Forging path forward for closed-loop drilling
Industry must support emerging technologies with standards, competent people
By Mike Killalea, editor
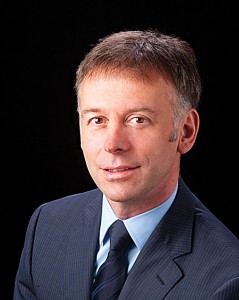
Nicholas Gee is senior vice president formation evaluation and well construction for Weatherford International.
Your career has given you really broad industry experience, including time with service, contract, drilling and operating companies, among others, and after all that I suspect you enjoy a rather rare perspective on the overall well construction industry. Given that background, what do you see as the most important issues facing us?
I think there are three key issues: safety, reliability and efficiency. With regards to safety, the industry has, over the years, improved its position in safety performance. If you compare our industry’s performance to those of other industries, we look very favorable. Yet we know that it’s not enough. From a drilling and well-construction perspective, the idea of a) continuous improvement and b) avoiding complacency are absolutely key. And I think there are a lot of things that play to that, including technology.
Our industry has experienced considerable improvements over the decades, especially in personal safety. However, some of the Macondo and Montara events have shown that, in many people’s opinion, we need to put more focus on process safety. Do you feel that service companies and service company technologies can help achieve improvements in process safety?
As service companies, it is incumbent upon us to do so. The reality is that, if I look from our vantage point as one of four multinational integrated service companies, the message to our organization is that operating at this level brings with it responsibility and ownership of some of that safety process. If you think about our scale, our scope and the technology we develop and deliver, our ability to impact the delivery of oil and gas is often on par with the operating companies, the NOCs and IOCs. But it’s often our personnel that are at the well site. We are part of the process, and we must participate in and take some role in the safety of that process.
The safety performance of the operator depends on them having the right level of engagement and the right relationship with their supplier, which should be one of a long-term objective driven nature, rather than solely short-term procurement driven.
For example, if we’re doing a total depth solution in terms of deploying a long extended-reach casing string, helping an operator drill a long section in difficult conditions and then deploy a casing string and get it cemented, we provide managed pressured drilling, top drive systems, cementing systems and isolation systems to assist with good cement jobs. Add to that some engineering planning at the well site and we’ve got as many as four or five simultaneous operations all going on at once. The responsibility is on us to integrate these activities, not only to provide an excellent piece of service and a successful job for the client but success in terms of knowing the jobs were completed safely.
The importance of successfully managing the entire interface brings me to another issue, a concluding issue around safety – investing in people. As an industry, the need to attract, train and develop people and in the context of process safety has never been so pivotal.
I’d like to turn to some of the specific solutions that Weatherford has engineered. For example, one influential operator recently commented that closed-loop systems represented the future normal for deepwater drilling. This is an area that Weatherford is focused on, and in 2011 Weatherford won an OTC Spotlight award for closed-loop technology.
What is the value added by and significance for deepwater of closed-loop drilling systems?
The development and deployment of closed-loop technology speaks directly toward improving reliability. I think that logic will dictate that it’s easier to understand what’s going on in a closed-loop system than it is in an open-loop system. Once you accept that, you can detect and understand what is happening deep down in the formation through which you’re drilling. And the issue with deepwater is not really that different than anywhere else, other than you’re dealing with necessarily long holes, in which the response times are longer because of the depth of the water. As a result, you want to understand more and understand better what is going on over those long distances.
Technologies traditionally used onshore are starting to be deployed in subsea environments. However, as an industry, we’re just starting out. Currently, we’re the only company to have done MPD using a subsea rotating control device. It’s certainly something that is clearly capturing the attention of the industry, both at the operator level and at the rig contractor level.
I am absolutely clear on the benefits for the industry as a whole using this approach, and I am absolutely clear that there are some technological challenges to making that happen in subsea. We’re at the forefront of addressing those with our subsea rotating control devices.
As you say, managed pressure operations have grown significantly in importance in the last decade or so. We at IADC have been very engaged in developing guidelines for MPD and underbalance, and Weatherford as you say is a market leader, most recently by installing the first rotating control device on a dynamically positioned drillship. What are some of the challenges you alluded to for MPD?
There are really three primary areas to consider. The first is process, which is where we are starting today. Whose processes are we going to follow? At the outset, we come to the client today with our way of doing it. I generally find that, as technology is adopted, clients want to develop their own particular way of doing things. But there’s a delay issue there about whose way of doing things is the right way and, over time, these become the industry standards. Then there are equipment standards. When you’re the first and it’s only just been done, then de facto you are the standard.
However, as you are building a business, you are investing in technology so that you can make the first move and gain the advantage of setting the standards. As uptake occurs, the standards begin to move away from where you are. I think it’s important that if we really do believe closed-loop drilling is going to be a widespread engagement, people should contribute to what they feel the industry should be doing in this area so that we clear the path ahead for achieving that.
We are delighted to be forging the path ahead and of course we’ll be delighted to participate in that journey. The first step in that journey is another key industry theme – people. The technology continues to develop from the engineering of the control head to the sophistication of the software. To be able to analyze what is happening downhole and help aid fast decision-making requires people on site who understand what that analysis means.
It’s complex data and complex information, and it isn’t just an answers-based product, much as we’re tempted to simplify the process. All of these require interpretation.
You need people on board the rig who are capable of understanding what’s in front of them when decisions need to be made. From our perspective, you have to address everything about access to and training of skilled individuals to be able to undertake this kind of work and who can communicate to the decision-makers on the rigs what something means and how to deal with the information that is being put in front of them.
I’m not just talking about catastrophic situations, rather about being able to make drilling decisions in real time, whether it’s controlling influxes or being able to navigate properly through narrow pressure windows to make sure that we get to TD on cost and on time.
As you alluded to, there are adoption issues in our industry. It’s kind of a “no one wants to go first” industry, so new advances are often viewed rather skeptically. With MPD, a lot of misconceptions have existed through the years, in fact, with regards especially to safety and well control that MPD is less safe than conventional methods.
I think it’s been demonstrated that that’s not really the case, but do misconceptions still exist among operators, and if so what would you say they are and how can they be dispelled?
I haven’t had any personal experience with those misconceptions in recent times. I think the use of the word “underbalanced” probably drove that to an extent, and managed pressure drilling is, as you know, not underbalance. I think the generic term for closed-loop drilling is an interesting one. It’s helpful because, not only does it get away from the idea of underbalance but it encompasses the entire universe of requirements to successfully mitigate hazards associated with the drilling process, which is what it’s all about.
It’s about people. It’s about the skills of those people and the decision-making derived from that understanding. It’s about hardware and software and pulling the system together. Closed-loop drilling encompasses all of those things. I think we’re beginning to see people understand and know more about that so there is less skepticism.
I think where you’ve got pockets of ignorance then you’re going to find concern. A lot of misconceptions were derived out of the early days of underbalance, and I think that’s what has driven concern. Today, we have IADC standards, so closed-loop drilling is becoming more mainstream.
The term close-loop is certainly more descriptive and really more informational than the other terms. Looking now at the land side, our industry recently has undergone a sort of “back to the future” phenomenon. We’ve reversed our historic trend away from onshore activities and are moving into ever deeper water depths. Of course offshore is still very important, but land well construction, driven mostly by unconventionals, has reached very astonishing levels. What challenges does the service industry face in facilitating this new drive?
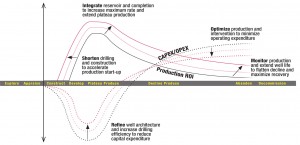
That’s an interesting one. Honestly, I’m not sure that talking about critical issues or key issues to the industry suggests any changes related to an increase in land work. Given the landscape in the United States, the response of the industry has been both remarkable but consistent with all other previous responses within the industry as our opportunities change.
It’s remarkable the flexibility and responsiveness of the industry, on both sides, operators and service, to be able to say, “Here’s an opportunity, I’m going to chase it,” and for the service sector to get behind supporting it. To what extent does it bring anything new to us? Whether we’re going to fly our products and services to the most remote jungle in Asia or whether it’s being able to successfully deploy large quantities of people and equipment in the new areas of the United States to exploit shale. It’s simply what we do.
I would consider that business as usual. The interesting thing for me, if you want to make a parallel between deepwater, high-pressure, high-temperature and what is going on today in onshore shales, is to further drive home the message of consistency, or similar issues relating to all wells, is wellbore integrity. If we think about what we’re learning and what we’ve yet to learn about Macondo, that’s a wellbore integrity issue.
Thinking about your point on land, then I think about the issues we’re facing about public concerns related to the water table. What we’re looking at there is the need to be able to demonstrate to ourselves, to the industry, to the public and to government that we’re successfully able to drill wells and provide isolation – so also wellbore integrity.
It doesn’t really matter whether we want to prevent massive spills at sea or whether we want to prevent gas getting into the water table, we need to be able to show that we can manage the process to achieve that integrity. Doing so goes to the heart of the real fundamentals of what we do. How we run strings and cement wells, this also needs to be “business as usual.” We need to show that we can do that successfully as an industry. It doesn’t matter whether it’s deepwater or high pressure or temperature or a land shale well.
You’re starting to see the industry itself asking questions: Can I adequately cement this well? Do I know how to do that? Have I got the right technology and have I got the right skills? Do I have the right skills then as an operator? Do I have the right skills as a service company, or the skills, processes, procedures, design? We’re seeing our customers asking themselves those questions, and for us it poses questions also. What new technologies can we bring to ensure adequate wellbore cleaning, good circulation of cement, good long-term cement jobs.
This is a key issue for the industry. It’s prescient, and it’s happening today on land wells and offshore wells.
Directional drilling advances were clearly enabling technologies for a lot of these shale developments, but operators continue to seek out lower-cost solutions. Can the service sector continue to lower costs on complex systems like rotary steerables or downhole motors or do we reach a plateau?
There are two issues, and the top one is value. The simple answer to your question is, yes, they can. That’s what we’ve always done. I think that the specifications associated with that, for example the spending, depends on the complexity of the wellbore you want to drill.
We’re making some real advances with our low-cost rotary steerable system, which has undergone some tens of runs to demonstrate its capabilities in the US shale plays to provide a lower-cost rotary steerable system. I think it’s also just an example of industry demand and service sector following. As long as there is demand for these things, technological innovation provides that and fulfills it.
My point about value especially applies at this early stage, and I can certainly see shale plays being at the relatively early stage of development. The question is, are we drilling for value? It’s not about coming to me and saying that I want to drill an x-thousand foot lateral and I want to halve the cost of it, so I need you to lower your rotary steerables cost. The question is, am I drilling the right well?
As an industry we are moving toward the value question, so I don’t see people coming to us only concerned about getting technology that’s going to halve the cost of the rotary steerable. I see people thinking, what’s the well I have to drill and complete to maximize the value?
These early days in shale we have lots to learn. You know we’re drilling long, long laterals, and we’re not really evaluating them. If we are evaluating, we’re not at a stage where we understand enough about the evaluation that we’re making to understand what’s productive and what’s not within those shales.
Where should I be targeting my completion? Where should I be targeting and pointing my well? I think there’s probably a lot of money to be saved to produce the same amount of oil or gas by putting my well in the right place and stimulating and completing in the right place.
Another way of saying it is, I’m spending a lot of money today that I don’t need to for the production I’m getting. A richer understanding of the shale reservoirs will allow me to get a richer understanding of how I can drill and complete wells and how I can save money on them on a dollar per barrel or mcf basis.
I think the corollary of your point is that new basins and new opportunities like this drive technological innovation, not only in the service sectors’ equipment – although clearly we’re able to respond to that and do so because of the economic opportunity – but it’s also in the reservoir and drilling engineering domain.
And it’s in the operator domain. Increasingly, for a big, integrated service company like ours, the relationship between operator and service company is a much more collaborative scenario.
Look at the stimulation and fracking that’s going on today. It’s a customer demand with a service company following, and the two things together have demonstrated the viability of a new resource. I think from the service sector it is both things. We can innovate, yes, at the individual technology level, but we can also help innovate at the reservoir and development level.
On the downhole measurement side, wired pipe telemetries are receiving increasing use, I guess it’s fair to say. Do you see over time that this technology will eclipse or even displace conventional mud pulse measurements?
If you’ve got very, very high data requirements, then you’re probably going to go to wired pipe. I don’t hear people complaining today that mud pulse doesn’t give them enough data. As you get into downhole seismic, you’ve got an awful lot of bandwidth that you need to get up the hole. Therefore, that’s what is going to drive you to wired pipe.
Wired-pipe telemetry has its applications, but I don’t think it will replace mud-pulse technology, which is well-proven and reliable. Against that, wired pipe is more expensive and must inevitably have associated reliability issues. That’s not to say I have any knowledge of it being unreliable, but if I were a well engineer I would trade off the benefits against the risks. Intuitively that tells me it’s not going to replace mud pulse.
It’s probably going to play a part in the future of the industry and, as you want to gather more information with higher bandwidth requirements, then you’re going to increasingly consider that. It’s always dangerous to get one’s crystal ball out, but I don’t think wired pipe is going to be a complete replacement for mud pulse.
Speaking of crystal balls, a lot of people are looking into theirs and seeing that rigs are going to be very highly automated at some point in the future. As long as you don’t say when then you’re reasonably assured that you’re right.
But in Weatherford’s case, you could say running casing on a rig has never been a particularly glamorous occupation, but as part of this increase in mechanization and automation, Weatherford recently introduced the Overdrive casing running and drilling system. What’s been the impact of that highly mechanized system? Do you think it’s going to revolutionize the kind of otherwise mundane casing-running operations and maybe supplant traditional solutions?
It’s interesting, isn’t it? Running casing is always mundane until you pressure test that string and you have a leak, at which point your $500,000 a day rig is now costing you money without making any progress. I would first reject the notion that running casing is mundane. I would say that even within my career I have seen a shift from making up chrome tubulars with rig tongs to treating it with kid gloves and developing specific chrome-handling capability and casing running.
It progressed from one to another, and I think our Overdrive casing-running and drilling system is a big step in that progression. But I don’t see it as a replacement.
Back to my point about integrity, I think if you ask any petroleum or drilling engineer, he would tell you that if we haven’t made that casing string properly in that shale well in the Marcellus, then we don’t have integral string; therefore we need to be doing something about it.
The Overdrive system has some additional benefits – efficiency as well as effectiveness – with the ultimate benefit of getting people off the drill floor and out of dangerous environments. That’s good for safety of people and that’s good for business.
Is there anything else that you’d like to add that you consider critical in our business now and in the near future?
I think thematically I started with safety, reliability and cost effectiveness. At the end of the day, it’s all about the service sector developing technology to drive down the cost curve.
If we consider the challenges of meeting growing demand in oil and gas from a declining base, an increasingly difficult set of reserves that are older with lower pressures, or from new reserves that are more difficult to access, then the cost base goes up. It’s incumbent upon us to be able keep the cost curve low enough so that we don’t impact the demand curve. And technology plays a big part in that.
My general point is that technology for productivity is a key role of the service sector. We’ve got a big role to play in safety, we’ve got a big role to play in reliability and cost effectiveness or driving down the cost curve.
A lot of that has to do with technology development and importantly, successful and reliable technology application in the field