology from potential damage, according to the company.
In cooperation with a major independent operator, Newpark conducted an initial field test, drilling horizontal production intervals on four wells in DeSoto and Caddo Parish. The fluid was built on location, eliminating most transportation costs and liabilities associated with OBM. The system is typically displaced into the well before drilling the intermediate casing shoe and is used throughout the build, turn and horizontal production interval to total depth.
In the initial trial, rate of penetration was seen to increase to the 90-120 ft/hr range, culminating in 1,003 ft being drilled in a 24-hr period. System performance improved and total fluid cost was reduced on subsequent wells in the four-well evaluation as lessons learned were applied.
The fluid system was then introduced in the higher-temperature environment of Red River Parish, where wells had bottomhole temperatures exceeding 350°F and hostile conditions that included elevated chloride levels. The custom fluid was used to drill one lateral interval of 6,100 ft in six days, a record for the operator. Both of these productions intervals in Red River Parish exceeded 5,000 ft.
This formulation has now been successfully used to drill and case dozens of Haynesville wells, meeting or exceeding OBM results in this play. “Having been used in more than 40 applications since its introduction, the fluid system easily ranks as the preferred WBM used in the Haynesville,” Mr Breeden said. “The wells have generally been drilled more efficiently, leading to substantial savings by the operator when the full well costs are analyzed, including costs of OBM cuttings.”
Eagle Ford Shale

Located in South Texas, the Eagle Ford Shale play produces from various depths between 4,000 ft and 12,000 ft and lies directly beneath the Austin Chalk shale. It is up to 250-ft thick in some places. Lateral sections are generally 3,000-9,000 ft but average 6,000-7,000 ft in length. Torque and drag, lubricity and wellbore stability are challenges associated with this play. Historically, OBM has been the fluid of choice in the Eagle Ford because it offers good inhibition and lubricity.
However, as is the case in some other shale basins, drivers behind the search for an effective WBM to replace the use of OBM are environmental constraints and economic issues. To answer operators’ requests for a WBM with the positive characteristics of an OBM, Baker Hughes recently introduced the Terra-Max system in the Eagle Ford.
An offshoot of the company’s Performax high-performance water-based fluid, which was developed for offshore use, the Terra-Max system is designed for onshore applications. “One problem with many of the WBMs is that they use some form of chloride to improve inhibition,” Tim Beyer, Houston sales manager for Baker Hughes Drilling Fluids, said. “In any kind of land-based situation, you have to stay away from chloride because either the cuttings can’t be land-farmed or an extra step needs to be taken to land-farm the cuttings.”
“When you look at land and, in particular, shale plays, one of the drivers is always going to be the environmental side,” he said. “So a fluid has to be designed around those constraints; this creates a challenge because typical WBM designs incorporate chloride materials and we have to go to some other form of chemistry to inhibit and control water activity in land applications.”
Baker Hughes describes its system as filling the technical gap between conventional WBMs and OBMs. It is customizable for various shale basins and for individual wells. It is designed around a proprietary sealing compound; when the compound contacts the connate water in the shales, the pH drops and a material is precipitated and deposited in the shale matrix.
“Most people don’t realize that shale is a porous material,” Mr Beyer said. “So if you can bridge those pore spaces, then you can prevent the transmission of pressure into the shale.”
Other system components include a product that creates a semi-permeable membrane at the near-wellbore and ROP enhancers. A deformable sealing polymer operates like a check valve, allowing one-way transmission of pressure. The ROP enhancers “oil-wet” the bit, drill string and other metal elements with environmentally friendly base fluids and surfactants, keeping clays from adhering to the bit and bottomhole assemblies. The other key element is a clay suppressor; an amphoteric material is used to coat cuttings so they don’t stick to each other or to metal.
“Not all shales are as reactive as others, so we may choose one, two or all four product components in a given area,” Mr Beyer said. “We design the system for each shale basin based on the geology and shale characteristics. But we use a combination derived from the same suite of products.”
Having been applied in approximately 300 wells in various shale plays, a custom Terra-Max system using all product components plus bridging agents has been used in nearly 20 Eagle Ford wells. The typical WBM mud program at Eagle Ford requires setting surface pipe with a basic spud mud down to around 4,000 ft, with the curve in the lateral being drilled in one section.
The kick-off into the lateral takes place at about 6,000 ft, and build rates are around 6°/100 ft. Total vertical depth ranges from 7,000-9,000 ft in the southern areas and 11,000 ft in the northern section.
In addition to addressing the operator’s waste management issues, use of the high-performance WBM achieved an average ROP of about 50 ft/hr, which was comparable to ROP rates using OBM, according to Baker Hughes.
Marcellus Shale
The Marcellus shale occurs beneath much of Ohio, West Virginia, Pennsylvania and New York, and small areas of Maryland, Kentucky, Tennessee and Virginia are underlain by this shale. The reservoir temperature is low at about 200°F, and the key concerns are wellbore stability and cost. Marcellus wells are highly deviated and composed of long shale sections. While optimum drillability required an invert emulsion drilling fluid, regulations discouraged the use of a conventional diesel-based oil mud. Operators called for WBMs that could drill the laterals, clean the hole and stabilize the wellbore at a low cost.
For this area, M-I SWACO developed a low-cost WBM formulation with good lubricity. Low Shear Rate Viscosity (LSRV) is provided by rheological modifiers, such as DUO-VIS xanthan gum biopolymer, while fluid loss is a combination of existing products, such as Poly Pac UL and the new Poroseal additive.
Marcellus wells drilled in southwestern Pennsylvania have kick-off points near 5,000-6,000 ft with total depths of 8,500 ft. In these laterals, the Poroseal additive enhances wellbore stabilization by sealing the microfractures of the rock. The polymer/Poroseal fluid system has shown high tolerance to contamination from the formations drilled and provided a fluid to a market where cost is an issue.
Although WBM are effective at getting the casing to bottom at a low cost, non-aqueous fluids (NAFs) inherently provide increased lubricity. For this reason, NAFs were brought back into the picture. The Megadril one-drum invert emulsion drilling fluid from M-I SWACO has experienced success in the major US shale plays.
When local regulators discouraged the use of diesel oil-based drilling fluids for horizontal wells, the company modified the Megadril oil-based drilling fluid, creating the Megadril P synthetic-based system with a one-drum emulsifier that met all environmental specifications. The system reduces the logistics and inventory on location by providing a one-drum emulsifying package that includes three one-drum emulsifiers – Megamul and One-Mul, both liquid emulsifiers, and Actimul RD, a dry emulsifier.
It has been employed in combination with the Virtual Hydraulics software package in more than 100 wells in the Marcellus, where days required to drill 10,000 ft were reduced to an average of 19.9 days from the 28.4 days recorded with the use of a WBM. The use of the fluid made the Marcellus the only US onshore drilling location to use a fully synthetic-based drilling fluid, according to M-I SWACO.
Lost circulation can be a drilling problem before entering many of the unconventional shale formations. M-I SWACO has developed a preventative strategy to combat the lost-circulation issues from the intermediate zones. After good drilling practices and the correct fluid is selected for the interval, the Integrated Borehole Strengthening Solution (I-BOSS) uses wellbore strengthening theory, enhanced software, loss prevention material treatments, environmental solutions equipment and engineering services to create an opportunity to drill intervals that previously were inaccessible.
“This is accomplished by strengthening the wellbore with various-sized loss prevention materials,” Shawn French, manager of business development for M-I SWACO, said. “Each wellbore and formation is different, and by using the Virtual Wellbore Strengthening module in the Virtual Hydraulics software, our engineers can tailor a loss prevention strategy to the needs according to the formation drilled and drilling parameters that need to be met.”
SHALEDRIL F is a registered trademark of Halliburton. Evolution is a registered trademark of Newpark Drilling Fluids. Performax and Terra-Max are registered trademarks of Baker Hughes. Poly Pac UL, Poroseal, One-Mul, Actimul RD, Megamul, DUO-VIS, Megadril P, I-BOSS, Virtual Wellbore Strengthening, and Virtual Hydraulics are registered trademarks of M-I SWACO.