Automation raises the bar in safety, efficiency
Contractors working to increase offline capabilities, prepare rigs for subsea completions and MPD, enhance training experience
By Joanne Liou, editorial coordinator
Claus V. Hemmingsen is CEO of Maersk Drilling and partner and member of the group executive board of A.P. Moller – Maersk. He also serves on the IADC Executive Committee and is a former IADC chairman (2009).
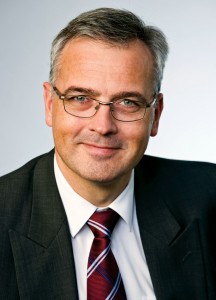
What are some of the most critical issues the industry faces in the coming year?
The industry has 146 newbuildings in the order book, and many of them are with improved technology. The need for competent people, well-trained people and people who can operate high-tech equipment is higher than it has ever been before. I think that’s our main challenge in the industry at large. That challenge of course goes directly to the competence.
We have to make investments in training, talent programs, development of competencies and so on. With the forecasted attrition, retirement and the new units coming out, it’s estimated that the industry will need about 20,000 new people, and they all have to have the required competencies.
The last time we saw a huge increase in activity was back in the ’80s. If you compare the current situation to those times, we had less requirements for our people then and took on crew with limited skills. A lot of these people came off to a rough start. Since then – and up until five years ago – I actually think the growth was very modest, and it was possible to cope with the growth just by having internal development programs and promotion programs.
What we are seeing in the last five years or so and in the coming three years is an explosive growth, and we have simply under-invested in education and training in the last 20 years.
What can we do to overcome the need for competent people?
You cannot undo what you have neglected to do in the past just overnight. There’s a backlog in what we need to do in terms of training and development. That means all of us in our individual companies have to put extra effort in both fast-tracking talent and making sure that we invest in training and developing people, enabling them to handle the new and more complex equipment and the more complex wells so we avoid at all costs coming into unsafe and critical situations.
Is the challenge a matter of finding the right people or putting them through the right training?
I’m an optimist, and I have the greatest respect for people of all nationalities, so I think the talented people are out there. It is more the fact that you cannot make them competent overnight. It takes time.
When I say competent, it is important to realize that competence entails three things: certified training, education and experience. In this industry, we cannot take people from the school bench, put them out there on the rigs and expect them to perform to the high levels that we demand today.
It is of course about the right training but it is also about making sure that we take the time to give people the necessary level of experience in order to reach a level of competence. I think too many people are focused on getting people the right certificates, thinking then they’re ready for the job. It’s the certificates combined with the relevant experience that makes people competent.
You need time on the rigs to gain the necessary experience, but you also need to spend a lot of hours training in a controlled virtual environment, very similar to what pilots do, so you are ready for all well control scenarios.
In Maersk Drilling, we are building a full-scale simulator with a three-dimensional dome. In terms of movement, visual impressions and sound, we can actually simulate all operations on each rig design we have in our fleet, and we can run that simulation together with training operations. It enables the crew to train specifically in the surroundings they find themselves in when going to the rig and gives a team-oriented training where different teams can train their mutual interactions.
This gives a far more realistic training experience, and we intend to try to use the simulator to fast-track the experience that people can gain.
The simulator will be located at the Maersk training center in Svendborg, Denmark. Our well control courses in that facility have been accredited by IADC since the late ’70s, and now we’re building a brand-new, state-of-the-art simulator.
We have a full-fledged anchor handler and supply vessel simulator in the same location, so we have many of the crews of both the supply vessels and the drilling rigs come through that facility every year. The new drilling simulator will be operating by June 2012.
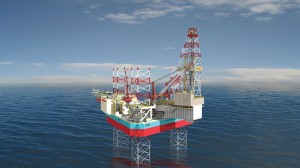
The industry has made great strides and progress in safety. How can we maintain that momentum with an influx of inexperienced personnel?
The same goes for safety as it does for equipment handling; it’s a combination of education, training and experience building. It’s also a matter of having mentors and people offshore that really take newcomers under their wings and help them get into the swing of things.
Safety is a mentality, and it’s not only work environment safety and people safety; it’s also process safety. We do see that the oil and gas industry is performing at a very high standard, both in people safety and process safety, and if we compare to other industries, these other industries are performing on an entirely lower level than what we are in the oil and gas industry. We really need to instill this safety mindset from the onset.
In safety terms, there’s no silver bullet. It’s hard work. It’s repetitive work. It’s continuous work, day in and day out. You have to keep working on that message, making sure you grow and motivate your people to think safety all the time.
Maersk has six newbuilds under construction. What challenges are you facing in rig safety and design? Are there safety elements going into the designs?
The construction is going according to plan. We are building two rigs in Singapore with Keppel FELS and four rigs in South Korea with Samsung. There is no doubt that these yards are busy, and you need to work very carefully with them to make sure that you get your building schedule maintained and all the technical specifications done.
In terms of upgrades of the newbuildings, in particular the two XL Enhanced jackups for Norway stand out. We’re building them based on the same design as the sister rigs; Mærsk Innovator and Mærsk Inspirer, which we call the XL rigs. They are the biggest jackups in the world and have proven to be very capable and efficient, and that’s all in observance of safety, capacity, drilling efficiencies and water depth.
Now with almost 10 years of operational experience on these rigs, we’re going to enhance the rig design even further. The new jackups will have superior capacities in terms of offline capabilities. They will have a very large hookload with an extreme XY cantilever outreach, and they will be prepared for subsea completions and managed pressure drilling (MPD).
On top of that, we have really gone out of our way to make sure all the areas that are normally exposed are even safer and more automated. We’re also doing a lot to make sure the crews are comfortable. On the jackups, we have 150 single-berth cabins. Everybody onboard will have their own cabin.
It’s quite extraordinary, and it is designed for Norway, which has very high demands for the work environment. We believe it will continue in that direction, so we started this one upfront to make sure we are on the forefront of development.
In that regard, we benefit from the close cooperation between the engineers at Maersk Drilling and the engineers at Maersk Line, the shipping side of the firm, where we can exchange ideas, especially when it comes to fuel optimization and power optimization. There’s a lot we can learn from each other.
Are all of Maersk’s newbuilds going to be equipped for MPD?
All six newbuildings under construction have been designed to accommodate the installation of third-party MPD equipment. We have witnessed an increasing interest in the capability of our units to be able to accommodate MPD equipment and, hence, took this into account during the design review for our current newbuilding program.
We do not yet see interest or demand reaching a level that would convince us to include MPD equipment as part of our standard build specification, particularly since there can be significant variance in our customer’s configuration and the equipment itself is in a state of evolution.

What results are you seeing with automation? Has it led to improvements in safety and efficiency?
Our initial focus in automation has been on safety, by eliminating the risk of personnel injuries and other accidents. Whenever people traditionally have been caught in the way of heavy machinery and handling heavy tubes, we try to automate these sequences so that we don’t have hands, feet and fingers in the way. That’s one thing we have achieved with automation.
We have also enhanced our efficiency with offline capabilities, so while we are doing one operation we can do something offline that prepares for the next sequence. This is one of the key factors that resulted in an improved efficiency of 20% when drilling the first well with the XL design.
Our expectation is that the XL Enhanced rigs will surpass that performance. We are now looking at what we think will be a bigger part of the future, namely the repetitive sequences where we aim to truly automate all of the repetitive work. For instance, on our deepwater rigs, we have a lot of the repetitive drilling sequences that are automated and the machine more or less runs on its own.
What challenges do you face in integrating new technologies?
I think it’s amazing and impressive what the industry has delivered over time to very complex challenges both offshore and onshore. The drilling industry has found solutions to those challenges, but that being said, there is still an opportunity to learn even more from other industries than what we have done so far. We’ve seen efficiency gains on drilling operations, but we have not really seen efficiency gains on the personnel side. That means that while we put more automated equipment out there, we’ve also had to put more people out there monitoring. There’s much more electronic equipment; more things need to be monitored all the time.
We need to further develop the consistency of drilling operations. Some challenges have been replaced by other challenges, but I think we’re moving in the right direction.
As the 2009 chairman of IADC, you noted two issues that you wanted to focus on, one being the public profile of the industry. The industry’s public image took a blow in 2010. How important is it for the industry to promote its image? What can the industry do to create a better image?
It’s an interesting situation because everybody in this world consumes fossil fuels. Everybody has a view on the effects of that, and very few have a view on what it actually takes to explore, find, produce and deliver oil and gas for people’s consumption. I think IADC, as well as oil companies, could do a lot to better portray the image of the industry.
I can’t find many industries that come close to how we operate. If you look at the modern rig, it is safe, it is clean, it does not require hard physical work with all the automated equipment, and it provides a good working environment. I think we have an excellent story to tell, not only to potential employees but also to the general public that this is not a dirty or dangerous industry entailing hard physical labor. This industry has an important purpose in providing energy to the world in a safe and environmentally responsible manner. That is what we need to communicate.
Of course, in the last two years, all the attention has been on the accident in the Gulf of Mexico and how to avoid accidents in the future. We have an opportunity to lead from there and say, “OK, there was that accident, and there are all these things that have been discovered and made contingencies for.” We need to make an effort to go out there and tell the public about all the things that were not wrong and all the brilliant technical solutions we have found, all the focus on safety, the relentless focus on avoiding spills and so on.
We need to turn it into something positive instead of constantly reacting to the negative or to criticism.
Maersk has had an environmental reporting system in place since 2007 to collect data on emissions and fuel consumption. What environmental targets has the company achieved in performance? What environmental goals do you have?
We are in the process of setting targets for our environmental performance for the coming years based on where we are now. It’s much more than just a target for emissions reductions. Of course that has to be part of it, but it also has to factor in the specific operations we are carrying out.
Today’s complex wells at deeper water depths cannot be compared directly with the environmental footprint from the operations we used to do. If you look at the machinery we put onboard and the specifications of the engines with the higher fuel efficiency, lower emissions and all the control and monitoring we do, we’re much better able to report on how we’re doing.
It’s also about how we control the chemicals we use. To reduce cost, complexity and risks we aim at two things: to reduce the variety of alternatives or substitute chemicals in our systems and to reduce the volume of hazardous chemicals onboard. This will reduce cost of administration, protection and management, risks related to storage, waste and handling and consequences from exposure to chemicals using it or spilling it. We plan to renew the ISO 14001 certificate and include the whole process, including chemical management, leakage management, waste management, etc.
One thing IADC has worked on since my chairmanship is the environmental performance indicator. It takes a long time and has been difficult to find common ground among contractors to find a good method of benchmark and how we can report together, like we do on safety.
Recently we have agreed that we will follow the IPIECA standard instead of creating our own, but I do think that drilling contractors have a task ahead of us in finding a more determined way to improve our environmental footprint, monitoring systems and benchmarking profiles to increase our individual performances.
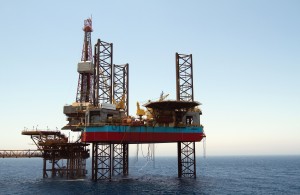
Is the industry as a whole doing enough to improve environmental performance to levels that are comparable to its safety initiatives?
If you go back and ask the guys who were here in the beginning of the ’80s when the safety focus started, that was also hard work and an uphill battle to get everybody to record and everybody to agree on which standards to be used. Environmental recording is much more complex, and that’s why it’s much more difficult to agree on what makes sense.
It is difficult – each well is different and so is the profile of the geology in which you’re drilling. One well can be easy; the one right next to it can be very complex and they can have huge differences in the environmental footprint. You cannot just do an emission per foot drilled. It’s much more complex, and I appreciate that, but I think we have the task ahead of us to find a way.
In October, Maersk signed a contract with BP for the Maersk Discoverer for work initially offshore Egypt. Do you think political implications are going to affect activity in that region? Do you see potential opportunities for more activity there in the next year?
There is a lot of tension in the countries affected by the Arab Spring, including Egypt, where we are also active through our joint venture Egyptian Drilling Company. We have been operating through the last year without any interruptions in Egypt and expect to continue to do so.
Will it be a big market for us in the future? From a Maersk Drilling perspective, it depends on the possibilities within the deepwater market that we intend to pursue. Our main markets for deepwater rigs remain the West African coast, the Brazilian area and the Gulf of Mexico. And we of course maintain our jackup focus on the North Sea market and Norway.
In 2012, do you plan to place more orders for rigs?
We have a clear ambition. We have 10 drilling barges in Venezuela and 16 large offshore rigs operating worldwide. We would like to increase those 16 to 30 by 2016. We have a plan to expand the fleet by 14 units in the next five years. Out of those 14, we have already placed orders for six. The timing of the ordering of the other eight units depends on market conditions, how we get the new equipment ready and that we see satisfying results. We will not order before we are satisfied with what we see in the existing newbuilding program.
We will take it one step at a time and make sure we don’t grow faster than we can ensure that we have competent people to run our equipment in a safe and efficient manner.
Dear Sir,
Good day to you
If it is possible, kindly requested to sent me a general arrangement drawing of a drilling barge(100*40*8 meter) which it will operate in shallow water.
Thank in advance
M. Tavakoli